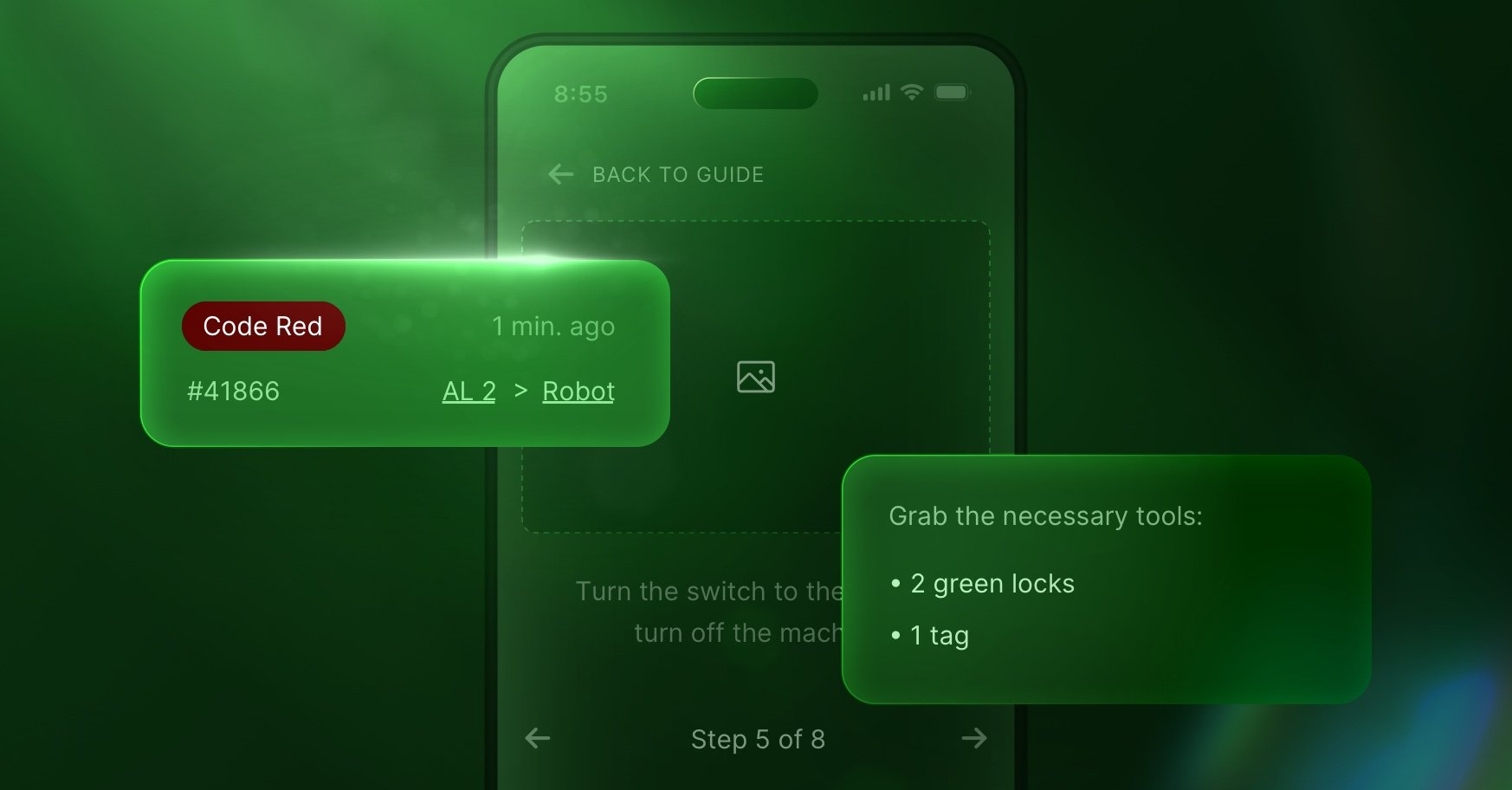
Staying competitive as a manufacturer requires more than just hard work; it demands smart work.
Amid labor shortages, increased automation, complex machinery, and relentless pressure to improve efficiency, industrial companies are constantly searching for ways to improve productivity without compromising quality.
The challenges are real
Manufacturers are grappling with several critical challenges:
- Skills gaps and knowledge loss: Experienced workers are retiring, taking vital knowledge with them. In fact, 84% of manufacturing leaders have seen this exodus hurt every area of their operations (LNS, 2024).
