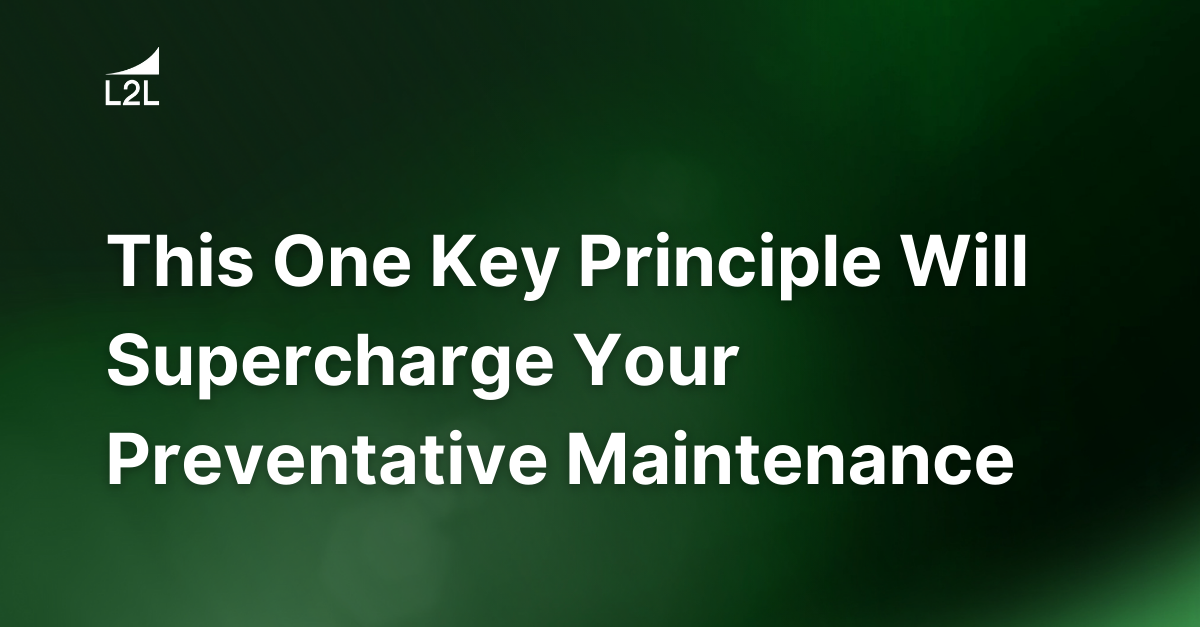
Every Preventative Maintenance Plan hinges on the fact that there are usually not enough time or resources to complete everything that needs to be completed. Each PM in the plan has specific tasks and requirements that, in most cases, are critical to ensuring the equipment continues to run. But, all too often, the Preventative Maintenance Plan does not incorporate the one key principle that, if adhered to, would free up a tremendous amount of resources and help the maintenance organization tremendously. This one key Principle Is Known as the Zero-Failure Principle.
The Zero Failure Principle
So what is the Zero-Failure Principle and why is it such an important part of your Preventative Maintenance Plan? Well, it is actually very simple. The principle is best explained when speaking of an iceberg. The part of an iceberg that can be seen on the surface in the ocean is usually much bigger under the water than the portion that is sticking out of the water. Hidden underneath where the eye usually cannot see is a large mass of hidden ice. It is thought that the Titanic actually hit this hidden ice of an iceberg rather than the piece protruding from the sea based on the way the damage was observed along the Starboard side of the ship, punching the fatal hole in the hull as it passed.
Much like the iceberg, machine downtime, quality defects, and safety incidents are usually just the most blatantly visible portions of machine failure and the ones most people are attempting to avoid. The issue is that they are attempting to avoid the downtime, but at the same time, totally ignoring the underlying issues that are really causing the systemic failures. These underlying issues are what we call Hidden Abnormalities, and eliminating them must be an integral part of any Preventative Maintenance Plan.
Hidden Abnormalities and Preventive Maintenance
In the maintenance world, and more specifically in the implementation of TPM (Total Preventative Maintenance), the identification and elimination of these hidden abnormalities is the very bedrock of the the first pillar of TPM known as AM (Autonomous Maintenance), or also known as OPM (Operator Preventative Maintenance). Call it what you will, but no Preventative Maintenance Plan can survive without it. Why do I know that to be true? Well, because much like our iceberg, these hidden abnormalities pose great danger and risk because they are the tell-tale signs of an impending downtime event. AM and the operators who perform the daily cleaning and inspection of the machine are the proverbial lookout in the crows nest. The life cycle of one of these abnormalities can be best illustrated by a simple example most everyone in a manufacturing plant has been exposed to at one point in time.
In this case, let's use a hydraulic leak as our subject. A new machine is bolted to the floor and is placed into production. This new machine is hydraulically powered and is used most days by an operator who does not have any responsibility for maintaining the machine, "that's maintenance's job".
Over time, a small puddle of oil begins to appear on the floor. Because the machine continues to produce product, there is no sense of urgency, no indication to investigate to avoid an emergency, to stop and find out where the oil is coming from. Pretty soon, some pig mats begin to appear on the floor to help contain the oil from oozing out into the aisle. And yet the machine continues to run, although we are starting to get some low oil alarms and every once in a while, we have to shut it down to refill the tank.
Then, some time later, and without anyone making a big deal out of it, it becomes very difficult to talk and hear around this particular machine due to the hydraulic pump noise. Then, out of the blue, without any "warning", the machine goes quiet and the operator cannot get the press to operate. Maintenance is called and if they have the part, they spend the next 8-12 hours removing and replacing the hydraulic pump. And to point out the ironic twist in our story, the likelihood of them fixing the leaking hose while they have the machine down is very low. Not as low as the oil level, but still. So we fill the tank with oil again, start the machine, and the entire broken process begins anew.
The Operator in the Preventive Maintenance Plan
A simple story, but yet very familiar to many many manufacturing plants around the world. But, had their Preventative Maintenance Plan taken into account the Zero-Failure Principle, this could have all been avoided early in the process. How? By empowering the operator as the frontline lookout in our plan, identifying the small original abnormality.
So, here is the question for you the reader: Does your Preventative Maintenance Plan include the processes and the tools needed to help the operator identify and track these hidden abnormalities? If not, you may want to consider implementing a system like L2L's CloudDispatch, that gives the Operator a process and the tools with which to record and log these hidden abnormalities directly to the piece of equipment. Then, as part of an overall Preventative Maintenance Plan, the maintenance planner scheduler can incorporate the rapid and repeatable repair of these small abnormalities before they turn into the large downtime events we are all trying to avoid.
If you found this helpful, you might benefit from our recent blog on Preventive Maintenance Checklists (Template Included).
Revisions
Original version: 21 July 2020
Written by: Eric Whitley
Reviewed by: Daan Assen
Please read our editorial process for more information
Related Posts
Subscribe to Our Blog
We won't spam you, we promise. Only informative stuff about manufacturing, that's all.