How Dart Container Transformed their Operations
Dart Container is a leading manufacturer of consumer and retail food and beverage containers, including clear plastic cups, foam cups, to-go dish containers, and the iconic Red Solo Cup.
With L2L, Dart Container has seen:
-> Double-digit percentage increases in efficiency
-> Record-breaking production numbers
-> Faster issue resolution
-> Reduced downtime
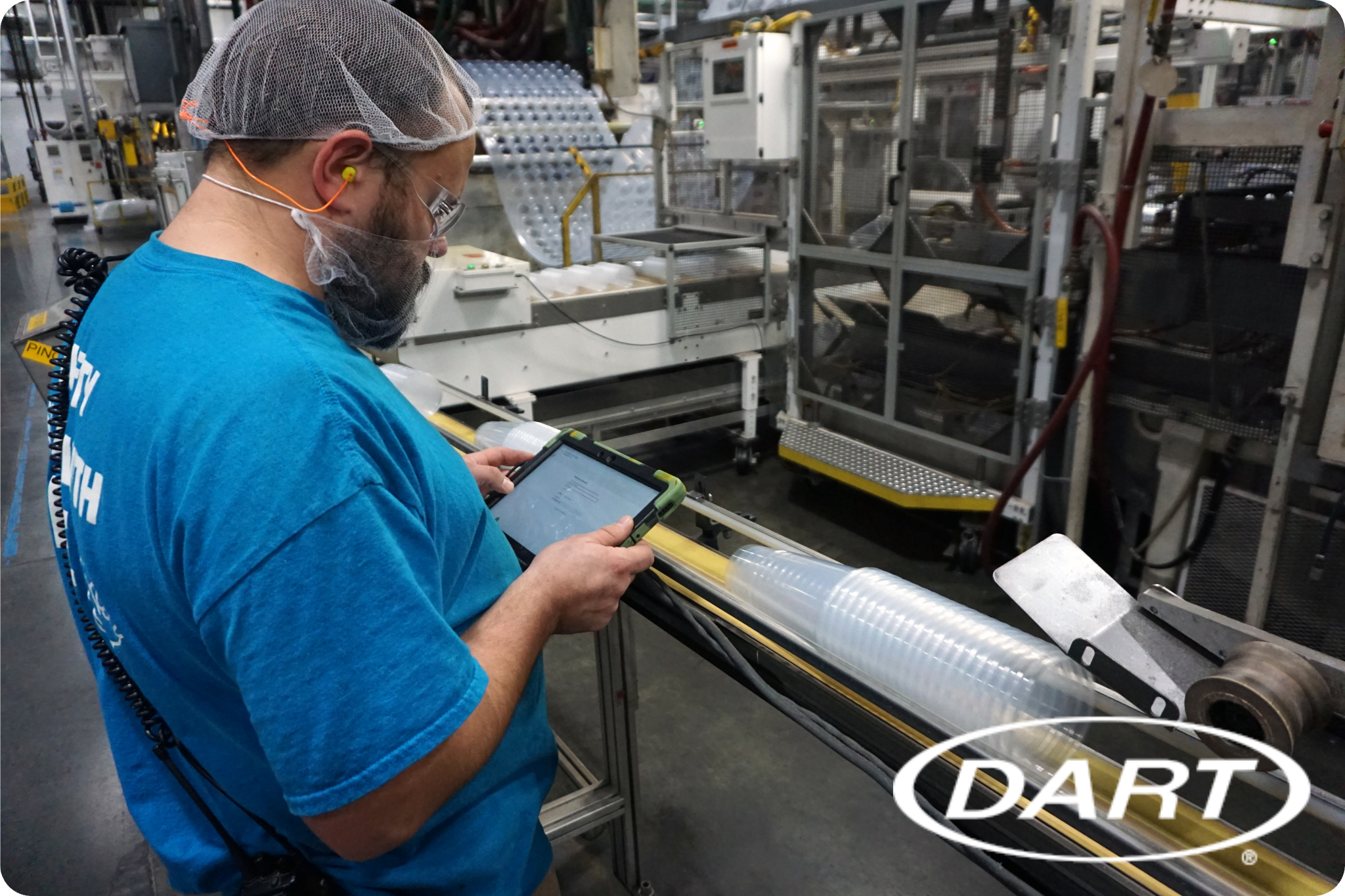
Increased efficiency
"We all have our fingers on the pulse of the production floor, now. I can say definitively that we've seen double-digit percentage increases on deficiencies. L2L has been big for connecting the dots."
