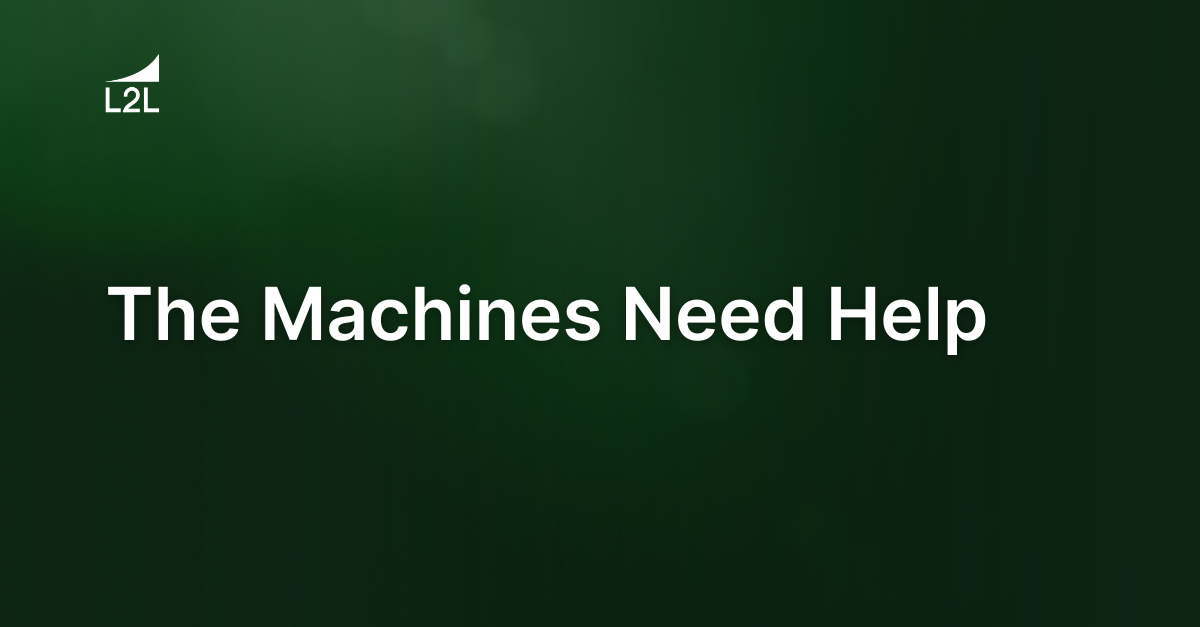
Estimated read time: 5 minutes
In an era dominated by technological advancements and automation, the role of human workers often comes under scrutiny. Some argue that technology is replacing traditional jobs and making human labor less valuable. However, a recent article published in the Wall Street Journal sheds light on the vital importance of a connected workforce alongside investment in automation. The article centers around the Craftsman Factory in Fort Worth, Texas, and its inability to produce as expected due to various machinery-related issues.
The Craftsman Factory opened with much fanfare. It “reshored” manufacturing from Asia to the US. It was intended to make sockets, ratchets, and wrenches emblazoned with the “Made in the USA” stamp. Craftsman hoped that additional automation and close-to-customer manufacturing would avoid potential supply disruptions while increasing profits. Unfortunately, this factory’s dependence on machines rather than a more efficient labor force caused issues that crippled the plant, leading to its recent closure.
Why did this strategy fail? Let’s take a closer look.
Over-Dependence on Machines
Craftsman attempted to reduce costs by employing state-of-the-art robotics. It would move from labor intensive manufacturing to automated manufacturing, in the process transitioning operations from Asia to the US. The problem with this plan was that it depended on the machines working at max capacity with complete efficiency. Neither of these things happened.
With Covid-related parts shortages and machines that didn’t live up to their hype, Craftsman was in a tough position. The machines couldn’t maintain quality control at higher production speeds and lower speeds meant lower profits. Shifting to an increasingly manual process made sense, but that justified moving production back to Asia, where labor rates were cheaper.
Understaffed and Unprepared
There is a base amount of labor needed for a factory to handle maintenance and production. If you hire less than this number, you risk quality issues, safety issues, and underperformance. You also restrict the factory’s ability to react to disruptions.
A major problem at the Craftsman Factory was the quality of manufactured parts. With only 35% of the intended workforce actually hired and many of them conducting maintenance on the machines, shop floor workers were overloaded and unable to handle the quality issues effectively. While Craftsman did manage to get many sockets produced, it failed to produce enough high-quality wrenches and ratchets — key components of the complete hardware sets that consumers demanded. This inability to produce the right mix of quality parts added to the factory’s woes.
Failures of Flexibility and Adaptability
In a rapidly changing world, adaptability is a key trait that human workers possess. While machines seem to operate at peak performance for longer, when issues arise, there is a higher propensity for machines to go “down” — producing nothing for long stretches of time.
The Craftsman Factory highlights the necessity of a flexible workforce that can readily respond to market fluctuations and quickly adjust to production changes. Unlike fully automated systems that might require significant reprogramming and investment to adapt to changing needs, human workers can quickly switch from one task to another, bringing remarkable agility to the production process. If additional labor is needed, hiring and training can take place faster than building a specialized production robot. Well trained and connected workers ensure that production goals are met and the factory remains financially viable.
Conclusion
While technological advancements and automation have undoubtedly revolutionized industries worldwide, the Craftsman Factory stands as a testament to the unmatched importance of human workers. The integration of modern technology should not overlook the flexibility, adaptability, and versatility that human workers bring to the table. As we move forward into an increasingly automated world, it’s crucial to strike a balance between automation and human labor. Embracing automation where it complements the existing connected workforce will lead to a more productive manufacturing plant. The Craftsman Factory reminds us that, while machines may offer abilities that humans don’t possess, they still need help to achieve their full potential.
If you’d like to support your automation efforts with an strong connected workforce, reach out to us and book a platform demo today.
Revisions
Original version: 31 July 2023
Written by: L2L
Reviewed by: Daan Assen
Please read our editorial process for more information
Related Posts
Subscribe to Our Blog
We won't spam you, we promise. Only informative stuff about manufacturing, that's all.