Purple Reduces Equipment Downtime by 54%
Purple is a leading comfort technology company that designs and manufactures innovative products to improve how people sleep, sit, and stand.
Since implementing L2L, Purple has:
-> Dramatically reduced equipment downtime
-> Exponentially increased preventive maintenance completion
-> Improved on-time completion of maintenance events
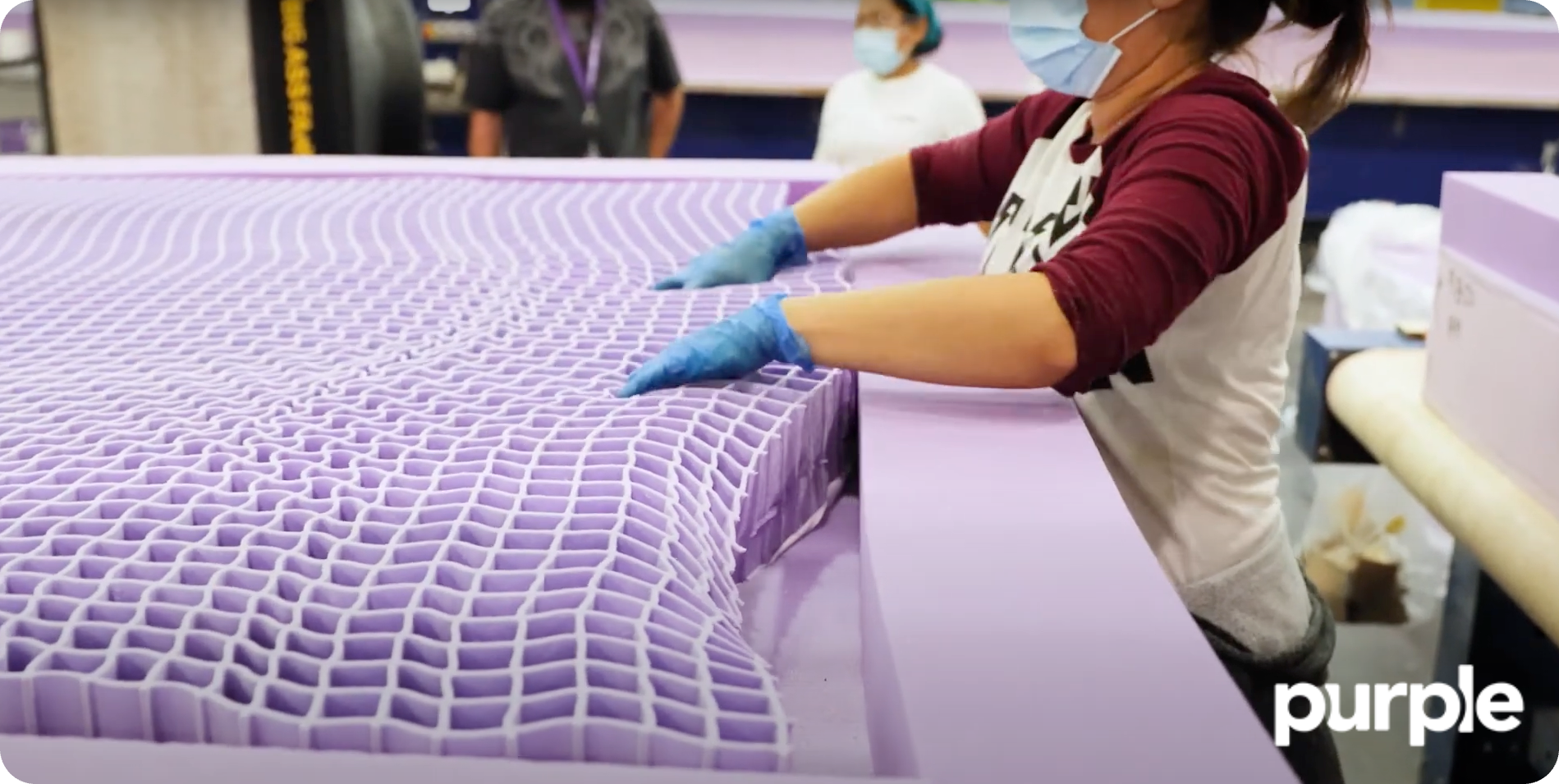
Purple x L2L achievements
