Unify your operations
Trusted by global manufacturing leaders
Your connected operations hub
See how L2L brings your maintenance, production, quality, and workforce tools into one unified system—so you can drive improvement across every part of your operation.
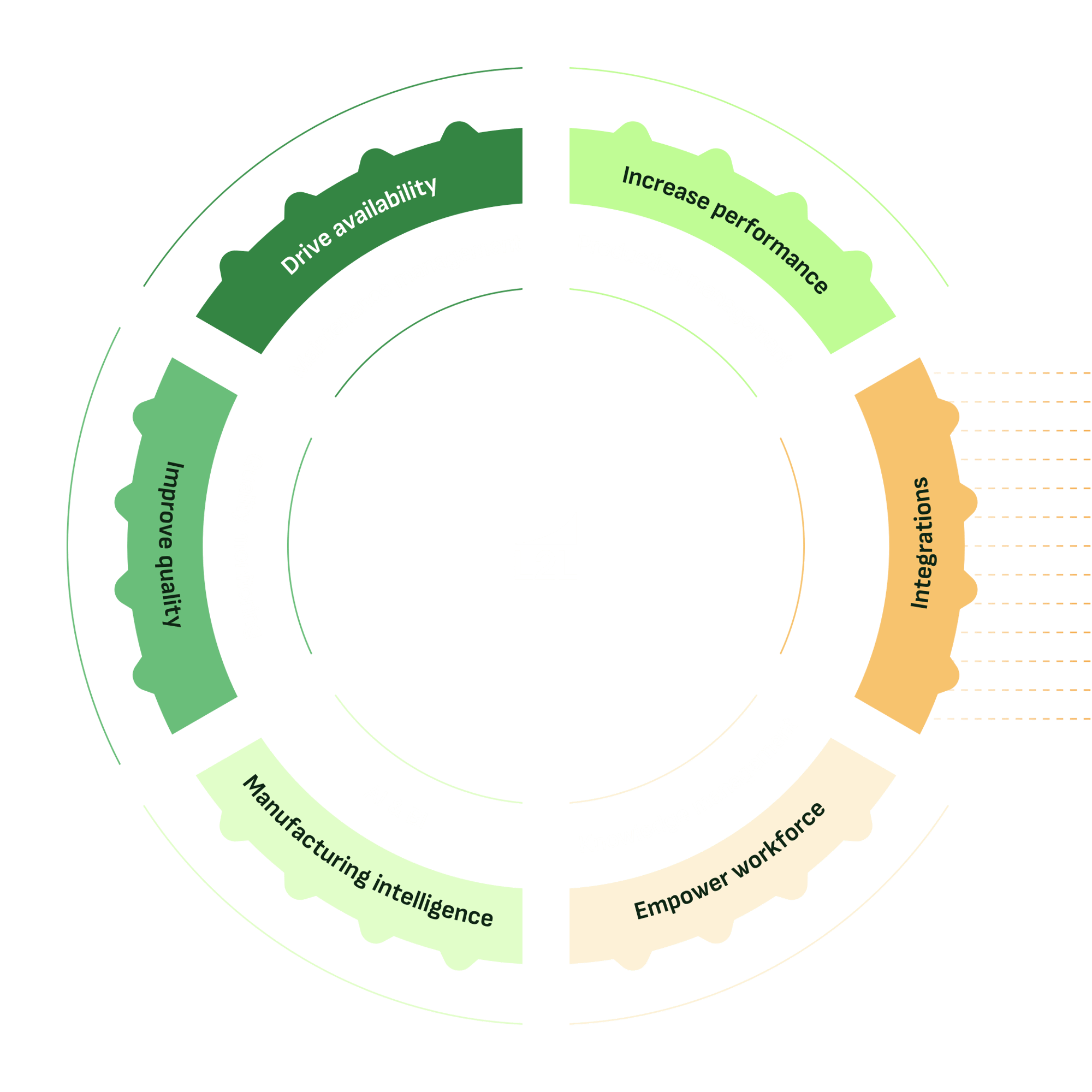
Production management
Manage production schedules, track OEE, and utilize real-time data to drive improvements. With comprehensive visibility into operations, you can make informed decisions and optimize your operations.
