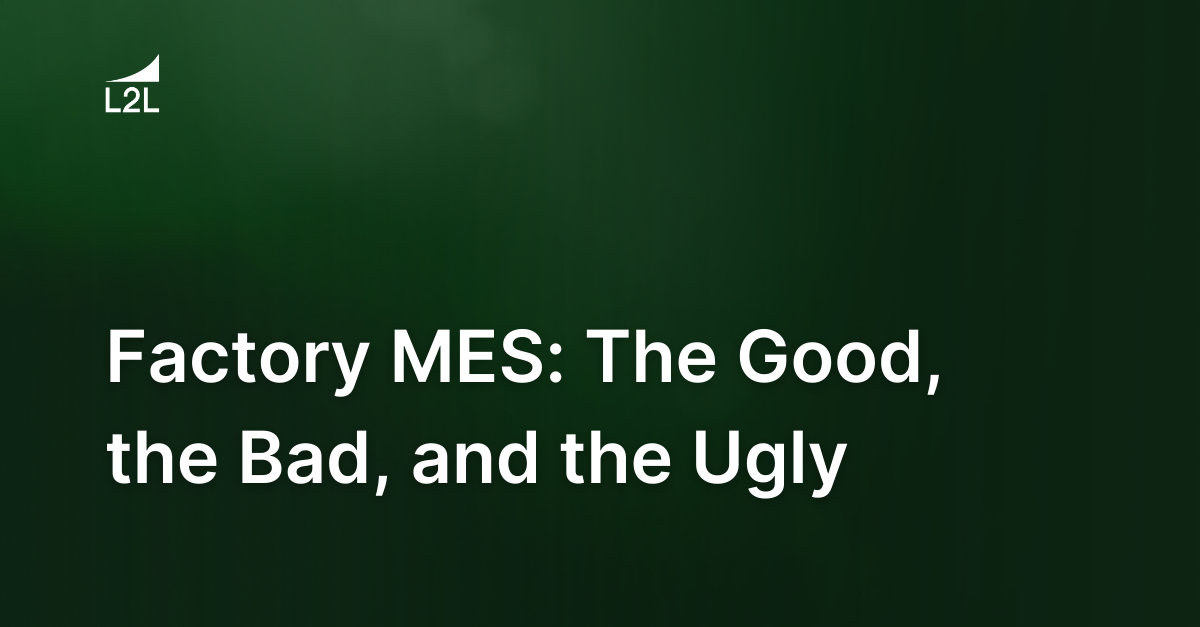
Estimated read time: 7 minutes
When it comes to production management and other day-to-day elements of manufacturing, the last thing you want is to rely on an incomplete data set. After all, you can’t go forth and conquer when you’re dealing with untrustworthy data to guide your decisions.
That’s why it’s important to know what you’re getting into, no matter the tool or software — and manufacturing execution systems, or MES, are no exception. Today we’re pulling back the curtain to reveal this solution for what it truly is — the good, the bad and the ugly.
Manufacturing execution systems: The good
Let’s start with the good news.
A manufacturing execution system is a digitized solution that promises to give you a complete view of your key production processes, illuminating every step on the journey from raw materials to finished products. In some ways, it keeps that promise.
A traditional factory MES can be described using what we call the Four M’s of Manufacturing: man, material, method and machines. There are certainly more elements at work on the factory floor, but these four M’s illustrate what’s working and what’s not working, which, in turn, helps guide continuous improvement. They’re like the primary colors of the manufacturing world.
With the Four M’s in mind, let’s take a look at where traditional MES excels:
Methods
Methods, while related to both machines and materials, are a whole separate animal. If you don’t have the tools to review and optimize the execution of every single process, workflow and data entry task — that is, if you rely exclusively on a traditional factory MES — manufacturing excellence will always be just a few feet out of reach.
Material
MES software also provides better material management. By enabling supply chain visibility, product traceability and process data, an MES can get you one step closer to manufacturing excellence.
While that’s all well and good — and certainly important to be aware of — it’s equally important to realize what’s not represented here. In other ways, traditional MES technology fails to keep the promises it makes to manufacturers like you — and here’s why.
Manufacturing execution systems: The bad
Don’t be fooled by first impressions. Although a factory MES can provide important value, it’s likely to let you down in other ways.
While traditional MES technology can help your manufacturing operation with methods and materials, there are a couple of equally important things it doesn’t address: man and machines.
