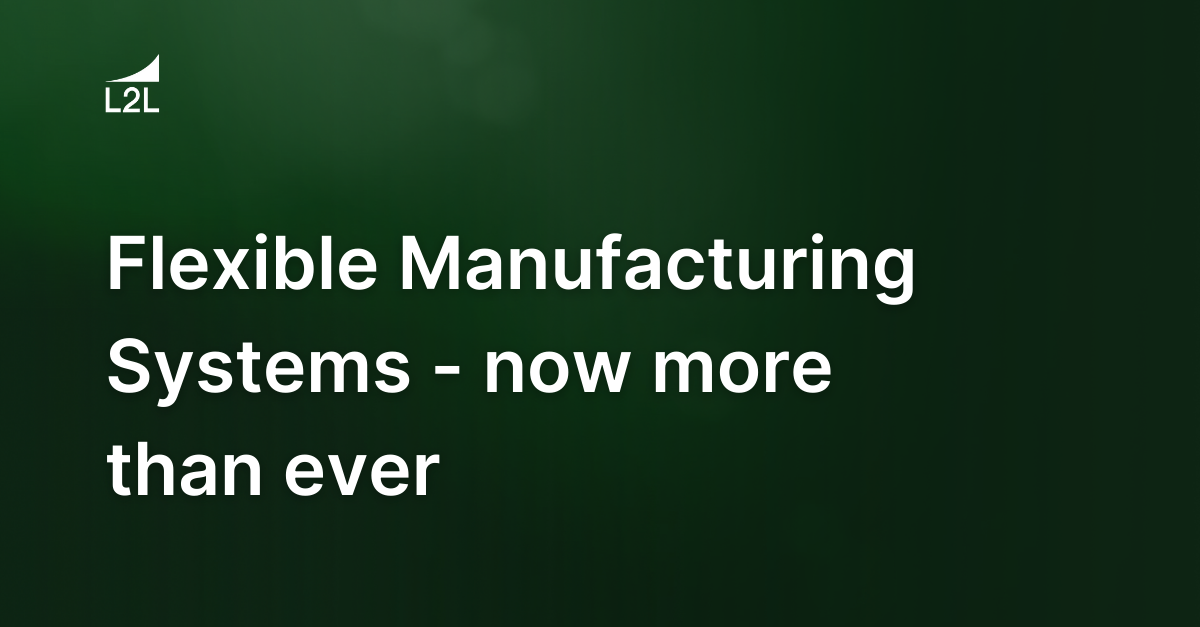
A Bit of History
Customer need is perhaps the single greatest driving force that compels shifts in business strategy. Historically, businesses have competed with one another by focusing on key customer needs, or production factors, such as cost, quality, service, or delivery. Increasing globalization in the 20th century, though, enabled manufacturers to reach many more market segments. The diversity in customer markets created a need for suppliers to provide customization, as each unique consumer base had variations in the exact requirements for products.
To be able to service these disparate needs, business operations had to become more flexible to satisfy varying product requirements. This ability has since become another core competency for businesses to leverage competitively. The abilities to:
- Make a variety of products with the same machines
- Produce the same products from different machines
- Create new products on existing machines
- For existing equipment to handle changes in product design
Never before in the history of manufacturing have so many disparate elements existed simultaneously. The unique challenges presented in 2020 have mandated flexibility, change, and adaptation.
Flexible Manufacturing System: Two Definitions
The inclusion of flexibility as a competitive priority meant firms needed the means to improve their capability of creating and rapidly delivering high quality, reasonably-priced goods to customers. This demand culminated in the development of the Flexible Manufacturing System (FMS), both as a manufacturing perspective and a technology.
The FMS philosophy centers on a holistic approach to instilling adaptability within a manufacturing organization at three levels. These three layers and associated segments, as described by the University of Kentucky, are as follows:
Basic Flexibilities | |
Machine Flexibility | How easily a machine can process various operations |
Material Handling Flexibility | An indicator of how easily various part numbers can be transported and positioned correctly at the machine tools in a site/firm's |
Operation Flexibility | An indiacator of how easily different equipment combinations can be used to create a particular part number |
System Flexibilities | |
Volume Flexibility | an indicator of a site/firm's ability to be profitable at varying volumes of existing part numbers |
Expansion Flexibility | How easily a site/firm can be built and expanded |
Routing Flexibility | An indiacator of the various available equipment combinations that can be leveraged for a specific manufacturing process |
Process Flexibility | An indicator of the quantities of a part numbers a site/firm can produce without additional setup requirments |
Product Flexibility | The quantity of particular part numbers than can be produced by a site/firm with limited setup |
Aggegate Flexibilities | |
Program Flexibility | How easily a site/firm can reasonably operate without outside intervention |
Production Flexibility | The quantity of set part numbers a site/firm can manufacture without major captial investment |
Market Flexibility | How easily a site/firm can adapt to chaning market conditions |
Reviewing these components of the FMS ideology, it is evident how critical production technology is to achieving flexibility at the basic, system, and aggregate tiers of an organization. This is where the Flexible Manufacturing System as a physical construct is applied to create competitive advantage. FMS technology is, conceptually, an automated production system which produces one or more part families in small, repeatable batches. The value proposition of the FMS is retaining the flexibility necessary to generate a variety of parts while capturing the production efficiency and economy of scale offered by mass production.
