West Liberty Foods Saves $2 Million in Maintenance Costs
West Liberty Foods, headquartered in West Liberty, Iowa, is a recognized leader in the food industry and one of North America's top protein processors.
With L2L, the West Liberty team has:
-> Shifted into proactive maintenance initiatives
-> Increased visibility into plant operations and improved operational availability (OA)
-> Seen significant cost savings utilizing actionable data
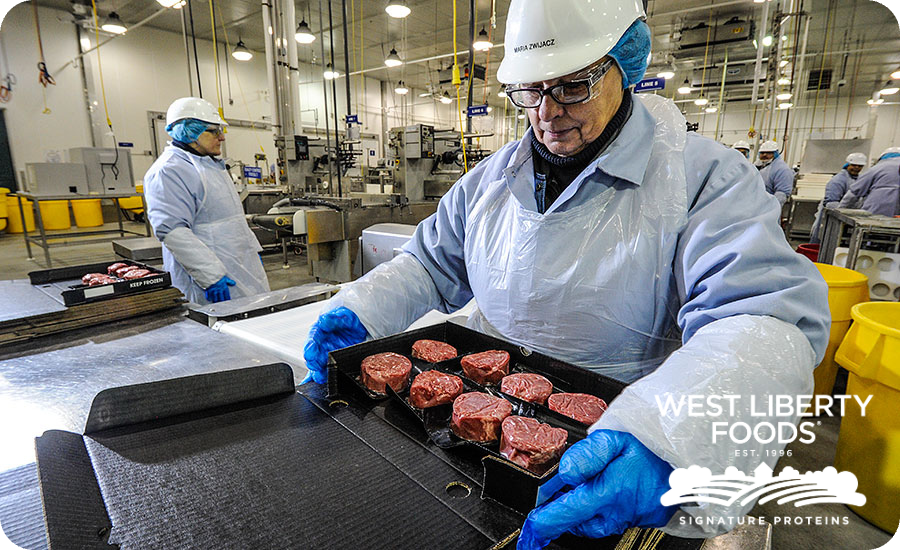
West Liberty x L2L achievements
Made for manufacturing
"We've seen an increase of over 10% machine uptime, that is attributed to having that visibility of preventive maintenance, work orders, and reactionary maintenance."
- Chad Williams, Corporate Maintenance Manager
Visibility into plant operations
West Liberty Foods implemented L2L to give maintenance teams and leadership unprecedented visibility into plant operations.
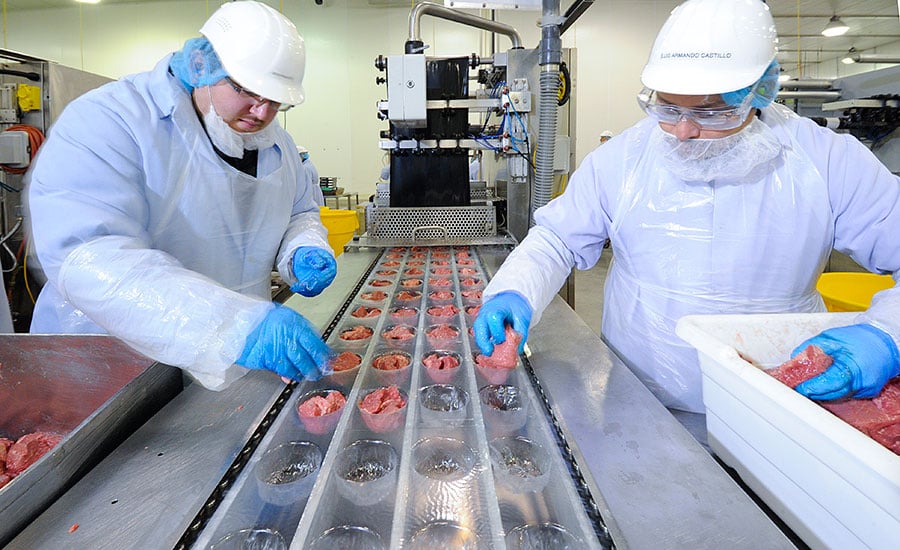
Before

Plant teams were diligent in taking notes and properly inputting data into their existing operations system, but technicians had difficulty finding and analyzing data. IT support was required to create any reports.
Now
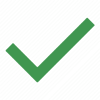
Everyone has real-time visibility into plant activities, allowing teams to quickly identify and address the root cause of problems as they arise.

