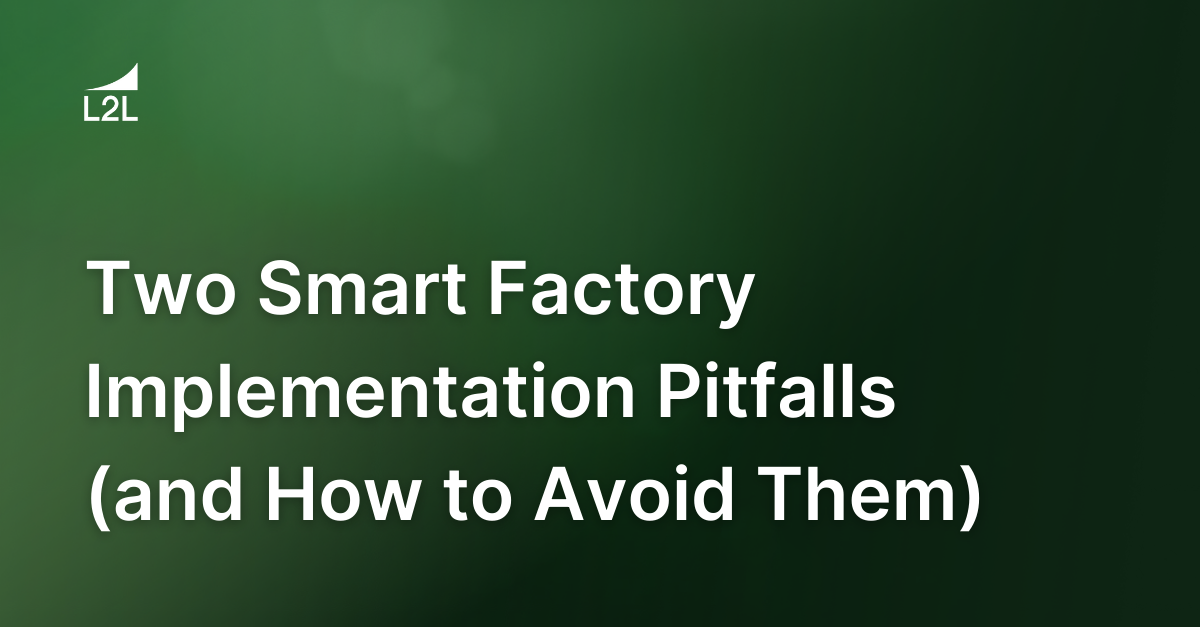
Few things are quite as frustrating as having a vision and not being able to reach it.
If you dream of efficiency, optimization, and digital transformation but can’t quite make those things a reality, don’t worry — you’re not the first to feel as if your manufacturing organization is doomed to be stuck in the past forever.
But you probably didn’t come looking for solidarity.
The good news is that there’s a way to make dreams a reality on your factory floor, and it all begins with one thing: the smart factory. However, even smart factory systems can leave you scratching your head if they aren’t implemented correctly.
Here’s how to get smart about the smart factory.
A Crash Course in Smart Factory Implementation
Smart factory systems are just what they sound like: a sleek, modern way to operate in the manufacturing landscape. The idea is to use smart technology pragmatically, enhancing and complementing human work with artificial intelligence, data capture, machine learning, and more.
When implemented properly, smart factory systems can deliver all kinds of benefits, including:
-
Measurable ROI: Quick, simple deployment of tech solutions can lead to operational excellence and visible ROI across the organization.
-
Improved efficiency: No more struggling to determine the cause of downtime — smart factories are outfitted with data capture and analysis capabilities to keep you informed 24/7.
-
Reduced upfront costs: It’s easier to control costs when you can track asset performance, employee workload, and more, all in one place.
-
Procedural improvements: Implementing a smart factory system makes it easier to streamline and improve operations, from predictive maintenance to real-time visibility to issue resolution.
But hold on just a minute. These benefits can only be enjoyed if you dodge a couple of significant pitfalls and create a full smart factory transformation — and knowing what not to do is the first step.
Smart Factory Implementation Pitfall #1: Maintaining the Status Quo
Remember elementary physics? One of the most basic rules is that an object at rest tends to stay at rest. The same principle applies to a manufacturing ecosystem. If you’re a little too comfortable with the status quo, you might be hesitant to try something new to keep operations moving forward.
There are a few reasons you might be in a “progress rut.” Here are some examples:
Financial hesitation
Long-term investments can often feel like a big risk. After all, you’re putting time, money, and resources into something that will pay off gradually. In a world where quick turnaround times are the new currency, patience can be difficult to maintain. That’s why some manufacturing leaders prefer to defer investment in smart factory implementation and often continue to put “band-aids” on issues that could be resolved with the right technology.
The truth, though, is that short-term investments usually deliver short-term benefits. They’re really just a bandage over issues with machine downtime, data capture, and access, operational efficiency, or your overall manufacturing process. In fact, they may even exacerbate the very financial pains they were supposed to overcome.