- Connor Cox, Process Engineer
Digital transformation
Dart implemented L2L's comprehensive digital manufacturing platform to replace outdated, paper-based systems. This gives employees immediate access to live production data through tablets, monitors, and mobile devices from anywhere in the plant.
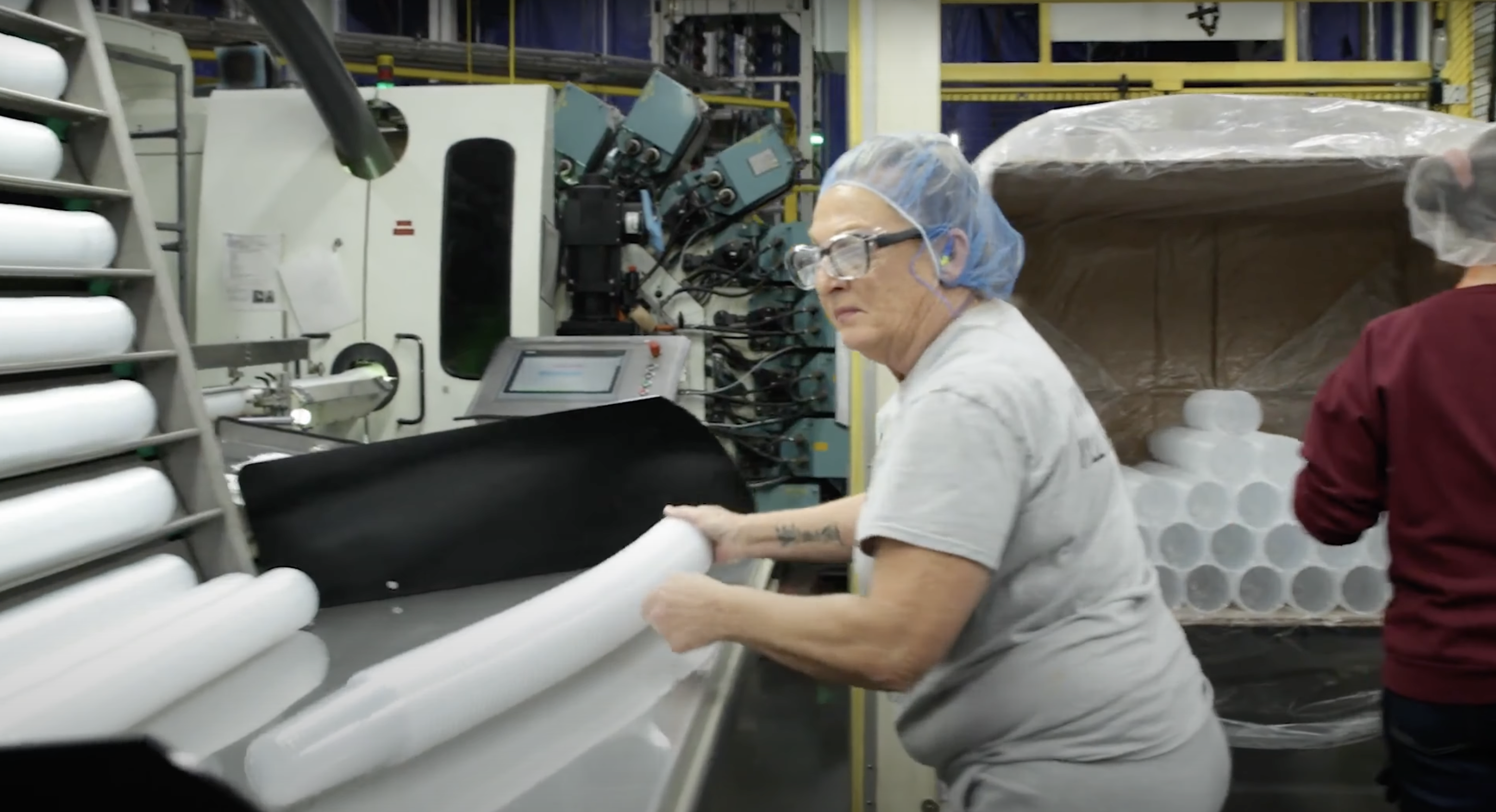
Before

Dart relied on dry-erase whiteboards to record critical production data, resulting in lost information and incomplete records.
Now
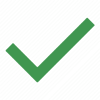

Now with L2L, we have the ability to see live data. There's so much available at your hands, readily. It's incredible.
Connected workforce
L2L connects maintenance and production teams, allowing operators to instantly create maintenance Dispatches when encountering issues. This eliminates the need to physically locate maintenance personnel, leading to faster downtime resolution.