L2L helps our maintenance teams maintain a world-class standard. Everyone has real-time visibility into what’s happening at our plant. If we have a problem, we can quickly get to the root cause of it.
Resource optimization
L2L helped West Liberty Foods dramatically improve maintenance resource utilization.
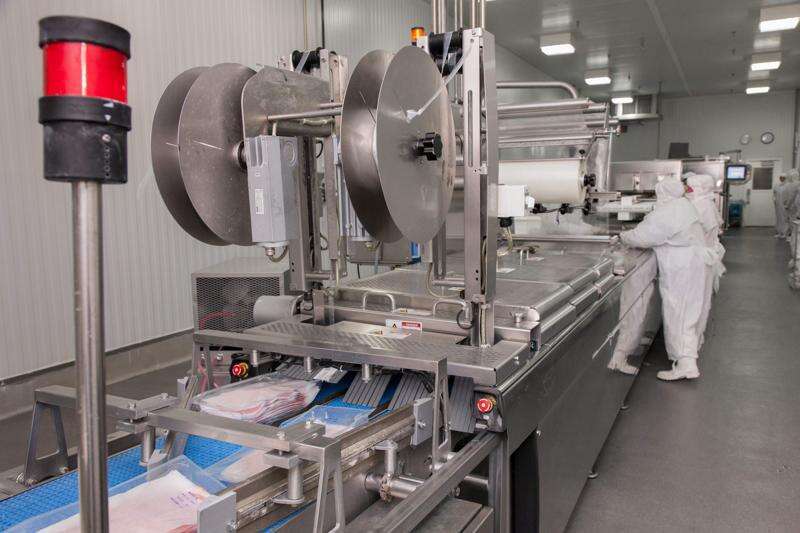
Before

Between recording information and running reports, it could take three to five days before the team really knew what was happening in the plant. With manual line and machine downtime data entry, important information got lost or wasn't recorded at all.
Now
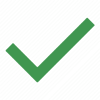
West Liberty Foods has improved its resource/workforce utilization by 88.5%. A real-time view of data helps the company identify and act on opportunities to improve efficiency in every area of the plant floor.

L2L has not only saved us money, but it has also improved our processes and made us more productive with the resources we have.
Machine uptime improvement
Through L2L implementation, West Liberty Foods achieved significant improvements in machine availability and uptime.
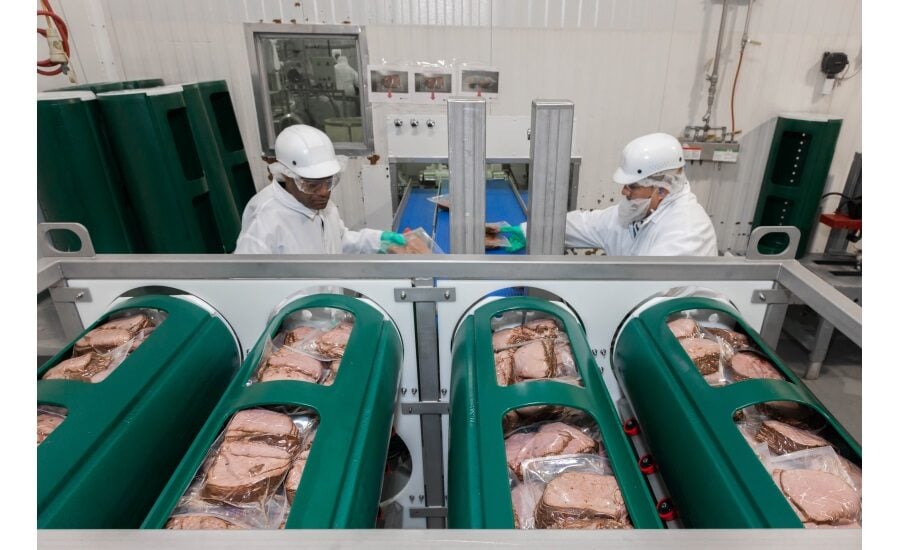
Before

