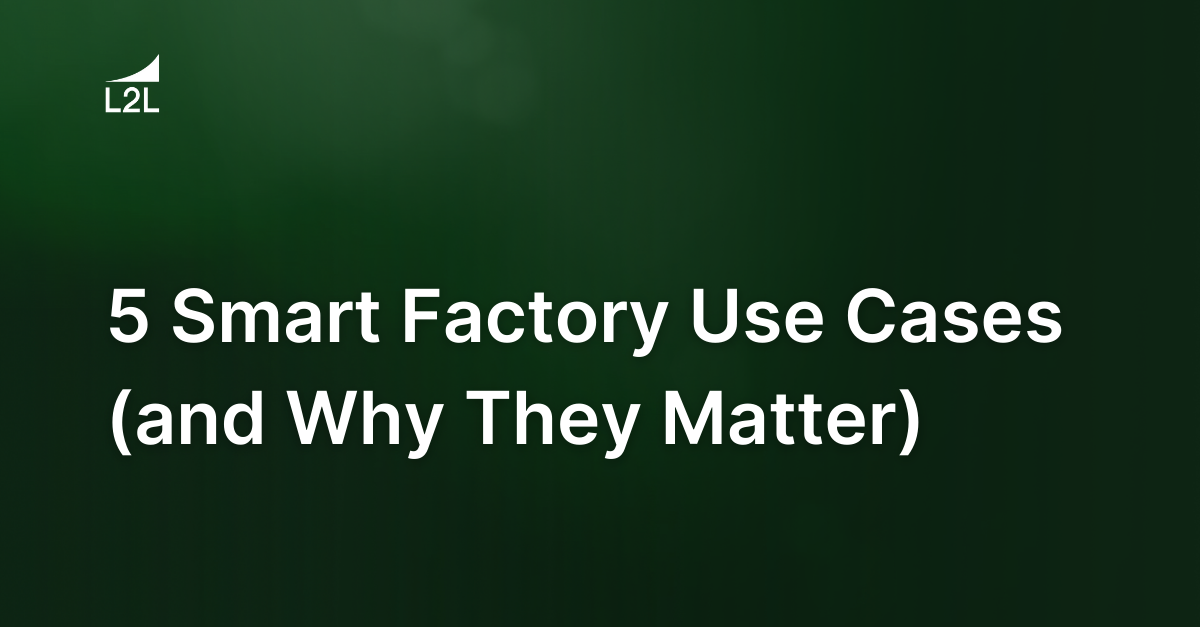
Estimated read time: 10 minutes
Do you ever wish you could take smart manufacturing solutions for a test drive? It makes sense — after all, you probably wouldn’t want to spend time and money deploying something that just won’t fit your plant. Unfortunately, while you can digitally try on clothes, taste ice cream flavors before you fill a whole cone, and even get free trials of new streaming services, the world still hasn’t figured out how to engineer a quick and easy test drive for smart manufacturing solutions.
That’s where we come in.
While we can’t exactly put you in the driver’s seat of a fully functional smart factory to test it out for a week, we can show you a few of our favorite smart manufacturing use cases that you may want to pilot and prove out. It’s not quite a test drive — more like an opportunity to see this approach in action.
These practical use cases may help you see smart manufacturing for what it really is: the future of the manufacturing industry (and maybe even the future of your plant).
What makes a smart factory so smart?
If this were a test drive, you probably wouldn’t hop right into the car and put your foot on the gas. First, you’d take a good look at the vehicle itself to make sure you knew exactly what you were getting into — both literally and figuratively. You’d pop the hood, inspect the paint job for chips, maybe kick a tire or two.
You should do the same thing (it’s called due diligence) when it comes to smart manufacturing.
Why? Well, the truth is that the “smart factory revolution” has become a pretty hot topic in the manufacturing industry. That’s good news for manufacturers — but it also means you could run into some misinformation or unrealistic expectations when doing your research. For that reason, we’re here to kick the tires of smart manufacturing and give you some insight into what you’re really looking at.
First things first: Let’s define the terms we’re using.