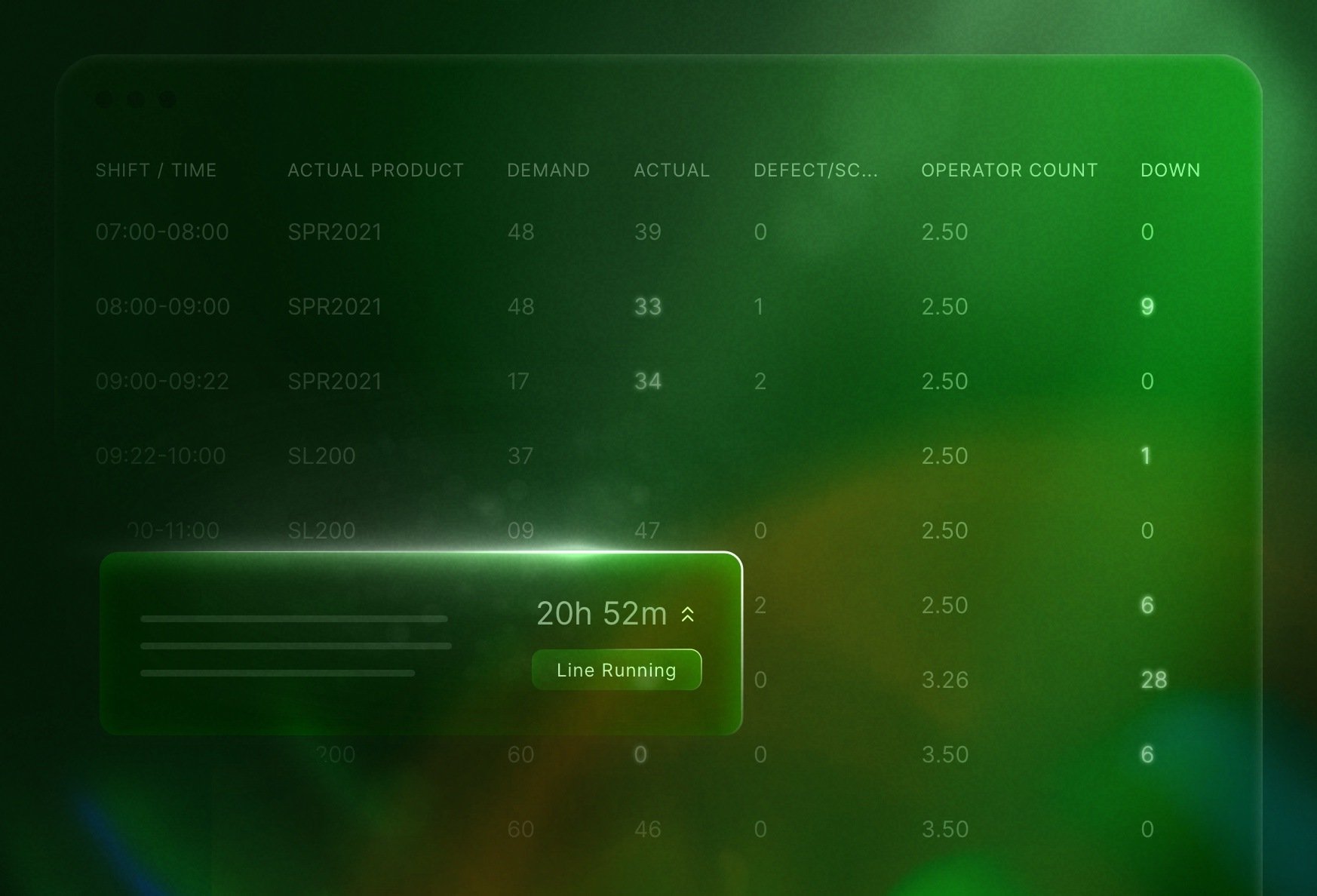
Quality management
Enlist your entire shop floor to reduce scrap, eliminate defects, and boost quality. Spot anomalies in real time with in-process inspections, quality monitoring, and root cause analysis.