Without proper tracking and visibility into machine performance, the company struggled to maintain optimal OA across production equipment.
Now
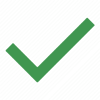
When West Liberty Foods deployed L2L at their first facility, machine uptime (OA) was 86.6%. After two years, the same facility led the company at 96.6%, a 10% improvement.
Cost reduction through data analytics
L2L helped West Liberty Foods gain insights into their maintenance spending patterns and reduce costs significantly.
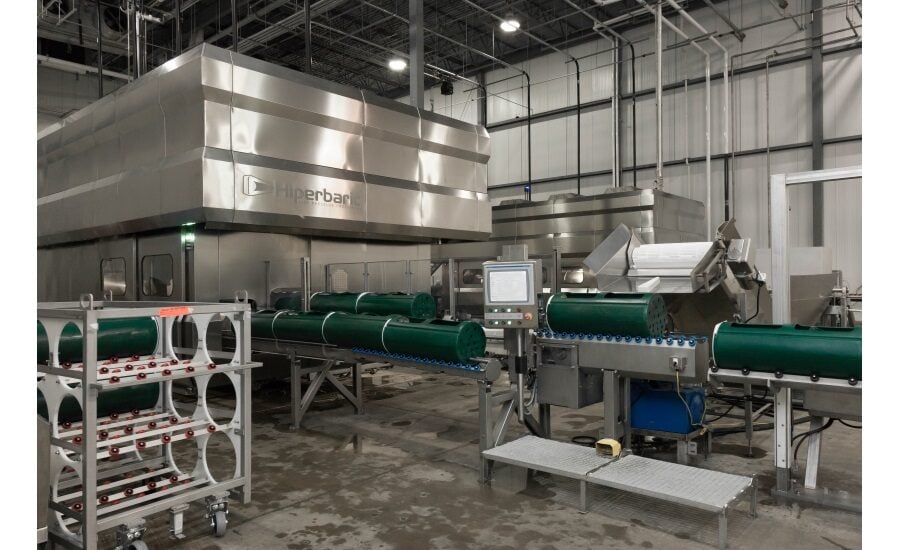
Before

The maintenance team was stuck in reactive mode, always responding to the same equipment failures. The lack of data meant they couldn’t find and fix the root problem.
Now
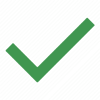
Deploying L2L helped West Liberty Foods pinpoint ongoing machine abnormalities occur—saving the company $2 million in maintenance costs. Because L2L maintains digital records of abnormality trends and resolutions, technicians can easily access machine history in a highly regulated manufacturing environment.
Regulatory compliance management
L2L provided West Liberty Foods with tools to effectively manage compliance with industry regulations.
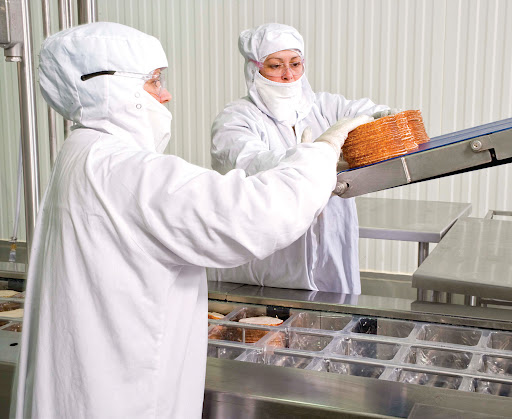
Before

The company needed to ensure compliance with USDA requirements while maintaining efficient operations, but it lacked streamlined processes to do so.
Now
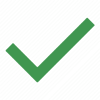
By affording West Liberty Foods greater visibility into its processes, L2L has helped the company streamline and simplify compliance with USDA regulations and other important guidelines.
The return on investment
Maintenance cost savings
$2 million saved in maintenance costs
Resource utilization ↑
88.5% improvement in resource utilization
Operational availability ↑
96.6% OA achieved within 2 years
Improved company culture
Compliance ↑
Better tracking
The solution that shows your manufacturing problems—and fixes them too
Drive continuous improvement in availability, performance, quality, and workforce enablement.
Quickly identify problems and take action faster with L2L. Empower your teams to achieve daily wins and drive success every day.
Trusted by leading sites around the globe.