Smart manufacturing is the combination of humans and machines to create something neither could accomplish separately. By integrating the right tech tools at the right touchpoints, your manufacturing plant can become better, stronger and yes, even smarter than ever.
A smart factory is the result of smart manufacturing. It’s an interconnected system of devices, production data, machine learning and human input, all working together in harmony. A smart factory is often better at navigating supply chain disruptions, leveraging big data and standing out among other manufacturers. If you need any more convincing that this is a big deal, just remember: The opposite of a smart factory is, technically, a “dumb factory.”
Digital transformation is the process by which your average “dumb factory” becomes smart; it is, in many ways, synonymous with smart manufacturing. Essentially, digital transformation is the journey by which you choose every device, data analysis solution and cloud computing tool you need to digitize your operations and then deploy them in the right place at the right time. It’s all about digitizing your factory down to its DNA.
Long story short: Technology makes a smart factory functional, but knowing how and when to use that technology makes a smart factory smart. Naturally, that’s where smart factory use cases come in handy.
5 smart factory use cases
This is where the fun begins. If this were a real test drive, you’d be stomping that gas pedal and zooming down the freeway — maybe with a half-panicked car salesman in the back seat.
Of course, smart manufacturing doesn’t lend itself to the same kind of test drive — so let’s just take a look at a few key use cases instead:
Use case #1: Using data to identify solutions to problems
Let’s say you're successfully gathering data from machines, people, and even various systems into one place. Your job is done, right?
Not quite.
The truth about smart manufacturing data is that it's only a piece of what makes smart manufacturing successful.
To make it happen you need a framework for turning data into insights. That often benefits greatly from the creation of a cross-functional team — for example, representatives from the IT, Transformation, Operations, Reliability, Engineering and Quality areas of your plant. This group of sharp-eyed creative thinkers can represent the needs unique to their department when performing big data analysis. The result is an ongoing conversation about what this data means, how it can be utilized and how best to learn from these problem/solution patterns for other factory applications.
Use case #2: Addressing reactive solutions
When something goes wrong, from supply chain disruption to big data frustration, do you grab the first solution that will solve your immediate problems? Do you shrug off the consequences and focus only on how this will help you right now? That’s like putting a bandage over a huge wound: It may stop some of the bleeding, but it won’t address the underlying issue and certainly won’t protect against infection. Unfortunately, it’s not easy to get out of this reactive cycle when you lack the information and predictive insights necessary to evolve.
That’s why this is yet another smart factory use case: As it turns out, smart manufacturing includes kicking knee-jerk reactions to the curb and introducing predictive maintenance.
It starts with data capture. A smart factory is driven by real-time data gathered from machines and workers and then amalgamated into a single, highly precise view. Every decision made in this factory is based on analytics, accurate information and a full understanding of plant conditions — which means you’re able to choose the right solutions for the right problems. You’ll know when your production problems need a full-scale medical kit and when a small bandage will suffice.
Use case #3: Navigating a disrupted supply chain
This use case probably hits close to home. After all, the supply chain has taken a beating ever since the COVID-19 pandemic — and with market volatility thrown into the bargain, the entire manufacturing industry has felt the squeeze.
The interesting — and perhaps disappointing — truth about supply chain disruptions is that you’ll never be able to completely control them. Just like a tree can’t control the weather that batters its branches, even a smart factory faces some challenges it simply can’t overcome.
Luckily, this use case isn’t about giving up. It’s about using smart factory solutions to identify the things you can control and direct your resources accordingly. Sometimes that means using data and analytics to help you make sure you’re measuring the right things; other times, it means using machine learning and artificial intelligence, or robots to automate manual tasks, leaving you more time and energy to deal with the repercussions of the uncontrollable. After all, a tree may be at the mercy of the weather, but it focuses on building a strong root system so it can survive anything the world throws at it.
Use case #4: Managing big data
If the manufacturing industry isn’t already infamous for big data, it certainly should be. Your people and machines create information every second, and to have any hope of making informed decisions, you need a way to gather and analyze that data. Sure, you could whip out the old spreadsheet or start scribbling on a whiteboard — but the required time, effort and potential for human error are all convincing reasons to take a step back.
