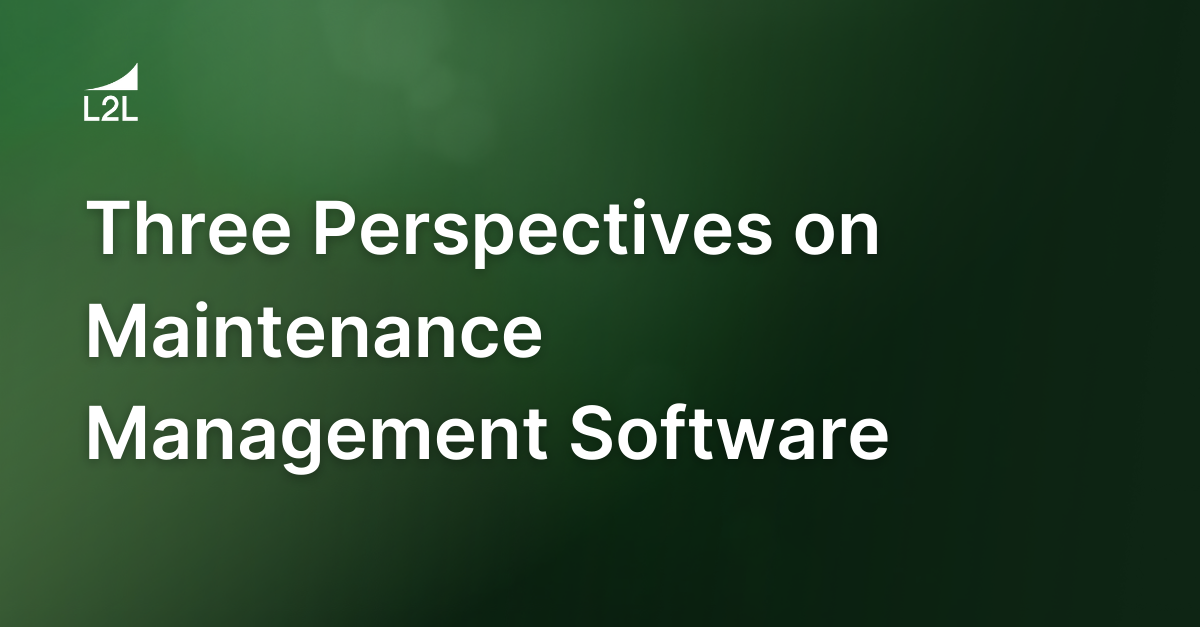
Estimated read time: 10 minutes
Have you ever heard a word repeated so many times that it starts to lose all meaning? That’s called semantic satiation, and it’s a good way to describe what happens when you spend a lot of time researching manufacturing solutions like maintenance management software.
The truth is that you’re probably too close to the topic. You’ve spent so long inspecting every tree that you’re no longer able to see the forest, and that means you’re not getting a full understanding of how a maintenance management solution supports your maintenance team, protects your equipment and benefits your whole plant.
You need a fresh perspective on the whole solution. Lucky for you, we’ve got three of them to share today — so sit back, relax and enjoy a fresh look at maintenance software.
Maintenance management software, defined
Before we get into the details of each perspective on maintenance management software, let’s make sure we’re all looking at the same thing.
“Maintenance management software” is actually an umbrella term covering two things:
-
Computerized maintenance management software (CMMS): If you’re using CMMS, you’re getting data about equipment performance, work orders and other key elements of your maintenance program. It’s technically a form of asset management, but it’s heavily rooted in the physical elements of maintenance work.
-
Enterprise asset management (EAM): As the name suggests, EAM solutions take asset management to the enterprise level by gathering more data about your equipment. They create richer context by providing insights, asset performance analytics and more, giving you a more complete picture of necessary maintenance care.
Still with me? Good — this is about to get a little more complicated.
While a computerized maintenance management system and some form of enterprise asset management are each important in their own right, their usefulness is entirely dependent on how you do them. There are three basic approaches to maintenance management overall:
Manual methods
If you need a pen and paper — or, worse, a spreadsheet — to answer basic asset management questions or perform a single maintenance task, you know you’re stuck in the rut of manual methods. They may have been functional in the past, but not anymore. These days, they're not just eating away at asset maintenance efficiency, facility management simplicity and even your ability to keep up with regulatory compliance; they're increasing asset downtime and maintenance costs at the same time.