- Difficulty maintaining consistent quality: Increased product variety and customization lead to higher error rates.
- Pressure to increase efficiency and reduce costs: Global competition demands streamlined processes and reduced waste.
- Challenges in onboarding and training: High turnover requires rapid and effective training solutions.
- Safety concerns: Complex machinery and evolving processes demand robust safety protocols.
Traditional, paper-based work instructions and siloed digital systems are inefficient, prone to errors, and hinder productivity. Simply put, they can't keep up with production demands, and these legacy systems put excess strain on frontline workers.
The solution: Visual and mobile digital work instructions
Imagine a world where your frontline workers have instant access to clear, visual, and standardized work instructions right within their L2L Dispatch screen.
Our new digital work instruction capabilities transform how work is done on the shop floor by providing step-by-step guidance, multimedia support, and real-time updates.
How digital instructions work
Utilizing digital work instructions in L2L is easy. Digital instructions can be accessed from right within a Dispatch, or within the Operator Console.
For example, if a Changeover Dispatch comes in, simply navigate to the documents section and identify the digital instruction link.
This link will open a visual work instruction to guide you through the task. Instructions will showcase an image or GIF for each step, paired with written instructions so you can easily follow the instructions.
Once you complete the task, you can provide feedback to further improve the instructions. And that’s it! Quickly resolve incoming Dispatches and address tasks more accurately with digital instructions.
Click through the interactive demo to see it in action!
Key benefits that drive results
- Addressing the skills gap: Visual work instructions capture and preserve institutional knowledge, accelerating training and ensuring consistent performance. We've seen a potential 50% reduction in training time.
- Maintaining quality and meeting customization demands: Clear, standard instructions minimize errors, leading to a potential 67% reduction in product errors and a +39% increase in first-time right.
- Increasing efficiency and reducing costs: Standard procedures, streamlined workflows, and reduced rework translate to a potential +20% faster task completion and improved profitability.
- Streamlining onboarding and training: Rapid learning and reduced reliance on trainers lead to faster proficiency. Lower labor costs can mean -33% changeover time with support for 52+ languages.
- Improving safety: Clear safety protocols and hazard identification minimize accidents, creating a safer work environment.
Heineken's adoption of digital instructions has revolutionized their operational efficiency. By providing frontline workers with instant access to digital standards and job aids, they:
- Achieved a 50% reduction in training and onboarding time
- Decreased in batch recalls by 67%
- Improved key Operational Performance Indicators (OPI), CLT Standards, and 5S due to better access to operational knowledge
A day in the life:
7 AM - Daily Safety Protocol: From the Operator Console in L2L, an Operator is able to access their Daily Safety Check documentation for their line. They follow the steps according to best practices and confirm they are following the required safety procedures as the day begins.
12 PM - Swift Changeover: It’s time for a changeover. A Dispatch is assigned to the Operator, and they follow the guided step-by-step instructions on their tablet. Digital instructions with visuals replace cumbersome binders, making the process quick and clear. The changeover is completed quickly, with minimal downtime.
2 PM - Tackling a Maintenance Issue: A machine starts exhibiting a slight vibration. The Operator sends out a Dispatch, and a Technician comes to resolve the issue. L2L provides a suggested fix, and they utilize the appropriate instruction set to resolve the issue. The machine is back up!
3:45 PM - Confident and Prepared for Tomorrow: As the Operator’s shift nears its end, they feel a sense of accomplishment. The digital work instructions have not only made tasks more efficient, but they have also increased the new Operator’s confidence.
They know they have access to the information they need, exactly when they need it, right within their workflow.
Digital instructions aren’t just about following instructions; they're about empowering frontline workers.
Digital work instructions = quantifiable results
We're not just promising improvements; we're delivering measurable results:
- +20% OEE
- +34% S5 improvement
- -33% Changeover time
- +11% OPI
Ready to transform your frontline?
Don't let outdated processes hold you back. Embrace the power of integrated digital work instructions and upgrade to unlock the full potential of your workforce.
Schedule a demo to learn how L2L's new digital work instruction capabilities can help you achieve operational excellence.
Revisions
Original version: 18 April 2025
Written by: Robin Lis
Reviewed by: Evelyn DuJack
Please read our editorial process for more information
Subscribe to Our Blog
We won't spam you, we promise. Only informative stuff about manufacturing, that's all.