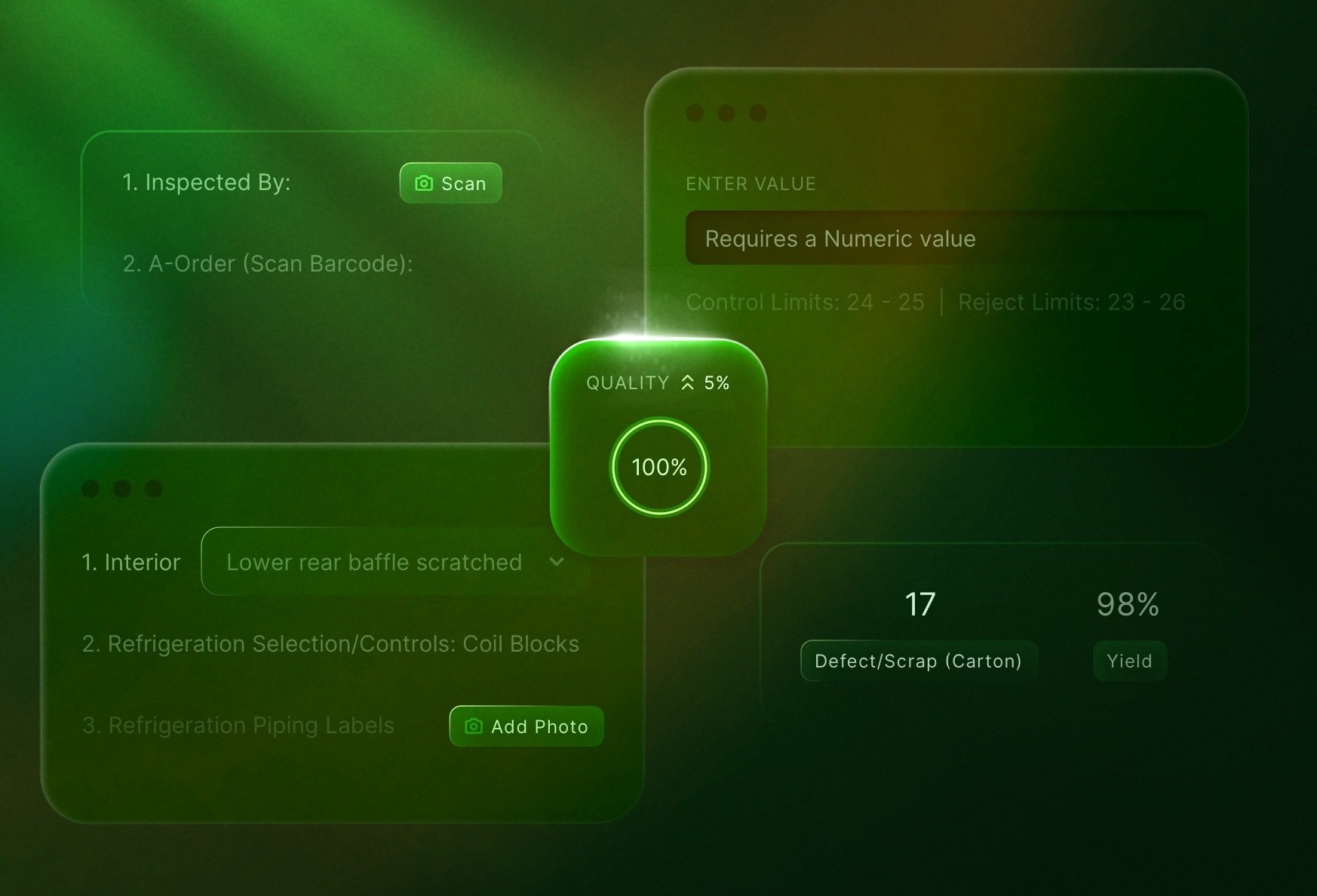
Maintenance management
Manage work orders, plan preventive maintenance around production schedules, manage spares, and track downtime to ensure assets are always optimized and running reliably.
