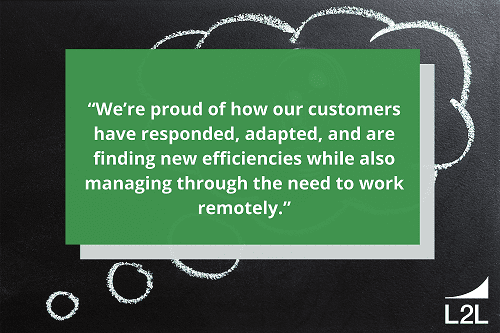
Spring 2020 marks an unprecedented environment across the world, certainly for manufacturers trying to protect the safety of employees and the community from COVID-19 while still keeping production running.
One thing rings clear, however, from the presenters of the 2020 L2L Manufacturing Virtual Summit (first time holding this event online). Many manufacturers are stepping up, adapting, and finding ways to succeed.
To paraphrase the kick off speaker, Keith Barr, President & CEO of L2L, “We’re proud of how our customers have responded, adapted, and are finding new efficiencies while also managing through the need to work remotely.”
Barr also touched on how L2L was built for this type of environment. L2L was born a decade ago during the Great Recession and the L2L team has worked remotely since its inception. The need for manufacturers to do “more with less,” find efficiencies, and continuously improve, is why L2L’s LES platform exists.
Worthington Industries
Worthington Industries, one of two 2020 L2L Operational Excellence Award recipients (Award highlights video for Worthington), led off the morning session of manufacturing presenters by describing their process for deploying the LES platform at a new plant every three months. This was possible by having a solid plan for systems integration.
Justin Skaggs and Ben Neal, Delivery Lead and Transformation Manager for Worthington, revealed their step by step procedure including which systems they integrated, how they did it, and how that helped them succeed. They maintained an emphasis on keeping things simple and building on the process over time while soliciting input from everyone involved.
A key theme that was woven into their approach to systems integration was the culture they've built: a culture of empowering people to act on solving problems.
Although for the more technical IT pro, it’s straightforward and packed with insights.
Key advice from Worthington Industries:
- Take an agile approach to integration by moving quickly but taking small steps. Keeping it simple is key.
See full Worthington presentation here
ADAC Automotive
Next up was ADAC Automotive who opened with their story of how they transformed their data collection from the use of Excel and Paper to a digitized and automated system. The velocity of this transition was possible through a focus on documentation and getting their entire team on-board for the update.
Chase DeGlopper, Advanced Manufacturing Systems Analyst for ADAC, focused heavily throughout the presentation on the need to document the process and use that as your standard to continuously improve moving forward. DeGlopper emphasized the ROI from enabling team leaders to work with engineers and quickly resolve issues.
Key advice from ADAC Automotive:
- Deploying a system for real-time data collection and analysis can seem like a daunting task, but with proper documentation and alignment of people, it will show great benefits in the end.
- An automated, real-time data system is paramount to more quickly address and solve problems.
See full ADAC presentation here
Petersen Inc.
Rounding out the first half of the summit was Petersen Inc. who described their operations, including over 50% one-off jobs such as large cylindrical parts of Disney’s Star Wars land rides and equipment for nuclear treatment facilities.
Chad Peterson, Process Improvement Specialist for Petersen, discussed Petersen Inc.’s need for quality response and dispatching. In their facility, the main issue was the response time for inspectors to check quality on weld jobs which resulted in wasted time and backlogs.
Peterson formed a cross-functional team to find and implement a cloud-based dispatch system (CloudDISPATCH), which to date has enabled them to cut response times by 40%-70% for quality inspectors in different scenarios.
Key advice from Petersen Inc:
- The value of data is harvested through the ability to easily access and understand it, and then to use it as a guide for solving your unique problems.
- Start wherever you are (your unique problems to solve) and work forward from there. Don't get hung up on your company being so different that the solution has to be totally different.
See full Petersen Inc presentation here
Purple
Purple Innovation, the second recipient of the 2020 L2L Operational Excellence Award, (Award highlights video for Purple) started off the second half of the summit by describing what it took to build maintenance operations from scratch. This blank slate, although challenging, allowed Maintenance Director Phil Galata to set up optimal systems and processes without the baggage of what might have been in place before.
This included starting off with a real-time maintenance management solution that would allow them to not only manage, but also continually improve their maintenance activities. While describing their transition to an electronic data storage system, Galata stressed the importance of making transparent goals and having great communication with your team as you develop a new system. Similarly, Phil covered the need to have healthy relationships with everyone using the system and allow for feedback as the system evolves and improves.
Key advice from Purple:
- Make your goals transparent and communicate them well
- Keep communication open and allow for constant feedback from your team: it's key to continually getting better.
- Each time an issue arises, ask yourself, “How can L2L help solve this problem?" It's designed to manage the different issues that arise throughout a plant on a daily basis.
See full Purple presentation here
Veoneer
Rounding out the guest speakers for the summit was Veoneer who presented an amazing data-driven walk-through of their integration between L2L and Power BI and how it makes data both accessible and actionable.
Paul Ciorgovean, Business Systems Analyst, showed all attendees of the summit the power of data when displayed in a way that is understandable to team-leaders and management. The alternative, "data overload" (the more data you have the more confusion you have), leaves the company unable to do anything about it.
Ciorgovean then illustrated how "having visibility is not what solved the problems, it was taking action based on the visibility."
Key advice from Veoneer:
- Focus on the data you can control.
- Provide teams a way to see the big picture, and then drill down to the specifics to understand issues as well.
- Enable teams to filter data at their own pace, and then empower them to act on it.
- The combination of Power BI and L2L's LES allowed Veoneer to visualize large quantities of data, make sense of it, act on it, and close the loop on achieving improved results.
See full Veoneer presentation here
Project Management Module Announcement
Wrapping up the conference, Tyler Whitaker - CTO and Devin Baldwin - Product Manager of L2L, shared the exciting release of L2L's new Project Management module. [hyperlink the module's title to the left to the module page once finished]
Also, among the many new enhancements coming in the near future, is the ability to integrate communication software such as Slack and Skype with your L2L system to make communication easier and more fluid than ever.
In Conclusion
In conclusion, although a different format, pivoting to an online event proved to be just as successful as past in-person summits. The excitement was palpable, engagement was high, and actionable takeaways were derived from each and every presenter.
We look forward to another outstanding L2L Summit in 2021, and once again, thank you to each presenter, and congratulations to the 2020 L2L OpEx Award recipients!
Revisions
Original version: 18 July 2024
Written by: Evelyn DuJack
Reviewed by: Daan Assen
Please read our editorial process for more information
Subscribe to Our Blog
We won't spam you, we promise. Only informative stuff about manufacturing, that's all.