Access to actionable data
"What specifically makes it successful is the ability to track data, look at the data, and then establish goals to improve from there."
- Dallin Johnson, Planning Scheduling Supervisor
Real-time visibility into production operations
Purple implemented L2L to give maintenance teams and leadership unprecedented visibility into plant operations.
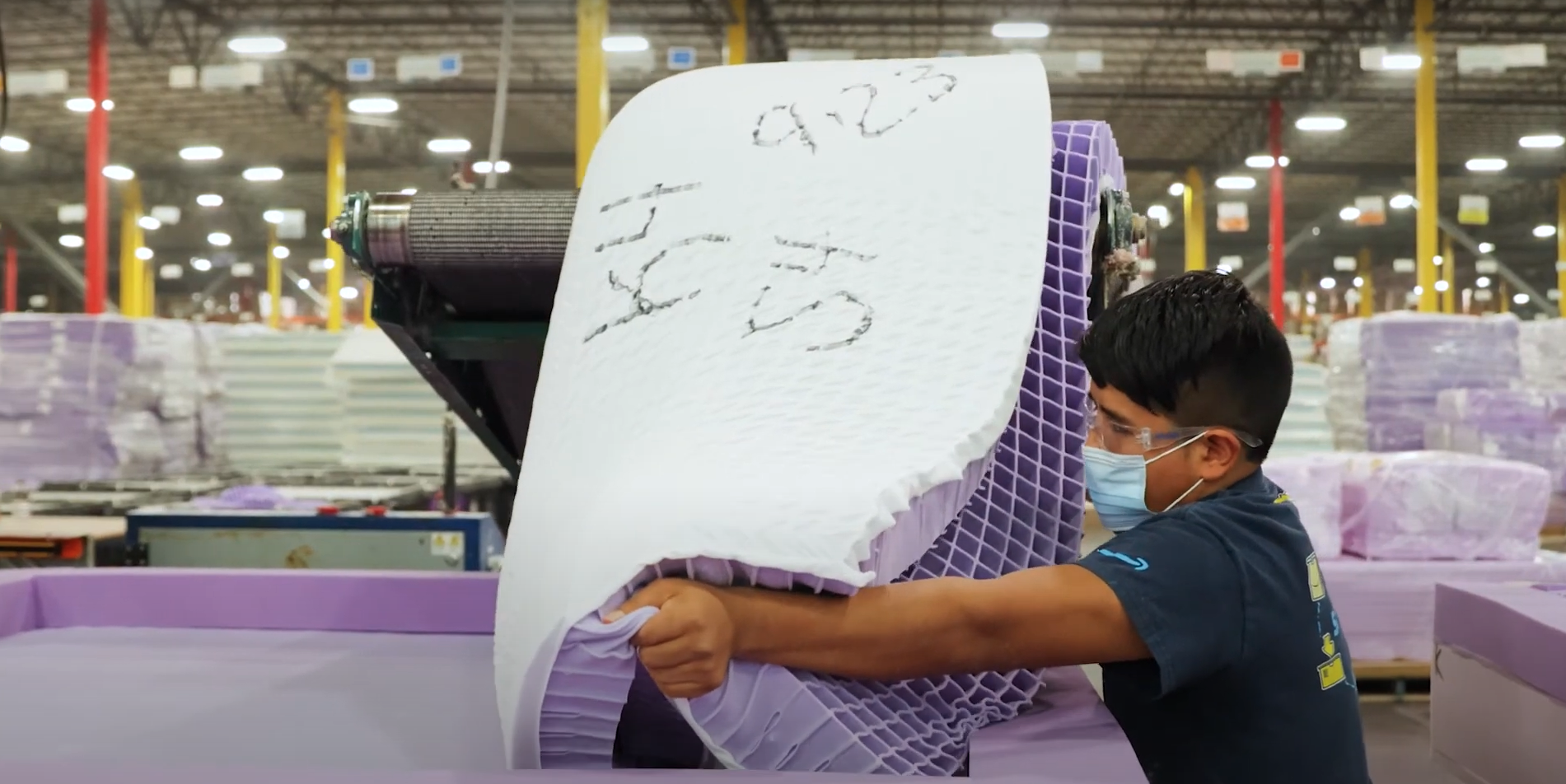
Before

