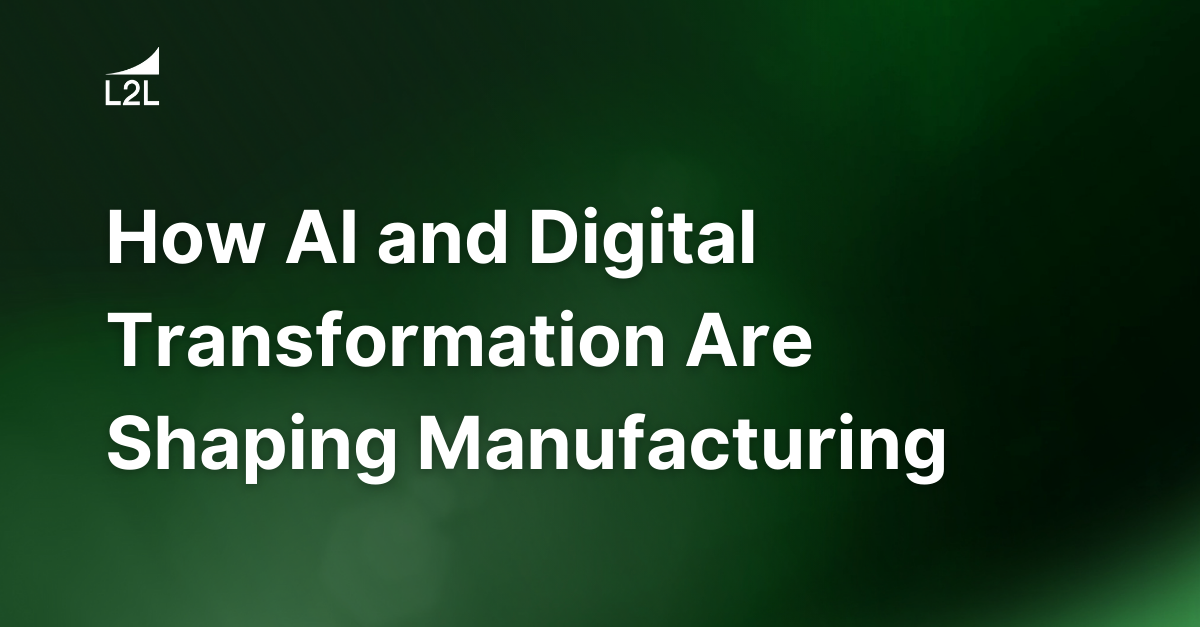
The manufacturing industry has long been characterized by its drive toward efficiency and productivity, consistently seeking ways to streamline operations and enhance output. The ongoing automation trend, encompassing AI and digital transformation, represents the latest chapter in this evolution. It builds upon past advancements while promising to redefine how manufacturers operate.
Let’s delve into the key automation trends shaping the industry and explore how manufacturers can harness these tools to drive efficiency and innovation.
Automation trends: The new era of manufacturing
Manufacturing is a delicate balance of standardization and innovation. Both are required for an operation to remain sustainable and competitive. This constant change drives several trends when it comes to automation.
From specialized to general-purpose machines
One of the most noticeable trends in automation is the shift from specialized machines to general-purpose systems. In the past, machinery was designed for specific tasks, requiring highly skilled human operators. Today, advanced multi-functional machines, such as CNC machines, 3D Printers, and Robotic Craftsmen, can be programmed to handle a variety of tasks.
The digital control of these machines allows them to quickly adapt to different products and processes, reducing the reliance on specialized hardware. These general-purpose machines provide manufacturers with far greater agility for future innovation.
Intellectual property is moving to data
In the early days of the Industrial Revolution, the manufacturing intellectual property (IP) that defined processes and products was embedded in the skills of the artisan craftsmen as tribal knowledge guiding their use of hand tools. Over time, as automation progressed, some of this knowledge was transferred to machines through tooling and templates.
Now, with digital transformation, this IP is increasingly captured and stored in databases. Advanced digital systems enable manufacturers to design, test, and implement processes outside the manufacturing environment through the use of Digital Twin technology, with the information transmitted to machines via software. Manufacturing IP managed as data allows for algorithmic updates to the manufacturing process through the creative use of AI and Machine Learning, significantly driving down the innovation cycle time.
Decreasing skill levels required for production
The role of the human worker has evolved significantly as automation has advanced. Artisans, who once needed years of experience to master their craft, have gradually given way to technicians and operators.
With the rise of digital transformation, much of the decision-making and control is moving away from humans and into software. This has led to a reduction in the skill levels required for production work, allowing manufacturers to focus their human capital on higher-value activities. Reallocating human capital to innovation and away from repetitive, low-value tasks has the potential to drive up long-term financial outcomes.
The role of AI and digital transformation in manufacturing
Digital transformation is more than just a buzzword—it is the logical extension of manufacturing's drive toward efficiency. It brings visibility and control to the manufacturing process, enhancing automation efforts. By embracing AI and digital transformation, manufacturers can unlock the full potential of their operations.
Here are a few areas in which AI and other digital innovations are making a huge impact.
Enhancing visibility and control
AI-powered systems provide real-time insights into machine performance, quality metrics, and production planning. This allows manufacturers to optimize processes and proactively address issues before they become problems. AI can also analyze vast amounts of data to uncover trends and insights that humans would struggle to find, further improving efficiency.
Shifting to data-driven manufacturing
Data is becoming the most valuable asset for manufacturers. Through digital transformation, companies can harness data to drive decision-making, improve processes, and enhance product quality. AI can help interpret this data, identifying patterns and making recommendations that can lead to significant improvements in productivity.
Supporting labor and skill development
With the right digital tools, manufacturers can automate routine tasks, freeing up labor for more strategic activities. This is crucial as the required skill levels for production continue to decrease. By automating repetitive tasks, companies can focus on training their workforce to manage and optimize the advanced systems that are becoming standard on the shop floor.
Preparing for the future of manufacturing
Manufacturers must embrace digital transformation to stay competitive in the evolving industry. This transformation is not just about adopting new technologies; it’s about rethinking how processes and workflows are designed and managed in the new world of human-machine interaction.
At L2L, we understand the challenges manufacturers face in this digital era. Our Connected Workforce Platform can accelerate your digital transformation journey by standardizing processes and improving data capture, which is essential for AI initiatives. Additionally, our products help free up labor so your workforce can focus on advancing your digital and AI efforts.
The rapid pace of change in manufacturing requires agility and foresight. By leveraging AI and digital transformation, manufacturers can improve efficiency, enhance data utilization, and empower their workforce to focus on strategic innovation.
Schedule a personalized demo today or reach out to sales@l2l.com to discover how our solutions can help you future-proof your business in this era of automation.
Revisions
Original version: 16 June 2024
Written by: Tyler Whitaker
Reviewed by: Daan Assen
Please read our editorial process for more information
Related Posts
Subscribe to Our Blog
We won't spam you, we promise. Only informative stuff about manufacturing, that's all.