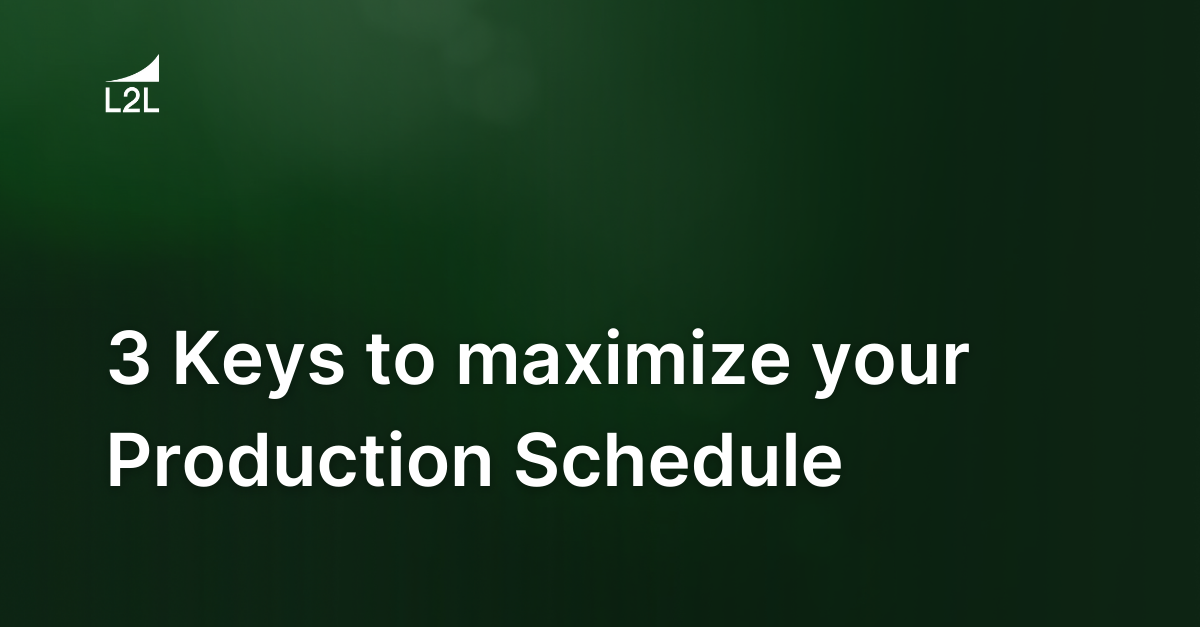
Over the past several decades, the manufacturing space has been beaten down pretty hard by the marketing beast that allows for the mass customization and hundreds, if not thousands, of SKUs (Stock Keeping Unit), per product family. The good news is, now that you know what SKU stands for, this reference will ring a bell whenever you see or hear SKU. It's no surprise when you go down a cereal aisle in any U.S. supermarket and find that there are usually about 10 different flavors, and then another 3-4 sizes, of each type of Captain Crunch. Better known as CAP'N CRUNCH in the business. Don't take my word for it. Ask your kids. This has been a boon for the consumer but a nightmare for the people trying to execute to this Production Schedule.
The Cereal Shelves Are Empty
This year has been the only time in my entire 36 years of life that I have ever seen the shelves empty in a supermarket. Almost all of the shelves. In every supermarket. It was mass hysteria the first few weeks of self quarantine here in the U.S. back in March. Many of the shelves where barren, and what was left was usually the shredded wheat, and who eats that stuff anyway? Aargh! Black Market Toilet Paper dealers and Pirates? Along with tooth breaking grape boulders, er, rather grape nuts. (Insert eye roll and call your dentist today. Book in advance because you'll end up with a broken tooth and dentists aren't essential.) It looks more like something you would clean dishes with. But I digress. This massive increase in demand caused a huge ripple in the supply chain that still has a few kinks in it.
Manufacturing responded to this unprecedented time by streamlining their Production Schedule to rapidly increase output capacity. The most common method was through SKU reduction. This strategy minimized the "Cats and Dogs" or small volume runners in the schedule to focus more on the more popular large volume runners. This shift has proven to be surprisingly effective and successful, as it reduces the number of forced changeovers and allows the process to stabilize for longer production runs. It has also had an added benefit of increasing quality due to the reduction in process variation that results from fewer changeovers.