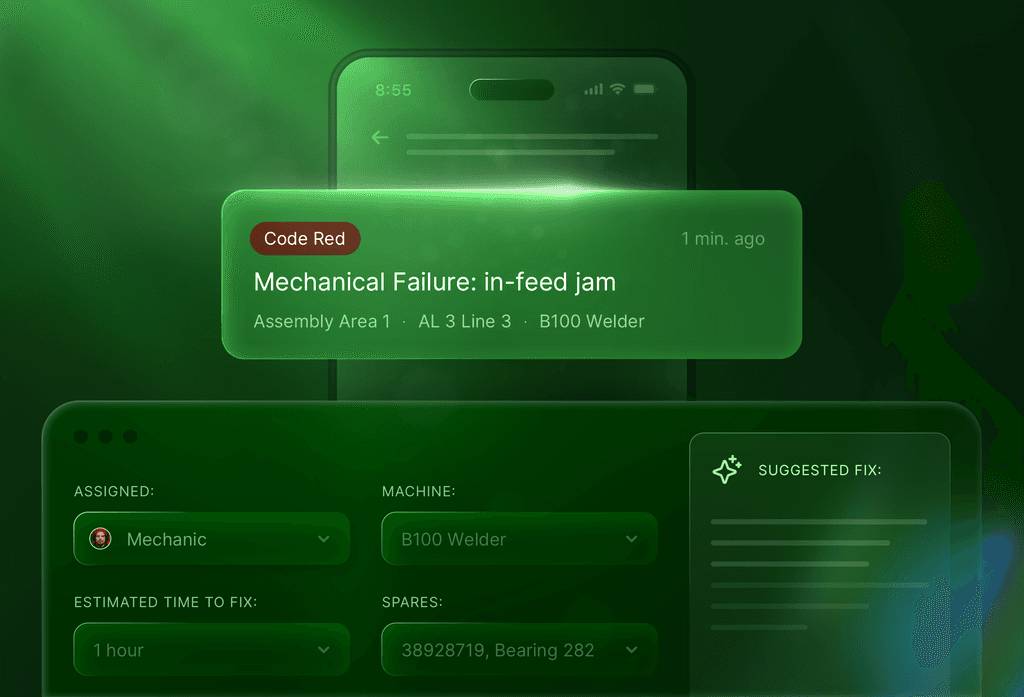
Frontline training and knowledge
Retain talent and accelerate productivity with clear, standardized mobile work instructions. Upskill and engage your global workforce with practical, comprehensive training initiatives available in over 50 languages, ensuring operations are safe and standardized.
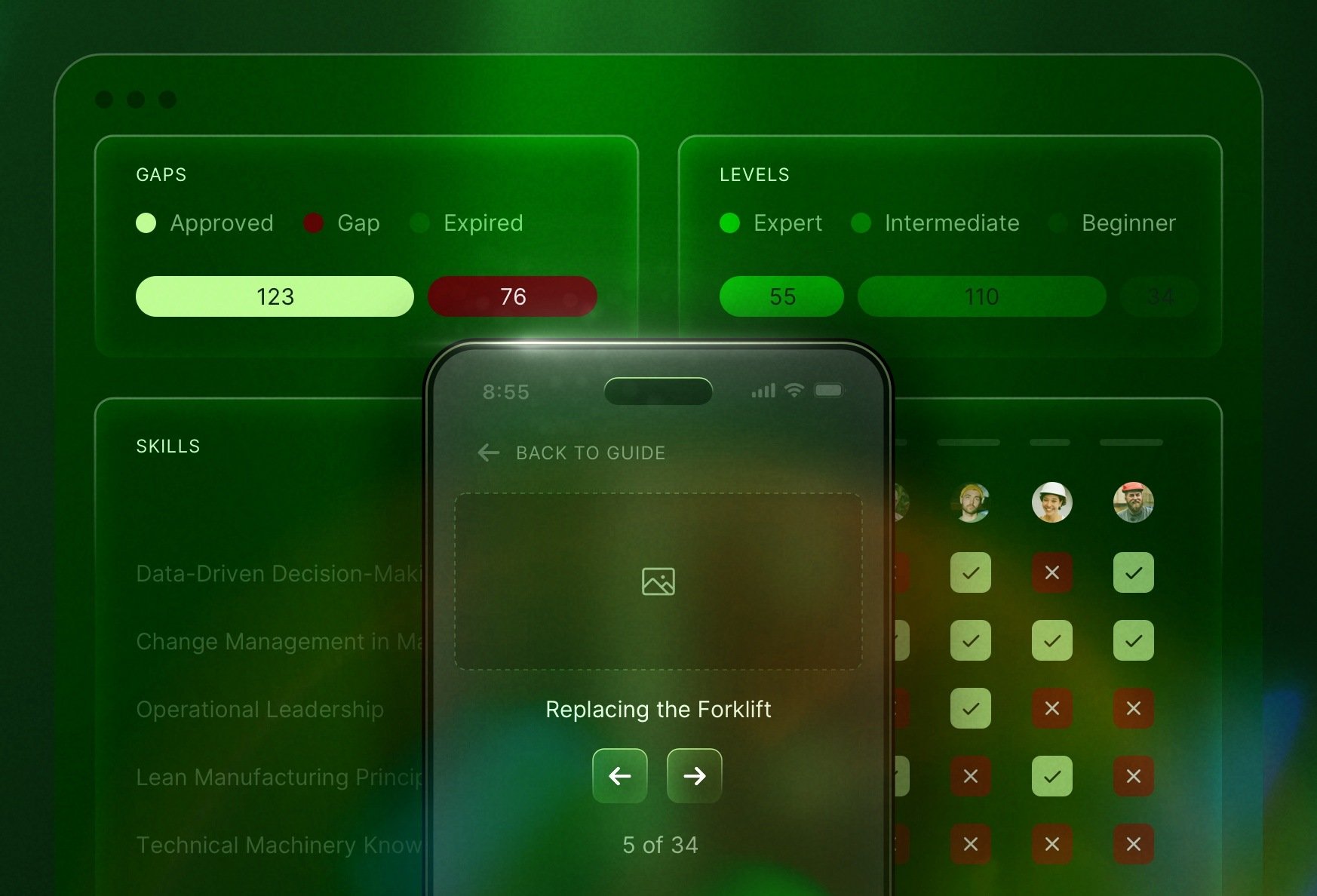
Focus on the problems that matter
Surpass your manufacturing goals across availability, performance, quality, and workforce. Say hello to the future of connected work.
-
Plant and operations leadersDrive continuous improvement.
-
Frontline teamsManufacture better, together.
-
Executive leadersStop making decisions in a vacuum.
-
IT leadersRapid implementation and value.
Connect data to action with AI and BI to identify bottlenecks, optimize resources, and drive continuous improvement.
Supervisors and managers gain essential tools—task management, skills tracking, and predictive analytics—to maximize productivity across all lines and operations.
Empower operators, technicians, and material handlers with clear task management connected to actionable checklists and work instructions in their own language.
Better knowledge management means real-time collaboration to prioritize and track work while driving action.
Improve engagement and retention by training and upskilling your teams with intuitive skills management and learning activities.
L2L helps you benchmark and measure the effectiveness of your operations across the entire organization.
Make informed decisions about utilization and effortlessly standardize and scale best practices across every line, business unit, and plant.
L2L delivers rapid time to value with no rip-and-replace. Standard implementation is 14 to 60 days, and you’ll experience value immediately. Our platform is simple and intuitive—we’re here to drive productivity across your user base.
-
Plant and operations leadersDrive continuous improvement.
Connect data to action with AI and BI to identify bottlenecks, optimize resources, and drive continuous improvement.
Supervisors and managers gain essential tools—task management, skills tracking, and predictive analytics—to maximize productivity across all lines and operations.
-
Frontline teamsManufacture better, together.
Empower operators, technicians, and material handlers with clear task management connected to actionable checklists and work instructions in their own language.
Better knowledge management means real-time collaboration to prioritize and track work while driving action.
Improve engagement and retention by training and upskilling your teams with intuitive skills management and learning activities.
-
Executive leadersStop making decisions in a vacuum.
L2L helps you benchmark and measure the effectiveness of your operations across the entire organization.
Make informed decisions about utilization and effortlessly standardize and scale best practices across every line, business unit, and plant.
-
IT leadersRapid implementation and value.
L2L delivers rapid time to value with no rip-and-replace. Standard implementation is 14 to 60 days, and you’ll experience value immediately. Our platform is simple and intuitive—we’re here to drive productivity across your user base.