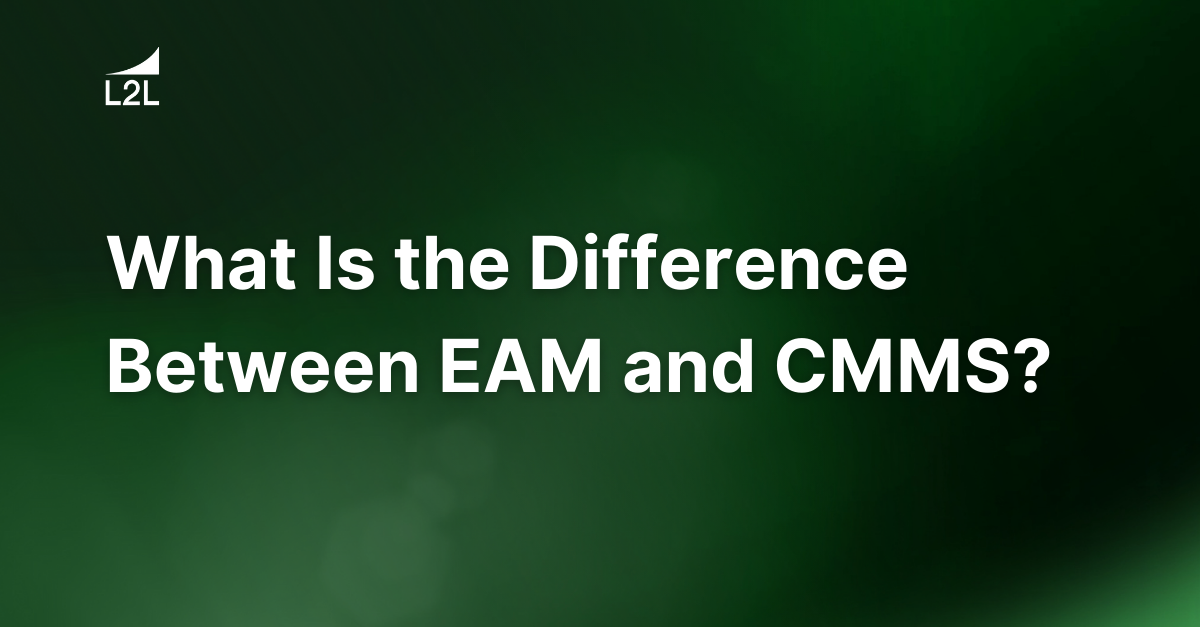
Asset management and maintenance are the backbone of manufacturing efficiency and productivity. As businesses strive to optimize their workflows and reduce operational costs, choosing the right software tools becomes all the more important.
Both EAM and CMMS are solutions that industrial businesses use to keep their facility and machinery in good working condition. While CMMS typically focuses on maintenance management, EAM software is broader in scope, covering the entire asset lifecycle.
To truly understand the difference between EAM and CMMS, we need to take a closer look at their definitions, key features, typical use cases, and distinct capabilities.
Understanding CMMS
A Computerized Maintenance Management System (CMMS) is a software designed to centralize maintenance information and streamline the management of a company’s maintenance operations.
CMMS helps organizations oversee all aspects of maintenance activities, including scheduling, tracking, and managing repairs and preventive maintenance for equipment and facilities, ensuring operational efficiency and data-driven decision-making.
Here are the key features of typical CMMS software:
-
Maintenance scheduling: Automates the scheduling of preventive and predictive maintenance to minimize downtime.
-
Work order management: Enables tracking of maintenance requests and work orders from initiation through completion.
-
Asset management: Records detailed information on assets, including location, condition, maintenance history, and warranty details.
-
Inventory control: Manages spare parts inventory, tracks usage, and reorders supplies to avoid stockouts.
-
Reporting and analytics: Provides comprehensive reports and dashboards to monitor maintenance activities, track associated costs, and optimize operations.
CMMS is typically employed by businesses that want to streamline operations through effective maintenance management. Common use cases include:
-
Manufacturing facilities: To reduce machine downtime and increase production efficiency.
-
Hospitals and healthcare facilities: For ensuring critical medical equipment is always operational and compliant with health regulations.
-
Schools and universities: To manage extensive campus facilities and automate maintenance tasks in order to improve asset longevity and safety.
-
Hospitality: Hotels and resorts use CMMS to handle routine maintenance and emergency repairs for guest rooms and common areas to boost guest satisfaction.
Organizations across various industries can use a CMMS to achieve a more organized, proactive maintenance process that improves overall operational reliability and efficiency.
Understanding EAM software
Enterprise Asset Management (EAM) software is a comprehensive tool designed to optimize the lifecycle management of physical assets across an organization. EAM encompasses a broader scope than CMMS, focusing not only on maintenance but also on the overall management of assets, from acquisition to decommission. Its purpose is to improve asset utilization, extend asset life, and ultimately enhance asset-related decision-making and cost control.
Here are the most common features you will find in EAM software:
-
Asset lifecycle management: Manages assets from planning and purchasing through to disposal, providing a holistic view of the asset performance and cost.
-
Maintenance management: Coordinates all work activities, including preventive, reactive, and corrective maintenance, ensuring efficient resource utilization.
-
Risk management: Identifies potential risks associated with asset failure and implements strategies to mitigate these risks and ensure compliance with regulations.
-
Resource allocation: Optimizes the use of resources, including personnel and equipment, to improve asset productivity.
-
Analytics and reporting: Offers advanced analytical tools to analyze and predict asset performance, helping you make informed strategic decisions about capital investments and maintenance strategies.
Typical use cases involve:
-
Utility companies: To manage extensive infrastructure and ensure compliance with stringent regulatory standards.