It’s time to say goodbye.
For many manufacturers, that usually means progressing to traditional CMMS and EAM.
Traditional CMMS and EAM
Although they’re far more efficient than their manual siblings, traditional CMMS and EAM approaches still leave much to be desired. They may be disjointed, difficult to integrate or incapable of gathering all the asset performance and maintenance schedule information you need to automatically create work orders. They get the job done, but not as effectively as possible.
Modern maintenance management software solutions
The best way to handle maintenance management is through a cutting-edge, user-friendly software platform. This approach puts the maintenance team’s thumb on the pulse of the entire plant. It integrates data from a variety of sources, helps leverage insights from maintenance care needs and gives you the power to take control of asset management — all from a single platform.
Better yet, this approach allows you to utilize both preventive maintenance and predictive maintenance when pragmatic. What’s the difference? Well, preventive maintenance relies on usage- or time-based triggers to create a work order; meanwhile, predictive maintenance uses software and sensor-generated data to identify issues and predict the best maintenance operation. These both exist in contrast to reactive maintenance, which can increase maintenance costs by forcing you into a break/fix pattern.
Long story short, “maintenance management software” means both CMMS and EAM. What it does not mean is paper, pens, whiteboards and spreadsheets. For the purposes of today’s blog, it also doesn’t refer to traditional CMMS and EAM, which both stand to be improved by the advanced tools and smarter techniques integrated into modern maintenance management software.
Maintenance management on the factory floor
Now that we know what we’re talking about, let’s look at maintenance management software from the first of three unique perspectives: Your maintenance team’s.
Just about everyone on the factory floor is likely to say maintenance software benefits them somehow. However, the truth is that the people actually responsible for maintenance care probably see the biggest and most important advantages. Let’s take a closer look:
Easier data management
Modern maintenance work is all about data. With an outdated approach, that data is difficult to capture. Even if your maintenance team does get the info they need, it’s likely to end up siloed in a variety of disjointed systems — which means they’ll still need to manually stitch together the different sources to get something even resembling a clear view.
That’s why maintenance management software is such a big deal.
Instead of layering new technology on top of fundamentally flawed approaches, maintenance management software reinvents the data capture, display and utilization process. Using wearable technology and mobile devices, workers can create and capture information as they work. This data is displayed side-by-side with asset performance metrics and other key equipment information, creating a single view your maintenance team can use to create and act on each work order.
Simpler, clearer tasks
With all that data right at their fingertips, your team will always know exactly what to do and when to do it. Of course, that’s not just because they’re hardworking geniuses (although they probably are). It’s because maintenance management software enables preventive and predictive maintenance measures, giving workers the insights they need to structure and perform simpler, clearer tasks. The software can also provide key maintenance history, including a view of every previous maintenance request, to eliminate redundancy.
Reduced downtime
When your maintenance schedule or asset management practices are messy, a few different things can happen:
-
You could perform unnecessary maintenance work, which leads to downtime.
-
You could miss the signs that maintenance is necessary and experience an equipment breakdown, which leads to downtime.
-
You could rely on the wrong asset performance metrics and end up with a maintenance program that addresses symptoms instead of problem sources, which — you guessed it — leads to downtime.
No matter its cause, downtime puts pressure on the entire manufacturing workflow. However, the maintenance team experiences this pressure most intensely because they’re the ones who have to fix it. The good news is that maintenance management software helps plan and direct maintenance work, resulting in less downtime and clearer action plans when something does go wrong.
What maintenance management means for your equipment
It’s clear that maintenance management software is good news for your workers. But asset management isn’t really about people — it’s about equipment! (That’s how your equipment would see it, anyway.)
Sure, your equipment may not have a mind of its own — but because these machines are an important part of your manufacturing workflow, it’s helpful to view maintenance management software from their admittedly fictional perspective.
Here are a few things your equipment would appreciate — if it could tell you — about maintenance management software:
Fewer breakdowns
Imagine you’re a machine whose only job is to help keep production on track. Naturally, breaking down would be the ultimate embarrassment.
With maintenance management software, it’s easier for employees to gather asset performance data and turn it into actionable insights. That means they always have the information they need to make fast, accurate decisions about necessary maintenance work. As a result, many breakdowns can be avoided, and those that can’t are handled more efficiently — all of which is good news for your equipment.