Man
Need to capture data from everyone on the factory floor? Want to make sure a process remains consistent across different days and workers? Hoping to simplify material orders, quality inspection and data entry tasks? Of course you do — but if you’re relying on a traditional factory MES, you’ll be out of luck. This MES technology overlooks one of your most important assets — people — and doesn’t even bother offering an apology.
Machines
Any manufacturer worth their salt knows the important role of machines on the factory floor. And although MES can play an important role in production success, it doesn’t help keep those machines running smoothly, giving you visibility into equipment performance issues and process inefficiencies. Other systems like EAM or CMMS can be used to manage machine maintenance and performance, but even those systems don’t help you deal with all the other non-machine related issues that can disrupt production (more on that later).
The truth of the matter is that this MES software leaves a gap. It’s a big, ominous gap — the kind you wouldn’t dare to jump across. Unfortunately, unless your manufacturing execution and production processes are miraculously independent of both humans and workflows, your only option is to make that leap to connect man, methods, machines and materials.
Let’s see what that “leap of faith” looks like.
Manufacturing execution systems: The ugly
That’s right: This is where it starts to get ugly.
Let’s say you never read this blog (or any of our other manufacturing wisdom, for that matter). You’re optimistic and innocent, relying on a traditional manufacturing execution system to keep your shop floor and all its processes running smoothly, and you have no idea what kind of trouble you could be in.
Here’s what you’d be up against:
-
You’ll only have a fraction of the truth. Your factory MES tells you plenty about those methods and materials, but that’s like trying to drive with one eye shut. You’ll miss out on that additional data from man and machines, giving you a narrow and potentially disastrous view of the world.
-
Putting data together is messy. When separate systems capture your data, you don’t end up with perfect puzzle pieces. What you get is a piecemeal “truth” that takes a long time to put together — and you might end up using spreadsheets, pivot tables, manual entry and other solutions that feel outdated (because they are) just to make it happen. Plus, if any information is untrustworthy or incomplete, you’ll only be compounding those issues when combining different datasets.
-
Manufacturing excellence will remain a stranger forever. The traditional manufacturing execution system that made such big promises is really letting you down in the evolution department. It can’t keep up with the rapid digital transformation of the manufacturing industry, which means you can’t, either. In order to succeed in today’s environment, you need tools that allow you to break down data silos and keep everyone pushing in the same direction — and traditional MES can’t always deliver.
-
Highly specific problems will be your downfall. Credit where credit is due: A factory MES can give you some data. But when it comes to granular issues on the shop floor, you won’t have the information you need to diagnose the problem and execute an effective response.
If this hypothetical situation is making you frustrated, don’t worry — you’re not the first to demand more of factory MES.
That’s why many manufacturers are turning to a smarter solution: connected worker platforms.
How a connected worker platform saves the day
If you want a truly smart factory, you need a solution that can combine data from man, machines, methods and materials, creating one unified version of the truth. That’s where L2L Dispatch can save the day. It’s a closed-loop system, which means every process is informed by the data you capture along the way, allowing you to learn from the past and plan for the future inside a single platform.
Remember that gap left by factory MES? It won’t be showing its face any time soon.
With a connected worker platform, you can identify abnormalities anywhere on the factory floor and streamline your responses. Better yet, you can take those responses and deploy them every time a similar issue pops up — all because you closed that gap and united man, materials, machines and methods.
Here’s what your world could look like with a tool like L2L Dispatch:
Clarity and transparency
By providing insight into every process on the shop floor, and where your most costly production disruptions are occurring, a connected worker platform provides the clarity and transparency you need to operate with confidence. You’ll be able to diagnose and prioritize issues no matter where they come from — and know just what to do next.
Data-driven decision-making
Not sure how to prioritize problems? L2L Dispatch has your back. By showing you the most important data and revealing the truth about how each issue will impact your productivity, this platform helps you make choices that will benefit your factory, your people and your bottom line.
Communicable results
Once you’ve solved a problem, you can feed that data back into the system, creating a go-to answer that can be shared across the factory floor and even across the company.
Put L2L Dispatch to work today
Whether you’re tired of empty promises made by a factory MES or you’re just looking for a solution to layer on top of existing MES technology, you’ve come to the right place. At L2L, we’re all about putting that smart factory dream within reach — and with a connected worker platform at your disposal, you could achieve manufacturing excellence in no time.
Sound too good to be true? See for yourself by booking a demo today.
Revisions
Original version: 8 February 2022
Written by: Trent Maw
Reviewed by: Daan Assen
Please read our editorial process for more information
Related Posts
Subscribe to Our Blog
We won't spam you, we promise. Only informative stuff about manufacturing, that's all.