Purple knew that without a best-in-class maintenance and operations management system, downtime and other disruptors would be an ever-present danger.
Now
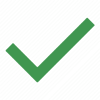
After L2L integration for the maintenance and production staff, the Purple team started seeing immediate results at their Grantsville, Utah, plant. With real-time data, Purple can identify and quickly fix any equipment problems, allowing it to drive continuous improvement.

The implementation was extremely fast. L2L had every step of the process handled at an incredible pace and truly provided a solution that helped our team understand why and what this platform meant for them. This sets them apart.
Proactive maintenance transformation
L2L helped Purple transform from reactive to proactive maintenance practices.
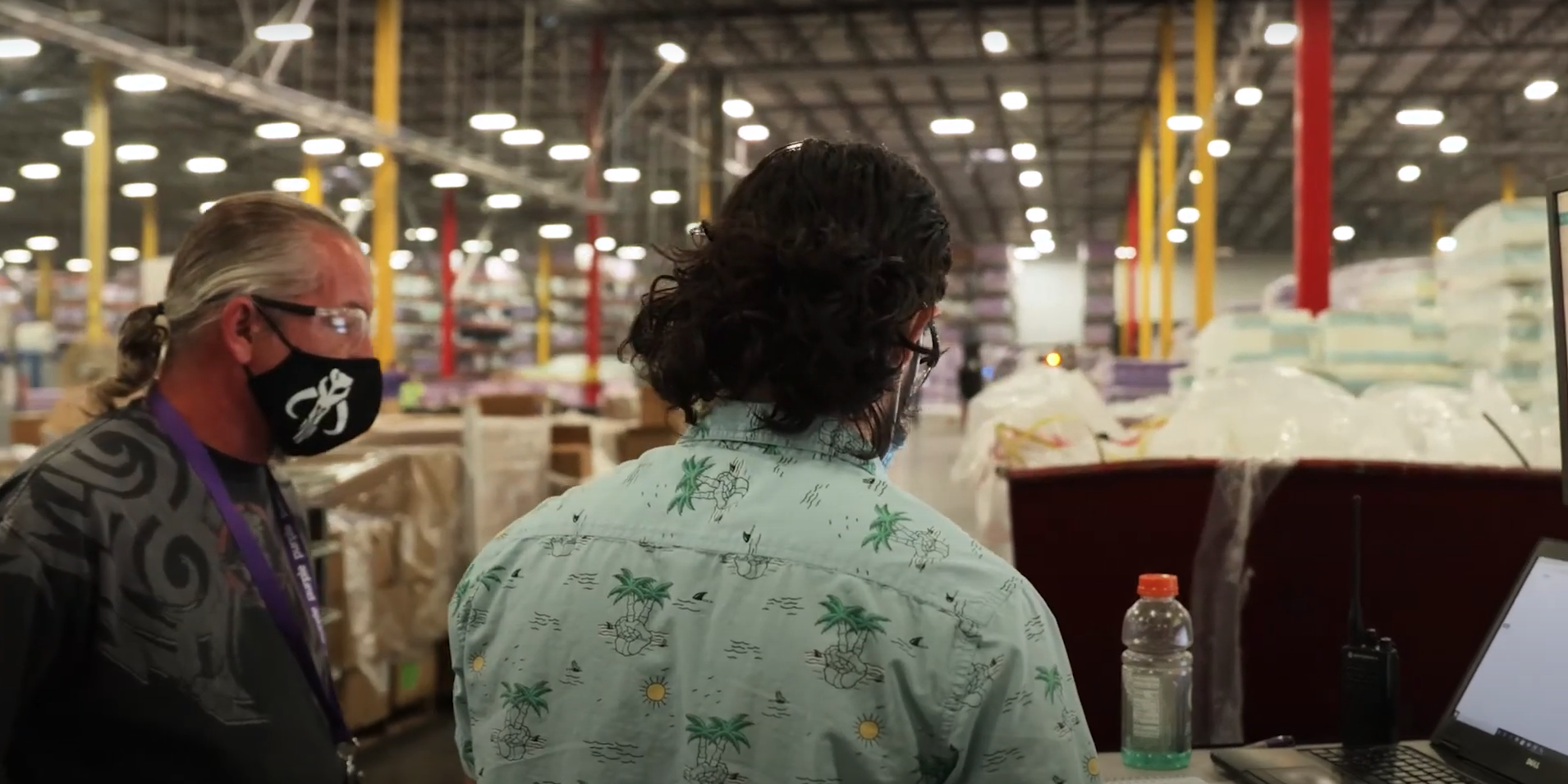
Before

The team needed a modern CMMS solution that would help keep production lines moving, but had limited visibility into maintenance needs and equipment performance.
Now
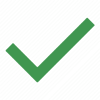
L2L allows the maintenance team to quickly launch the planning and scheduling of preventative maintenance functions that are traditionally manual processes. L2L also provides real-time performance data that Purple uses to spot and respond to issues in the plant.

When we first looked at L2L, it seemed like such a sensible and versatile bolt-on to take us to the next level of managing processes.
Equipment reliability improvement
Through L2L implementation, Purple achieved significant improvements in equipment reliability and uptime.