In truth, the best way to manage this big data is to let smart manufacturing take over. Smart factory software helps you capture information more effectively and automatically store it in a centralized database, allowing you to compare statistics, perform necessary data analytics and even decide where a new device might expand your view. The key is to work with your factory’s most granular information, not against it.
Perhaps more importantly, a smart factory should be well-equipped to turn that big data into meaningful insights. It’s not enough to simply capture and store information; you need to leverage data to help you make decisions and navigate challenges.
Use case #5: Dodging the break/fix pitfall
Without the right technology, it’s easy for your maintenance habits to fall into the break/fix loop. You’re responsive, almost panicked, like a rabbit running from a fox. Wouldn’t it be nice if that rabbit could identify the fox’s territory ahead of time and go the other direction?
That’s what a smart factory is capable of.
Say you’re stuck in a reactive mentality. You turn to smart manufacturing to help dig yourself out, and it all begins by placing sensors that will identify irregularities and other signs that a machine is going to fail. With this data in hand, you can perform the necessary fix ahead of time, avoiding this failure altogether. It’s called Condition-Based Maintenance, and it’s all about using tools like IoT devices to help the rabbit sneak around the fox.
For a real-world example, look no further than Sonoco Metal Packaging, an L2L client since 2017. With a little help from our connected workforce platform, they were able to create and implement their own Condition-Based Maintenance program, allowing them to confidently maneuver predictive maintenance scenarios and prioritize proactive repairs over total replacements. Results included $50,000 in yearly cost avoidance from a single problem being fixed — but if you want all the juicy details, you’ll have to keep an eye out for the full case study.
Making smart factory solutions work for you
Although it’s helpful to look at smart factory use cases, you’ll only know if this approach is a good fit once you sit down and think about return on investment (ROI). What do you need to consider to take smart manufacturing from “solving a few key problems” to “defining the future of the entire plant” — and where do you begin?
The key is to treat smart manufacturing as an evolutionary process. It takes time and effort to completely redesign yourself in this way; don’t rush the results, or you’ll start to lose out on that ROI. Instead, make each use case fit your unique plant, creating a one-of-a-kind partnership between your people and your tech.
Here are a few more considerations for getting ROI from a smart factory:
-
Make value-based decisions: Every choice you make in manufacturing should be about creating value. It’s up to you to determine which types of value are most important, but no matter what you decide, you should let that information guide your implementation of smart manufacturing solutions. That way, you end up with something that fits your needs — not something that tries to cram you into a premade box.
-
Don’t over-invest in tech: Technology is tempting, even to long-time fans of manual processes. Don’t let yourself grab every new tech solution. That’s tech for tech’s sake, and it’s not smart manufacturing. Instead, use other smart factory solutions to help identify specific places where technology would make a measurable difference.
-
Set realistic expectations: It’s important to know what smart manufacturing can do and what it can’t. For example, while a smart factory may be great at navigating supply chain disruptions, it can’t necessarily solve those problems; it can, however, help you identify what’s within your power and what you should stop worrying about.
-
Learn from yourself: One of the benefits of a smart factory is that it allows you to become self-aware. Through data analytics, machine learning and other solutions, you’ll be able to learn from previous decisions. Which solutions delivered the greatest ROI? What small change set off a chain reaction of incredible benefits? Once you know how to identify these patterns, you can leverage them throughout your smart manufacturing journey.
Start your smart factory journey today
If we could put you in the driver’s seat of a smart factory, we would — but for now, the closest we can get is showing you a few smart factory use cases, offering a few manufacturing best practices and helping you implement solutions for yourself. It might not be as fun as a drive down the highway, but hey — we’re always here to help you kick the tires.
Of course, if you’re ready to begin the smart manufacturing journey, we’re here to help with that, too. Take the first step by booking a demo of our connected workforce platform today.
Revisions
Original version: 18 July 2024
Written by: Evelyn DuJack
Reviewed by: Daan Assen
Please read our editorial process for more information
Related Posts
Subscribe to Our Blog
We won't spam you, we promise. Only informative stuff about manufacturing, that's all.