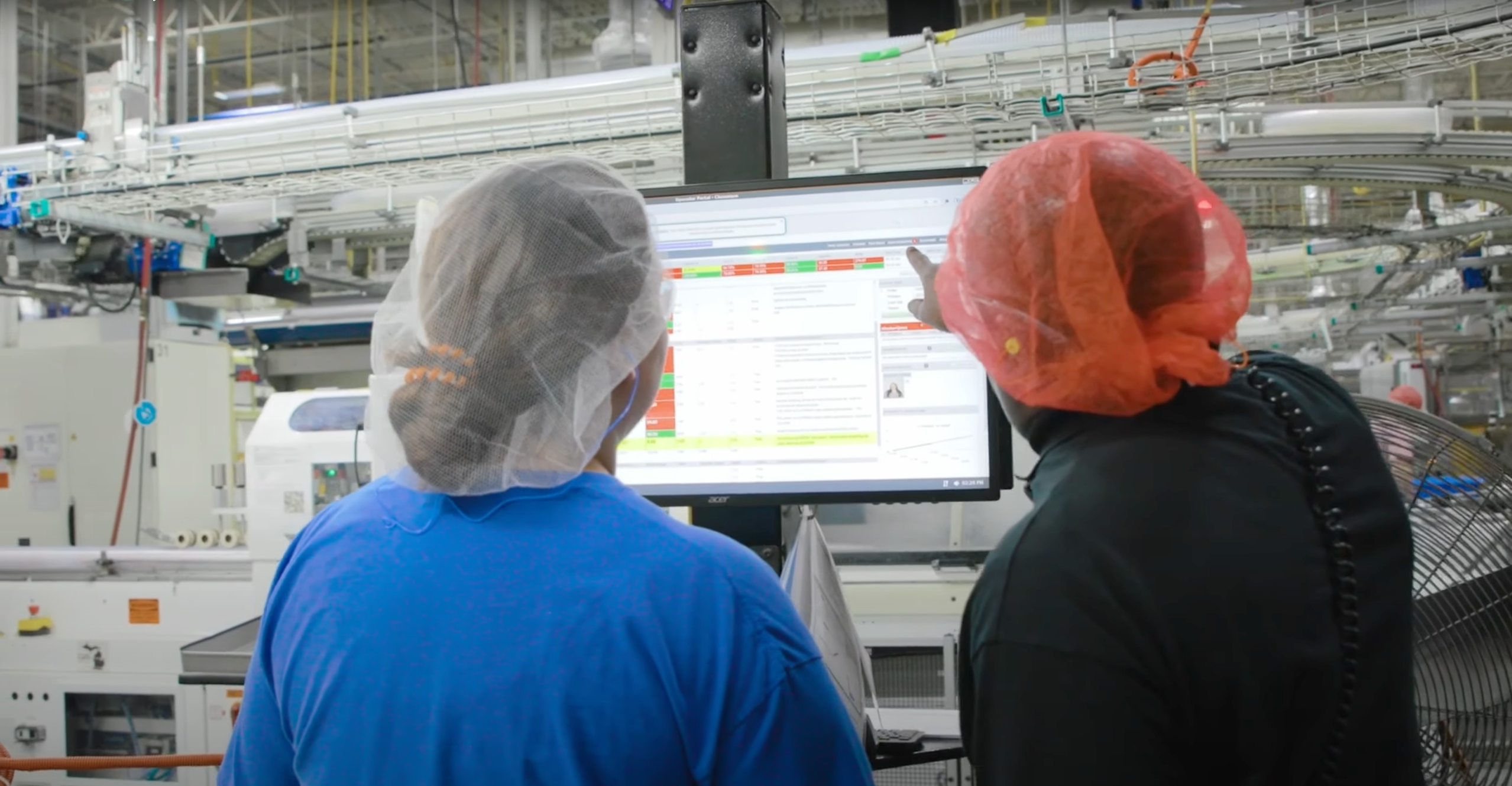
Before

Teams operated in silos with fragmented communication systems, causing delays in addressing equipment malfunctions and quality issues.
Now
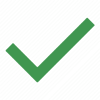
Maintenance teams receive detailed information before arriving at the location, allowing them to prepare the necessary tools and parts in advance. The result? Much faster response times.

From a maintenance standpoint, we are connected to everything on the production side now. We have a lot of information at our fingertips, and it makes us more productive in the things that we do.
Data-driven decision-making
With comprehensive data analytics, operators and managers can compare current performance against historical data to identify patterns and process optimization opportunities.
