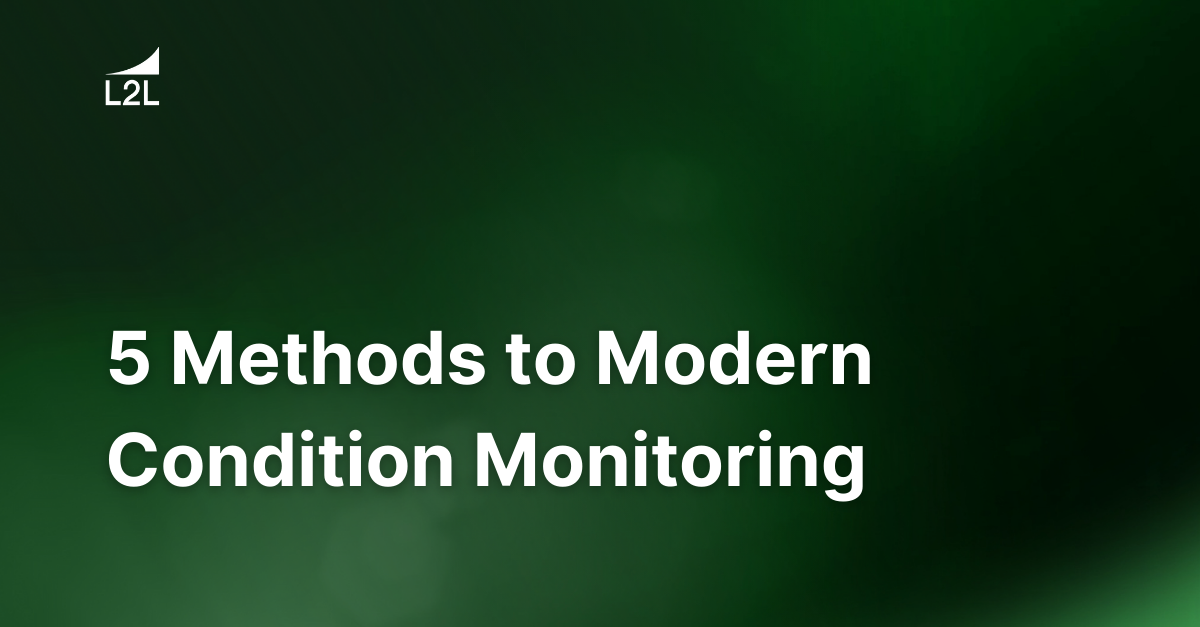
In the age of Siri and Alexa, it seems everything is constantly being monitored to identify commands or to provide input and solutions to optimize experiences. For example, my car is constantly monitoring a myriad of conditions via sensors such as tire pressure, water temperature, oil pressure, and even valve timing and climate control.
Many of these features have been around for a couple of decades, while some were introduced more recently. But they've all become standard in most car models. The benefits of these features have proven themselves in terms of safety, reliability, and convenience.
How did we evolve to this level of condition monitoring, and how does it apply to manufacturing?
Condition Monitoring In Manufacturing
I can vividly recall that when I first started to drive, my dad harped on me to check the oil level and make sure the tires were aired up properly. It was basic equipment care. With manufacturing, this habit of condition monitoring translates to what we now know as Total Productive Manufacturing (TPM) and, more specifically, tools such as Clean, Lubricate, Adjust, Inspect, Repair/Replace (CLAIR), to apply the same principles for basic maintenance in the manufacturing process.
These methods of basic condition monitoring are key in the early detection of defects to prevent equipment failures. It's pretty widely recognized that planned fixes are less expensive than reactive fixes. If you've ever run out of gas or had a blowout due to a worn tire, you know what I mean. Even with AAA, it's still going to throw a major wrench into your road trip — or your ability to meet a customer order on time.
Both cars and manufacturing equipment have become increasingly high-tech, and in turn, less serviceable by the average Joe. For example, you have to practically pull the engine to replace the oil filter in some cars. Manufacturing has also followed suit by building automated and incredibly high-speed processes that often make even the most basic maintenance a specialized task. That's not to say that if you see an oil leak under the machine or car, you shouldn't investigate or get it serviced.
The Next Evolution of Condition Monitoring
With maintenance tasks becoming so high-tech, what's the next evolution of condition monitoring? For manufacturing, it comes in the form of sensors. The Internet of Things (IoT) space is full of sensors capable of monitoring nearly every aspect of a manufacturing process.
Examples include:
-
Temperature / Thermography
-
Flow / Pressure
-
Vibration
-
Vision Systems
-
Sound / Ultrasonic
These are just a few of the conditions commonly monitored in manufacturing. Let's dig a bit deeper into these to really capture the value and benefits of each.
Temperature
There are many ways to capture temperature from thermographic cameras, thermocouples, and even basic thermostats. These devices provide critical data to ensure that certain environments stay at the optimal temperature to produce a quality product. Often, temperature is used to measure supporting assets such as pumps and motors, as failure can often be very costly and sometimes lead to major downtime events.
Flow
Flow meters are often used to monitor the volume of the liquid or air required to operate the facility or asset. High-speed equipment is now engineered so precisely that the air pressure required to support the process needs to be not only consistent in its pressure but in its volume as well.
Vibration
This one falls into the common bucket of Product Data Management (PDM) and other predictive maintenance tools. Vibration is often monitored in rotating equipment, such as motors, to identify early failures. Vibration analysis sensors allow you to remotely monitor these parameters. Not only does this give you peace of mind, but it also notifies you when a problem needs immediate attention and escalates the issue to systems like L2L's Connected Workforce Platform for resolution.
Vision Systems
This is another form of condition monitoring typically used to ensure products meet certain specifications and that equipment components are in the correct place. Vision systems have revolutionized the ability to prevent defects from going downstream by building processes in-stream to reject and quarantine anything that doesn't meet the defined standards. Vision systems have also reduced the number of mundane inspection jobs, allowing workers to focus on more value-added activities.
Sound/Ultrasonic Tools
Last but not least, ultrasonic tools provide another condition-monitoring method often used in facilities' pneumatic systems to identify leaks. Ultrasonic tools have other applications, but they're most often used to help stabilize the air system delivery. This is also an effective cost savings approach.
There are also many more condition-monitoring methods and sensors used in manufacturing than those listed above.
Human or Artificial Intelligence in Condition Monitoring?
So, will these solutions ever completely take the place of the operator or human element of condition monitoring? Personally, I don't think so. Sure, the car can tell me that my right front tire dropped 1 PSI, but it's unlikely that auto manufacturers will put a vision system in the wheel wells to see if I have a nail in my tire; the cost would likely outweigh the benefit to the consumer. A human being's keen senses will continue to work in parallel with the technology I've outlined above.
From our experience, we use technology most often in areas where there is no operator present, such as facilities and support equipment.
At L2L, we recommend a dual-pronged approach to condition monitoring. We believe in optimizing technology as well as the human element based on past data and risk assessment. This has proven to allow customers to achieve world-class operational efficiencies while leveraging emerging technologies in areas that support the investment.
For more information about how to enhance condition monitoring in your plant, contact us for a free demo.
Revisions
Original version: 18 July 2024
Written by: Evelyn DuJack
Reviewed by: Daan Assen
Please read our editorial process for more information
Subscribe to Our Blog
We won't spam you, we promise. Only informative stuff about manufacturing, that's all.