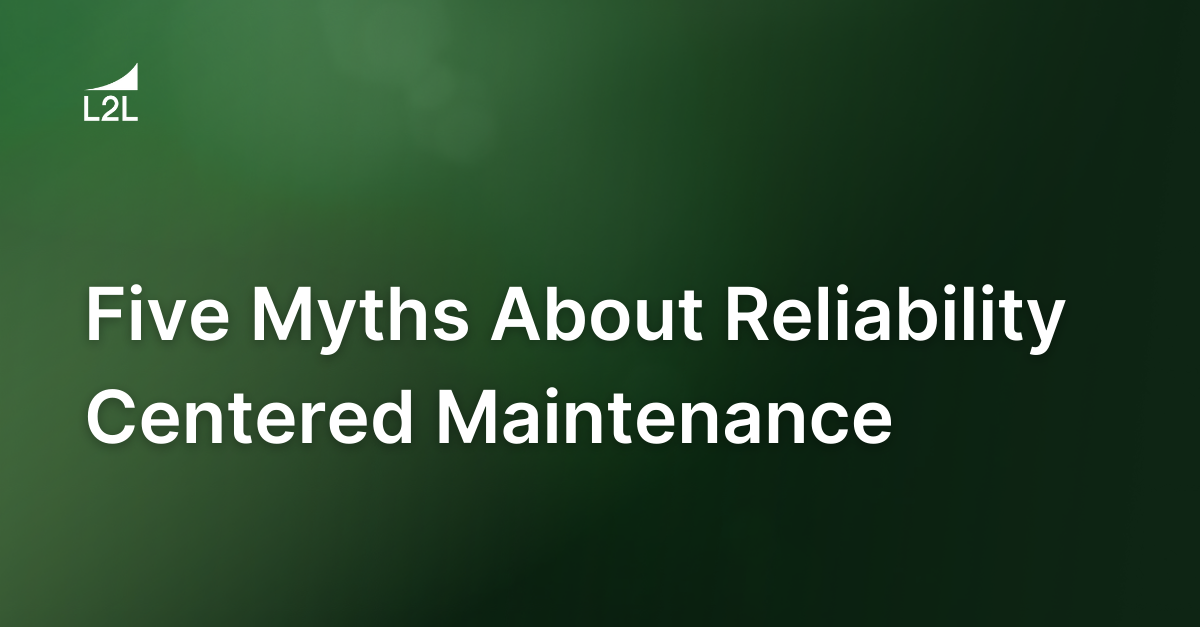
When it comes to reliability centered maintenance (RCM), many myths prevail. Here are some common myths and why they should be dispelled for you and your workforce.
MYTH #1: RCM Makes Sense for All
When you have a big oil processing plant, or similar situations, where millions of dollars per minute may be your reality, then it can make sense. It makes sense in two scenarios:
- Failure is catastrophic because human lives or safety are at stake; think of the aviation industry. If an aircraft fails and crashes, it’s catastrophic.
- Failure can cost the company a tremendous amount of money in terms of lost production or quality.
The hard reality is that this kind of failure can also be extremely costly in terms of damaged reputation and investor confidence. There is no way to put a price tag on human lives that may be lost. In any facility, there might be specific places where RCM makes sense because of safety or mitigating risk.
For the majority of cases, a manufacturer's operations don't involve the high level of risk that would justify RCM. In those cases it ends up being overkill and probably not worth the investment.
MYTH #2: RCM Makes Sense for Every Maintenance-Related Failure
In RCM there’s always the “sudden infant death syndrome.” In other words, components may fail early in their life, due to no reasonable explanation other than they slipped through the quality control of the manufacturer where they were procured.
A part may be brand new and still fail. When it does, it usually fails early. Early failure can’t be explained by faulty maintenance management or through poor maintenance policies and execution, which include RCM. The part failed due to a bad component or batch from the factory and all the RCM in the world will not prevent its failure.
MYTH #3: RCM Will Save You Money
Sometimes it could cost more than it’s worth. There’s no ROI from RCM for most manufacturers. It’s situational and depends on the application and the equipment, systems, and environment. While RCM is very methodical and avoids subjectivity, some ingenuity is always welcome and can end up overriding RCM signals and practices.
Myth #4: If It Ain’t Broke, Don’t Fix It
Nothing lasts forever. And most everything can last longer and more efficiently with some maintenance, even if that maintenance is relatively minor. If equipment is old and worn, failure can happen at any time. As equipment ages it may require a higher level of proactive maintenance to ensure that the chance of an unplanned failure is minimized. This may include adding more preventive or predictive maintenance or even planned equipment rebuilds to bring the machine back to a like-new level. It's also extremely critical to document standard repair procedures that are available to everyone to ensure that knowledge is continually being shared. At some point the cost of maintenance may even justify purchasing a replacement as the best business choice. In summary equipment maintenance should never be ignored and should evolve with the life of the equipment.
Myth #5: The Cost of Parts and Labor Is All That Matters
Disruption matters more. Production must allow and schedule for maintenance to take place. Production doesn’t want to stop producing product. They never want to take the race car off the track. In that analogy, the race car driver only cares about keeping the car on the track so he can cover distance and finish the race. The pit crew only cares about making sure there’s not a breakdown during the race.
With that mentality, if the car finishes last but never breaks down, they were successful as a pit crew. What we really want is for both to be aligned behind the common goal of winning the race!
Interested in the path to maintenance mastery? Check out our free eGuide:
Revisions
Original version: 18 July 2024
Written by: Evelyn DuJack
Reviewed by: Daan Assen
Please read our editorial process for more information
Related Posts
Subscribe to Our Blog
We won't spam you, we promise. Only informative stuff about manufacturing, that's all.