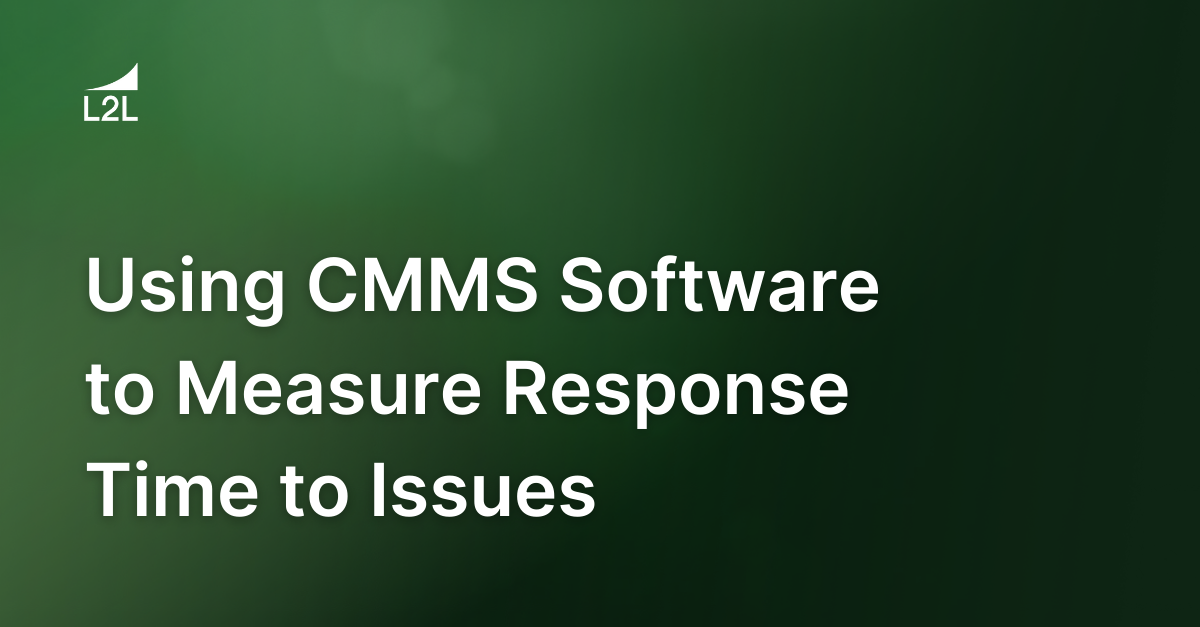
Does your current CMMS software provide response time by individual causes/events? Can you objectively quantify response time to a job? If the answer is no, then you need to fix that first. Otherwise you won't be able to use that information to understand what's driving the response time. As you understand that more clearly, you'll know what your best opportunities are to drive improvement and eliminate waste.
What Your CMMS Software Should Tell You About Downtime
Some may think that keeping the total downtime clumped together and not separating it out is best. However, downtime is not all wrench time. The machine may be down 60 minutes when it only took 15 minutes to make the repair. Some may view the call as downtime of 60 minutes, when truly a majority of the waste and opportunity lies within the 45 minutes of unknown time it took to complete the job.
Are you able to breakdown your total downtime and categorize the other incidental tasks? Can your current CMMS software categorize the Total Downtime and distinguish wrench time, response time, etc.?
Response time can be a powerful KPI intended to help manage a process. Allowing total downtime to be categorized as one event allows for hidden inefficiencies and poor processes that cannot be improved. You can't resolve an issue until you can clearly see it and define it.
For example, the Response Time to issues can be a good indicator of how efficient your overall facility and processes/procedures are running. Excessive Response Times can be an indicator of:
-
- An understaffed maintenance team
- Poor communication process to notify of issues
- Lack of real-time visibility to issues as they occur
- Slow/Long travel time to issue
- Under-defined Process and Procedures
- Inefficiencies in obtaining proper tools, work instructions, drawings, etc.
- Technician looking for Spare Parts / Complicated Process
- Technician obtaining spare parts as needed
Not measuring response time (or masking it) skews the perceived amount of time it really took to get the machine up and running after a breakdown.
By measuring and categorizing every minute of the total downtime, you get a much clearer picture of what's lengthening the time it takes to resolve the issue. A large portion of the downtime may be the response time. However, in order to understand this and make improvements, we must separate and measure all the causes of downtime and understand them each individually.
Honor the reality, identify and eliminate waste.
Can Your CMMS Software Give You the Data to Solve Problems?
Once you measure response time and other causes, you can then begin to identify all variables and incidentals that drive up response time. In the past, I have seen some simple procedures and reactive countermeasures put in place to reduce response time. However, you must honor the reality and address these causes. Some very simple and very effective countermeasures include:
-
- Scooters/Bikes. Transportation for maintenance technicians may reduce lead-time.
- Increased Workforce. Adding skilled technicians.
- Mobile Devices. Technicians are able to access notifications, drawings, and work instructions at the point of use. This eliminates running to offices and/or finding individuals that can provide documents.
- Spare Parts Delivery to Machine. Spare parts ordered from machine/mobile devices can be delivered to the machine or central drop-off locations.
- Visual Indicators. Area/location dashboards can tell you, at a glance, what is Normal vs Abnormal.
- Kits @ Point of Use. Kits for machine/line kept in Kanban locations at the work site and are replenished based on time.
Each site and Facility will bring its own set of unique constraints. However, if you are not measuring Response Time with your CMMS software, you need to. If you are measuring Response Time, ensure you are reviewing this powerful KPI regularly and identifying the waste within this Total Downtime Data.
Can your CMMS software do this? Most can't. Check out our eGuide on why CMMS will let you down –and the steps you can take to change that.
Revisions
Original version: 18 July 2024
Written by: Evelyn DuJack
Reviewed by: Daan Assen
Please read our editorial process for more information
Related Posts
Subscribe to Our Blog
We won't spam you, we promise. Only informative stuff about manufacturing, that's all.