Three Keys to a Winning Production Schedule Strategy
Many Manufacturers were able to react and respond much more quickly and efficiently to the demands of this new Production Schedule reality than most of us would have imagined possible. So how do did they do it? The three keys are: SKU Rationalization, Schedule Smoothing, and Focused Execution. Let's expand on these keys and how each plays into creating a winning strategy:
-
SKU Rationalization:
As we touched on briefly above, it's probably by design that the Marketing team is typically separated from the Manufacturing teams. Because the folks in the plants would likely strangle the Marketing carpet dwellers due to this mass customization and the endless minor tweaks to products and packaging. You know things always look easier on paper, from the chair behind the desk in that comfy office.
These tactics are all done in an effort to carve off pieces of market share from the competition. It's not uncommon for companies to end up with dozens of variations of the same product with custom labeling, packaging, and pack sizes. These all create chaos and added cost to the Production Schedule process. Often without evaluating the true cost. You could even be losing money when you run small orders with high levels of variation vs. your big runners or core SKUs. This is always a delicate balancing act. But truly capturing your takt time can help justify reducing your SKUs and allow production to focus more on products with the greatest profit capability.
-
Production Schedule Smoothing:
Fortunately for us, there are now software applications like L2L, who make managing Production Schedules easier than ever. With a robust Lean Execution System (LES) like L2L, everything you need to make good, well informed decisions is all together and immediately available at your fingertips. All of your product orders and the necessary due dates to meet customer delivery. Your asset and resource schedules, as well as scheduling tools like EPEI (Every Product Every Interval), another word for Heijunka, are built into the LES.
Having this degree of access to data allows you to optimize your production runs and streamline any changeovers to maximize your run time and output. The ease with which these tools facilitate all of these functions is remarkable especially when you take into consideration that this used to be the domain of pencil and paper, maybe dry erase boards. All of this had previously been executed by hand, on paper or in an excel spreadsheet. They were not nearly dynamic enough to provide the flexibility or visibility across all levels during a normal run, let alone the chaos and staffing challenges of a Covid Production Schedule process.
-
Execution:
Now that we have reduced the complexity and level loaded the schedule for optimum flow, the operations staff is still on the hook to deliver. By digitizing the process of scheduling and execution to L2L's Cloud Dispatch and its Production Module, it is far easier than ever before. Operators can see in real time the list of orders and upcoming changeovers. They also have real time visibility to whether they are winning or losing, thus enabling them to make adjustments or escalate issues digitally to support resources. Those resources may be working remotely or not directly stationed on the shop floor due to social distancing considerations. This approach has allowed manufacturers to continue meeting these increasingly high consumer demands while still maintaining a safe work environment.
Key Benefits of taking this approach:
- Enhanced Visibility
- Dynamic Scheduling
- Increased Productivity
- Fewer Changeovers
- More agile in staffing shortages
- Remote worker ready
- Quicker Delivery
The "New Normal" Production Schedule
Never before has manufacturing as a whole been on a burning platform like we are experiencing in 2020. It has forced many to step up and modernize their processes. Those who were ready responded with ease while others were left struggling to manage through these challenges. Many say this is the new normal. I suspect that includes the way we manufacture and manage the Production Schedule. If that's true, than companies will now need and have more contingency planning than ever before and will exercise them regularly. In addition, the need to digitize and leverage systems like L2L has never been more apparent: the ability to do more with less; secure a safe and healthy work environment, including ensuring social distancing, while still actively engaging and leading effectively.
If any of the issues or challenges above ring true for your plant or organization, don't wait. Reach out to L2L for a demo to learn how you can turn the corner on getting control of and maximizing your Production Schedule. We are busier than ever! Customers who have pushed off their digital journey are quickly making a move to bolster their process to handle the new normal.
Revisions
Original version: 18 July 2024
Written by: Evelyn DuJack
Reviewed by: Daan Assen
Please read our editorial process for more information
Related Posts
Subscribe to Our Blog
We won't spam you, we promise. Only informative stuff about manufacturing, that's all.