Better, more timely maintenance
In some cases, poorly timed maintenance is just as bad as no maintenance at all. Incorrect or improperly performed maintenance is even worse.
Luckily for your machines, maintenance management software helps workers understand what’s required as well as when and how to do it. Built-in monitoring features can flag when a task isn’t performed correctly and which steps should be taken to solve the problem. Better yet, maintenance management software includes the ability to track the results of maintenance work — so if a new best practice is discovered, it can be replicated across the entire asset management program.
Longer lifespan
Although maintenance management increases productivity, reduces costs and otherwise supports manufacturing workflows, one of its most important tasks — at least from your equipment’s perspective — is increasing asset lifespan. When every element of your maintenance operation is moving smoothly, machines experience fewer damaging incidents and last longer overall.
That’s good news for you, too. Longer equipment lifespan means less money spent on repairs and replacements, simpler asset management, clearer spare parts management and more. Plus, you won’t have to pay for new machines quite as often (or navigate the downtime created by removing old equipment and installing the new model).
Does everyone love maintenance management software?
By now, you’re probably pretty confident that your whole plant will fall in love with maintenance management software. After all, it simplifies life in ways everyone can enjoy — humans and machines alike. So is there any part of your manufacturing workflow that doesn’t benefit from a better maintenance program, simpler work order management, improved asset performance and streamlined data capture?
As a matter of fact, there is.
Think about it this way: Your old processes — whether it’s an outdated computerized maintenance management system, a spreadsheet or even a pen and paper — probably aren’t happy about the change. After all, nobody likes being replaced.
If they hadn’t been dragging you down all this time, you might even feel bad for them.
Here are just a few ways modern maintenance management software improves on outdated approaches:
-
Speed: Old or disjointed systems tend to add unnecessary delays to your maintenance schedule. That’s not to mention the time it takes to maintain the systems themselves. With maintenance management software, you can count on quick data capture, work order creation, asset performance monitoring and more.
-
Accuracy: If you’re still collecting data with a whiteboard or other manual process, you probably aren’t getting the truth. Even a computerized maintenance management system that doesn’t integrate with other tech solutions will eventually lead to data silos and inaccuracies. Luckily, modern maintenance management happens in a single, easy-to-use platform that helps eliminate human error across the board.
-
Efficiency: Technology is no replacement for the creativity and flexibility of human workers, but that doesn’t mean they can’t work together. In fact, maintenance management software is the perfect opportunity for people and tech to boost efficiency in ways neither could accomplish alone.
-
Flexibility: Outdated approaches don’t leave much room for updates or new discoveries. They trap you in a pattern of layering new devices on top of old foundations, which ends up being a tech-for-tech’s-sake approach. Instead, maintenance management software reinvents your maintenance program from the ground up, allowing you to build flexibility, adaptability and other digital-first benefits right into your DNA.
-
Digital transformation: At the end of the day, stagnant, outdated processes are the anchor keeping you from exploring the wide-open ocean of digital transformation. Although asset and maintenance management are certainly not the only manufacturing processes that deserve digitization, they’re a good first step into the world of tomorrow.
Put simply, the old ways have been keeping you from all the things your plant is capable of. Modern solutions, tools and software can help you make a difference — but only if you have the courage to say goodbye to the approaches that are slowing you down.
Take maintenance management to the next level with L2L
Manufacturing wisdom comes in all shapes and sizes, but when it comes to maintenance management, our advice is always the same: Out with the old and in with the smart.
That’s right: Solutions like maintenance management software aren’t about throwing technology at all your problems. They’re about wisely and pragmatically leveraging available tech to make real differences in your factory. That means you have to know which problems to focus on and how best to solve them — and to do that, you need an all-inclusive platform.
That’s where we come in.
Our manufacturing software helps you work smarter, giving you the power to take control of your maintenance and asset management, support your employees and even save money along the way. To see for yourself, request a demo today.
Your maintenance team and equipment will thank you (even if your outdated approaches aren’t crazy about the upgrade).
Revisions
Original version: 18 July 2024
Written by: Evelyn DuJack
Reviewed by: Daan Assen
Please read our editorial process for more information
Related Posts
Subscribe to Our Blog
We won't spam you, we promise. Only informative stuff about manufacturing, that's all.