Although initially focused on machining industries, modern FMS encompass a broader scope of manufacturing environments: assembly, creating finished products from individual components, and forming, the formation of components or finished goods. A representative Flexible Manufacturing System is made up of five pieces:
- Require minimal changeover and set-up time between consecutive jobs.
- An automated material handling system which moves batches (jobs) among machines according to the respective part routing requirements.
- A computer control system that manages at least some of the following: routing of jobs through the cell; status tracking of all in-process jobs against required routing sequence; delivery of operational instruction to the production stations for each job; managing availability of tooling required to process each job per station; and monitoring of station operational performance and signaling of deviations.
- Buffer storage at either or both the work station and cell levels.
- Jobs to be processed within the cell, as input to the control system.
The Benefits of Utilizing a Flexible Manufacturing System
Implementing a Flexible Manufacturing System offers companies plenty of value, both in hard and soft savings. Overall, the automated nature of an FMS, from material handling to information management and machine interaction, removes the need for the majority of repetitive human tasks that would otherwise be required to operate the equipment cell. This reduces not only direct labor costs but opportunities for production injuries and accidents as well.
The automated controls within the FMS will also improve product quality due to machine driven accuracy and precision. This also decreases the cost of indirect labor to handle rework and repairs by eliminating error root causes. Further, the control system’s planning precision reduces both inventory and waste through more exact use of raw materials and components.
Flexible Manufacturing System deployment additionally increases equipment utilization. This is achieved through several means. The automated controls and handling components of the FMS frees the machine tools from human dependency, eliminating waiting on personnel to complete tasks. It furthermore allows most changeover and setup tasks to be performed externally, while the machine is still completing a batch, which minimizes the amount of machine downtime required between jobs. This combination of improved productivity with the same or fewer labor resources also lowers the overall cost per finished unit.
What Gaps Still Remain?
While a leveraged Flexible Manufacturing System offers many appealing advantages to a manufacturer, there still remain several disadvantages and qualifiers to this production approach. Foremost is the initial design and establishment of the FMS. Considerable time investment is needed to understand the current production state and to spec out the criteria for the FMS. On top of which, extensive capital must be spent to build and install both the physical and digital infrastructure of the FMS.
Relatedly, a Flexible Manufacturing System is best applied initially across a relatively narrow band on the product mix - product volume chart. Any somewhat large swings in a company’s product mix or product requirements could quickly exceed capability of its FMS to adapt. This could force additional investment within the FMS to accommodate the demand changes. If an organization has not fully matured, this process could repeat itself multiple times.
Lastly, the complexity of a Flexible Manufacturing System can create challenges for some potential adopters. Some firms may find that the technological capability of an FMS exceeds the processing needs of their products, especially in light of other barriers to implementation such as cost and lead time. The sophistication of an FMS may also require companies to make additional investments beyond the system itself; leveraging FMS could also drive further expenditures on technical literacy and training for support resources, as well as increased maintenance and energy costs over traditional production cells.
What’s the Best Path?
While Flexible Manufacturing Systems bring a host of benefits, these systems and particularly their implementation, also raise several concerns. Fortunately, whether these are financial hang ups or questions of organizational maturity, there are other means by which companies can achieve similar results. For those seeking to make targeted improvements to equipment availability and utilization, Lean Execution Systems (LES) such as Leading2Lean (L2L) provide an intermediate measure between current state and broad FMS deployment.
LES are designed to uncover and drive change across all plant processes, through the classification and capture of details for each unique event type desired. Not only do these include all the factors that an FMS may address – changeovers, material handling, etc. – but it further encompasses all site processes, production and otherwise. These events can be entered manually, though L2L as an LES provide for easy integration, so events can be logged automatically from production machine and sensor conditions.
LES reporting can then be used to analyze and expose the true systemic issues affecting productivity. While availability and productivity elements will be represented, they may be interspersed with other unconsidered but equally impactful issues. Taking a Pareto approach, the major contributor can be targeted for improvement, with a deep dive root cause investigation being retained also in the LES. Repetition of this process will incrementally improve process performance and stability to the point that FMS implementation is a logical investment instead of a potentially costly gamble.
To learn how L2L can help you start where you are (wherever that is) and take the next step toward improvement, contact us.
Revisions
Original version: 18 July 2024
Written by: Evelyn DuJack
Reviewed by: Daan Assen
Please read our editorial process for more information
Related Posts
Subscribe to Our Blog
We won't spam you, we promise. Only informative stuff about manufacturing, that's all.