-
Transportation and logistics: For maintaining fleets of vehicles and associated infrastructure to minimize downtime and improve operational efficiency.
-
Oil and gas industry: To handle complex asset structures and high-risk environments, ensuring safety and efficiency in operations.
-
Manufacturing companies: Great for managing large and diverse sets of machinery and equipment to optimize production efficiency and maintenance processes across multiple locations.
-
Government and public sector: To oversee public assets and infrastructure, from roads and bridges to public buildings and parks, aiming for longevity and cost-efficiency.
EAM software is ideal for companies looking for a broad, integrated approach to asset management that encompasses financial, operational, and maintenance aspects. It's a holistic solution that ensures assets deliver maximum value over their lifecycle and align with the organization's overall strategy and performance goals.
EAM vs CMMS: The key differences
There are dozens of EAM solutions on the market, and probably hundreds of different CMMS vendors you can choose from. What complicates this discussion is the fact that they do not offer a universal set of features.
Sometimes, an EAM software will include one or two features typically found in a CMMS — and vice versa. In rare scenarios, there can be so much overlap that the solution you’re looking at could easily fit into both categories.
That said, in most cases, there are clear differences we can point to.
Scope:
-
CMMS is primarily focused on maintenance operations. It helps manage work orders, schedule repairs, and maintain historical records of maintenance activities.
-
EAM encompasses a broader range of asset management functionalities and gives organizations a birds-eye view of their assets, facilitating strategic decision-making.
Used by:
-
CMMS is typically used by maintenance and operations teams looking to improve the efficiency of their maintenance operations and reduce downtime.
-
EAM is used by various departments — including finance, compliance, operations, production, and maintenance — to ensure a unified approach to managing the organization’s assets for optimal operational efficiency and cost-effectiveness.
Implementation time:
-
CMMS systems are generally quicker to implement, as they are less complex and have a narrower focus compared to EAM systems.
-
EAM systems require a more comprehensive setup as they are typically integrated into many different aspects of an organization, thus taking longer to fully implement.
Cost to implement and run:
-
CMMS tends to be less expensive both in terms of initial setup and ongoing costs because of its focused capabilities and simpler architecture.
-
EAM systems, providing extensive functionalities and requiring integration across multiple departments, generally involve higher initial investment and maintenance costs.
What CMMS software can do that EAM usually can’t:
-
Rapid deployment: Simpler CMMS systems can be quickly implemented to immediately improve maintenance tasks. It also requires less comprehensive training.
-
Maintenance optimization: CMMS typically offers more advanced features for managing maintenance activities, offering more flexibility in terms of scheduling and tracking maintenance work.
-
User accessibility: Often designed with user-friendly interfaces, CMMS systems can be easier for technicians and operators to use on a daily basis.
What EAM software can do that CMMS usually can’t:
-
Asset lifecycle analysis: EAM provides tools to monitor and analyze asset performance throughout its entire lifecycle.
-
Strategic asset management: EAM includes capabilities for long-term asset planning, risk assessment, and investment forecasting, which are crucial for strategic asset management.
-
Broader facility management: Beyond just maintaining assets, EAM systems can include functionality for managing entire facilities, like space planning or energy management.
Ideal use cases:
-
CMMS is ideal for organizations that need a robust, focused system to manage and optimize their maintenance operations without the need for broader asset management functionalities.
-
EAM is suited for larger organizations that require comprehensive management of every aspect of the asset’s life cycle for strategic planning and execution.
Can EAM and CMMS work together?
In short, yes. It’s not unheard of to use EAM and CMMS in conjunction to get the best of both worlds: advanced maintenance management capabilities and a complete overview of your asset management activities.
With the right technical expertise, each system can be integrated to exchange information with the other and with existing software (like ERP). This helps prevent data silos, which often result from using multiple software solutions.
So, when is this the right approach?
Using CMMS and EAM together only makes sense when there isn't much overlap in terms of the features they cover. With CMMS vendors constantly expanding the scope of their products, this overlap is becoming more common.
Connected Worker Platforms: Better ways to manage maintenance and production
Traditional EAM software, while powerful, has many challenges — it’s usually slow, clunky, and not flexible enough for a modern manufacturer. CMMS solutions are typically more intuitive and customizable but give little to no insight into the production side of manufacturing operations.
What’s worse, both frequently come loaded with a bunch of features you pay for, but will never use. There is a better way.
The L2L Connected Workforce Platform is designed to create an efficient and safe production floor while minimizing downtime and friction between different teams. It enables you to digitize and centralize your manufacturing operations by giving each team the tools they need to succeed:
-
Operators and maintenance technicians get access to standard operating procedures (SOPs), digital work instructions, and safety guidelines and can report and fix problems quickly.
-
Maintenance managers get insight into machine and technician performance, ability to schedule preventive and predictive maintenance work, data to track downtimes and other important KPIs, and much more.
-
Production managers get real-time notifications about production issues, the opportunity to coordinate production and maintenance schedules around demand targets, and more.
-
Operations and HR managers get the tools they need to develop and track workers' skills, optimize internal workflows, manage resources, and implement new lean techniques.
-
Key decision-makers across all departments get access to granular maintenance, production, and cost-related metrics, helping them make the right strategic decisions.
If you want to see first-hand how L2L can solve your asset management issues, simply request a demo and one of our sales reps will be in touch!
Request a Demo
Revisions
Original version: 29 April 2024
Written by: Evelyn DuJack
Reviewed by: Daan Assen
Please read our editorial process for more information
Subscribe to Our Blog
We won't spam you, we promise. Only informative stuff about manufacturing, that's all.