Before

Purple was dealing with frequent equipment failures that disrupted production flow and impacted output.
Now
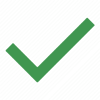
After implementing L2L, Purple reduced equipment failures by 52% and equipment downtime by 54%, creating much more reliable production processes.
Preventive maintenance optimization
L2L helped Purple dramatically increase both the quantity and the timely completion of preventive maintenance.
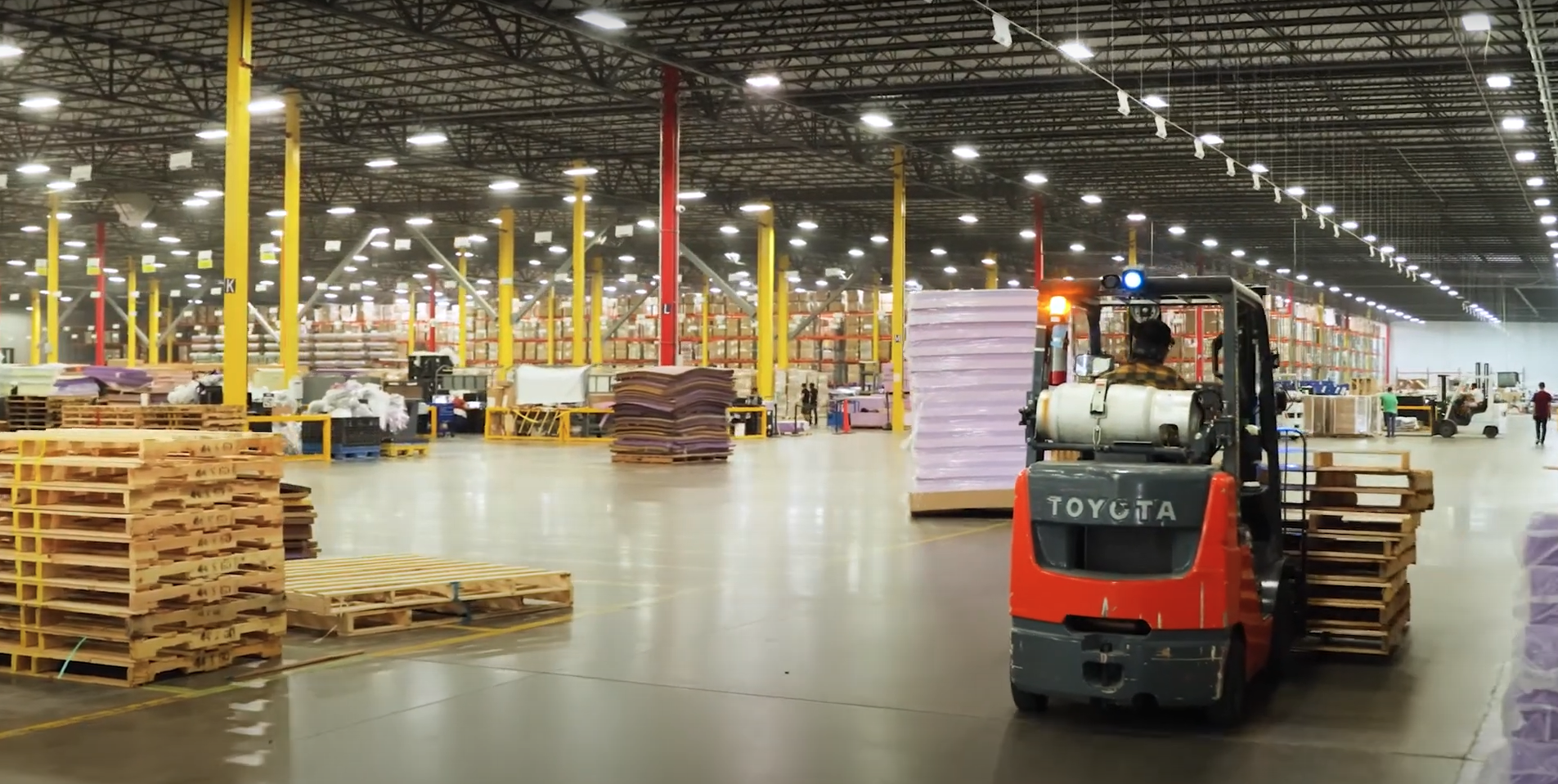
Before

The maintenance team struggled to complete preventive maintenance tasks on schedule, often getting pulled into reactive work.
Now
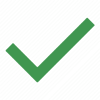
Purple has seen a 1,400% increase in completed preventive maintenance events and a 42% increase in on-time completion of those events, creating a much more proactive maintenance culture.
The return on investment
Downtime ↓
54% reduction in equipment downtime
Equipment failures ↓
52% reduction in equipment failures
Preventive maintenance ↑
1,400% increase in completed preventive maintenance events
On-time preventive maintenance ↑
Team understanding
Better team understanding of maintenance processes
Continuous improvement
Continuous improvement cycles in production operations
The solution that shows your manufacturing problems—and fixes them too
Drive continuous improvement in availability, performance, quality, and workforce enablement.
Quickly identify problems and take action faster with L2L. Empower your teams to achieve daily wins and drive success every day.
Trusted by leading sites around the globe.