Concern about learning curves
Another reason manufacturers dodge smart factory implementation initiatives is the assumption that they come with complex learning curves. Training doesn’t just take time. It may also invite comments like, “The old way worked just fine. Why rock the boat?”
Luckily, user-friendliness and intuitiveness are core elements of the smart factory vision. The right tools, technology, and unifying process were all designed by manufacturers, for manufacturers — which means your people can count on experiences built on common sense. In fact, implementing smart factory technology could make things easier, faster, and simpler for employees, making “the old way” look just that: old.
Efficiency anxiety
Smart factory implementation might give manufacturing leaders pause if they don’t know if it will interrupt their workflows. That’s not entirely unreasonable; after all, technology doesn’t always have the best reputation, especially when it comes to integration with existing procedures and systems.
The good news is that smart factory implementation doesn’t have to be an efficiency nightmare. Deployment of the right tools is quick and painless, meaning your workflows won’t suffer, your machines don’t go down and your employees don’t have to stand around twiddling their thumbs while new tech is added to the manufacturing ecosystem.
The bad news is that hesitation isn’t the only challenge you’ll have to look out for.
Smart Factory Implementation Pitfall #2: Over-Investing in Tech
Being overly cautious represents one end of the smart factory implementation spectrum. At the other end is, of course, the opposite approach: embracing digital transformation with eyes for technology and nothing else.
In all fairness, a name like “digital transformation” suggests that technology will be paramount — and that’s true. Smart factories wouldn’t be nearly as smart if they relied on whiteboards and sticky notes to get the job done, which is why they’re an improvement over the old ways.
However, technology also can’t do the job alone. For example, say you deploy thousands of sensors across your factory floor. That’s a step in the right direction, but it’s not smart manufacturing. You also need to consider the placement of those sensors, the data-gathering process and analytics involved, the behavioral changes required from operators, and, most of all, whether the technology is solving a specific problem with projected ROI.
A technology-led mindset can undermine your smart factory projects and leave those benefits looking a little flat. Here are a few examples of what “too much tech” can give you:
-
High upfront costs: Technology can get pricey, especially if you line your pockets with it. These high upfront costs can quickly undercut any financial benefits you may expect from your smart factory system or hardware.
-
Low efficiency: A tech-led mindset can be like having too many cooks in the kitchen. There’s a lot going on and no clear way to manage it all. While the potential is there, the result ends up being frustration.
-
Slow ROI: Technology is just a tool. It needs a framework and solid procedures in order to be used to its full capacity. Without that framework, smart factory implementation results could be scattered and ROI may become sluggish.
-
Loss of faith: Slow ROI generally translates to a loss of faith in the tools and solutions, which is when manufacturing leadership may pull the plug.
Stepping Up to Smart Factory Solutions
Although these pitfalls may seem intimidating, the tools you need to succeed at smart factory implementation are well within your reach. The key is simple: You need to find the balance.
Addressing financial hesitancy
If you maintain the status quo for too long, digital evolution will leave you behind.
Instead of dragging your feet, look at smart factory systems as a sleeker, more powerful version of something familiar — like a phone booth compared to a mobile phone. The functionality is similar, and once you get started, you’ll find that the overall process is much the same; only the smart factory implementation has changed (and the benefits too, of course).
It’s also important to consider that smart factory systems are long-term investments. What that really means is that they’re one-way tickets to the future of manufacturing, so you’ll never have to slap an old-school bandage over an issue again.
Addressing over-investment in technology
The opposite problem requires the opposite solution.
Remember that smart factory systems must be respected as the intricate approach they are, which means they deserve gradual, pragmatic deployment. For every piece of new technology, you should also have a clearly projected ROI — one that helps you harness the power of your tech, enhance human skills on the factory floor, utilize all the data you now have access to and ultimately achieve bottom line savings or profits. In summary, the goal is to solve targeted problems, learn from those solutions, and apply them across the factory and even the rest of the company.
Finding Your Balance in Smart Factory Implementation
If these solutions seem a bit broad, that’s because they are. The real secret to smart factory success is finding a balance that works for you — and to do that, you need a platform that keeps production data, asset information, up-to-the-minute analytics, and other mission-critical details all in one place. Additionally, it would be helpful if that one place was in the palm of your hand.
That’s right: L2L’s smart manufacturing platform makes it easy to deploy smart factory technology and be an active part of digital transformation at every step. With real-time mobile access, you can stay updated on machine downtime, create a solid resolution structure to standardize responses across multiple locations, and even utilize machine learning or other AI tools.
Get Smart with L2L
If you’re ready to get started with smart factory systems, you’ve come to the right place. As manufacturers ourselves, we know what makes you hesitate — and what makes you eager to get your hands on a new solution. We’ve taken that background knowledge and created a platform that puts smart factory solutions directly in your control, all without the stressors or complexities that can throw a wrench in your workflows.
To learn more about the smart approach to smart factory implementation, download our eBook today.
Revisions
Original version: 18 July 2024
Written by: Evelyn DuJack
Reviewed by: Daan Assen
Please read our editorial process for more information
Related Posts
Subscribe to Our Blog
We won't spam you, we promise. Only informative stuff about manufacturing, that's all.