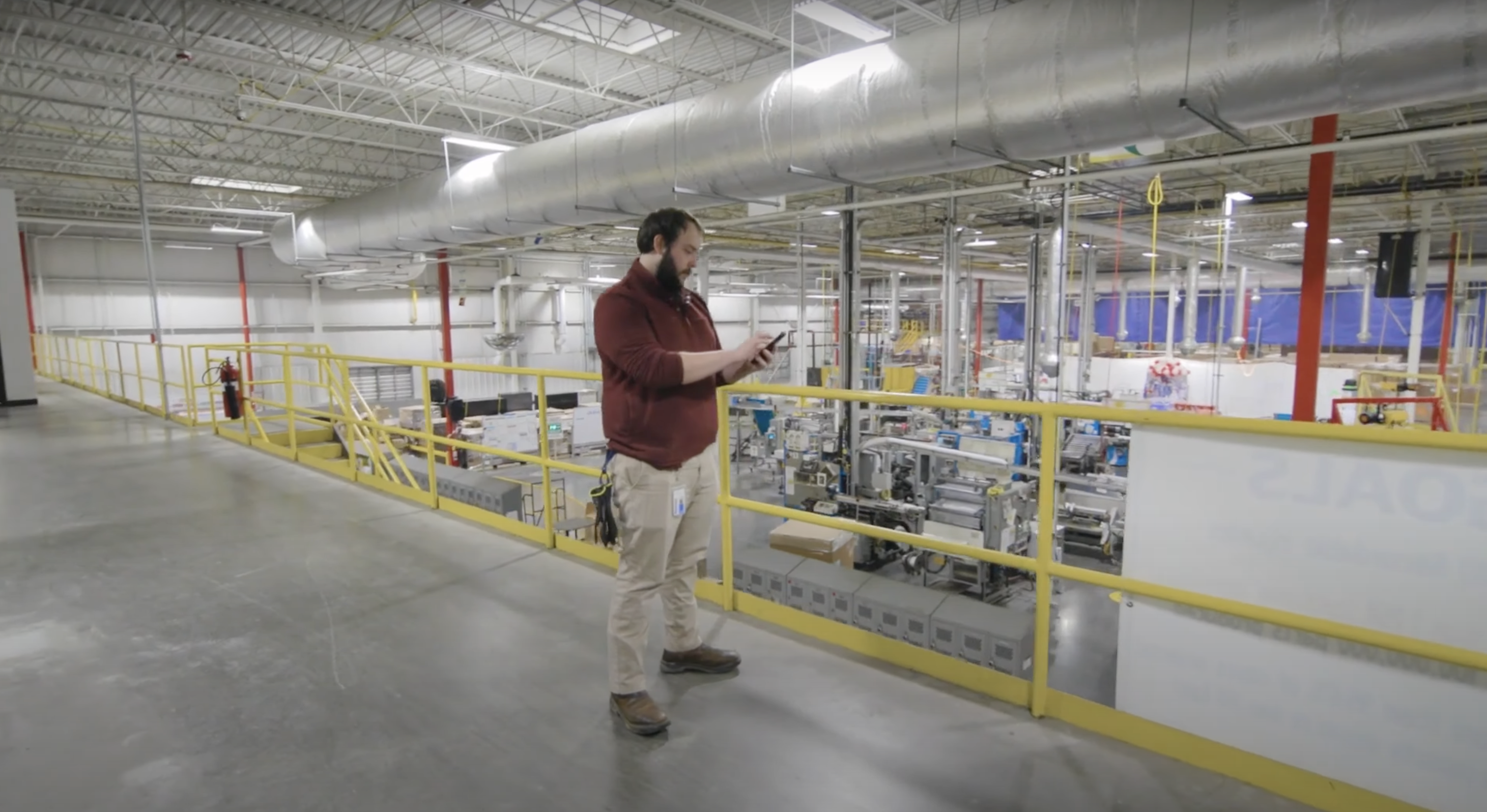
Before

Limited visibility into performance trends made it difficult to identify bottlenecks and improvement opportunities.
Now
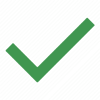
Staff can access and analyze data from days to months prior, enabling proactive rather than reactive operations and driving a culture of continuous improvement.

We've hit some of the highest production numbers this year that we've ever seen since the incorporation of L2L.
The return on investment
Efficiency ↑
Double-digit percentage increases in efficiency
Record-breaking production
Record-breaking production numbers since the implementation of L2L
Downtime ↓
Collaboration ↑
Proactive Maintenance
Culture shift
The solution that shows your manufacturing problems—and fixes them too
Drive continuous improvement in availability, performance, quality, and workforce enablement.
Quickly identify problems and take action faster with L2L. Empower your teams to achieve daily wins and drive success every day.
Trusted by leading sites around the globe.