Autoliv Transforms Global Manufacturing Operations
Autoliv is a global leader in automotive safety systems.
With L2L, Autoliv has:
-> Reduced equipment review time to minutes
-> Improved technician accountability and tracking
-> Enhanced data collection for problem-solving
-> Streamlined communication across departments
.png)
Actionable data
"If we have downtime on a machine, it's really easy for us to understand where that downtime was, who worked on it, what model we were running, what they did to fix it, and when it was back up and running. If we can't solve problems, we can't improve, and if we don't improve, we may not exist in the future."
- Valerie Held, APS Coordinator
Data collection and equipment review
Using L2L, Autoliv transformed how it tracks and reviews equipment maintenance data.
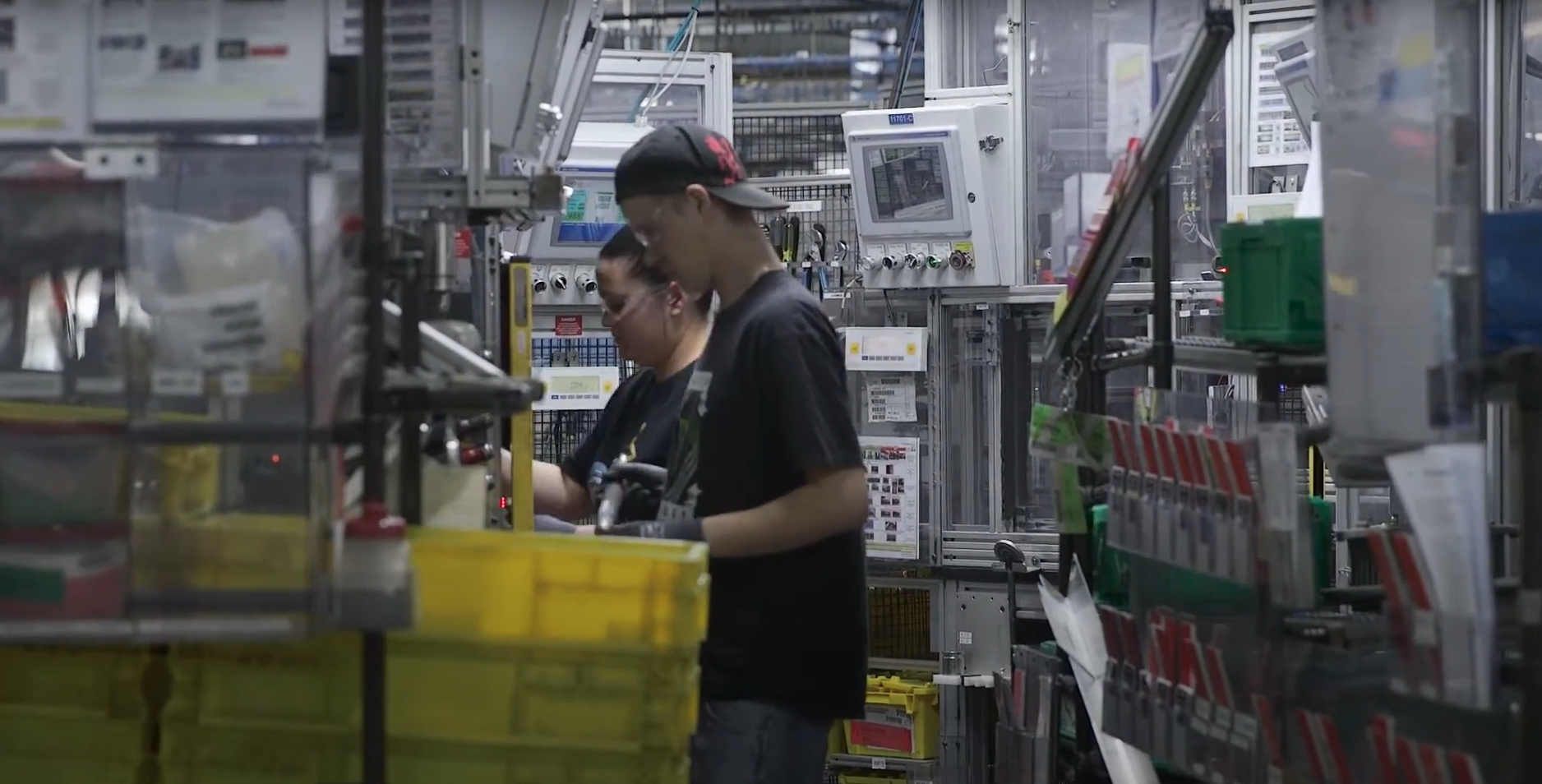
Before

The company relied on "red book" binders with handwritten maintenance logs stored with each machine. Reviewing the maintenance history and status of their thousands of equipment pieces took an entire day, with fragmented and inconsistent documentation.
Now
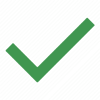

The system that we have now, with L2L, I can accomplish reviewing all of my equipment within a matter of minutes.
Resource accountability and allocation
L2L created visibility into maintenance resource utilization and effectiveness.
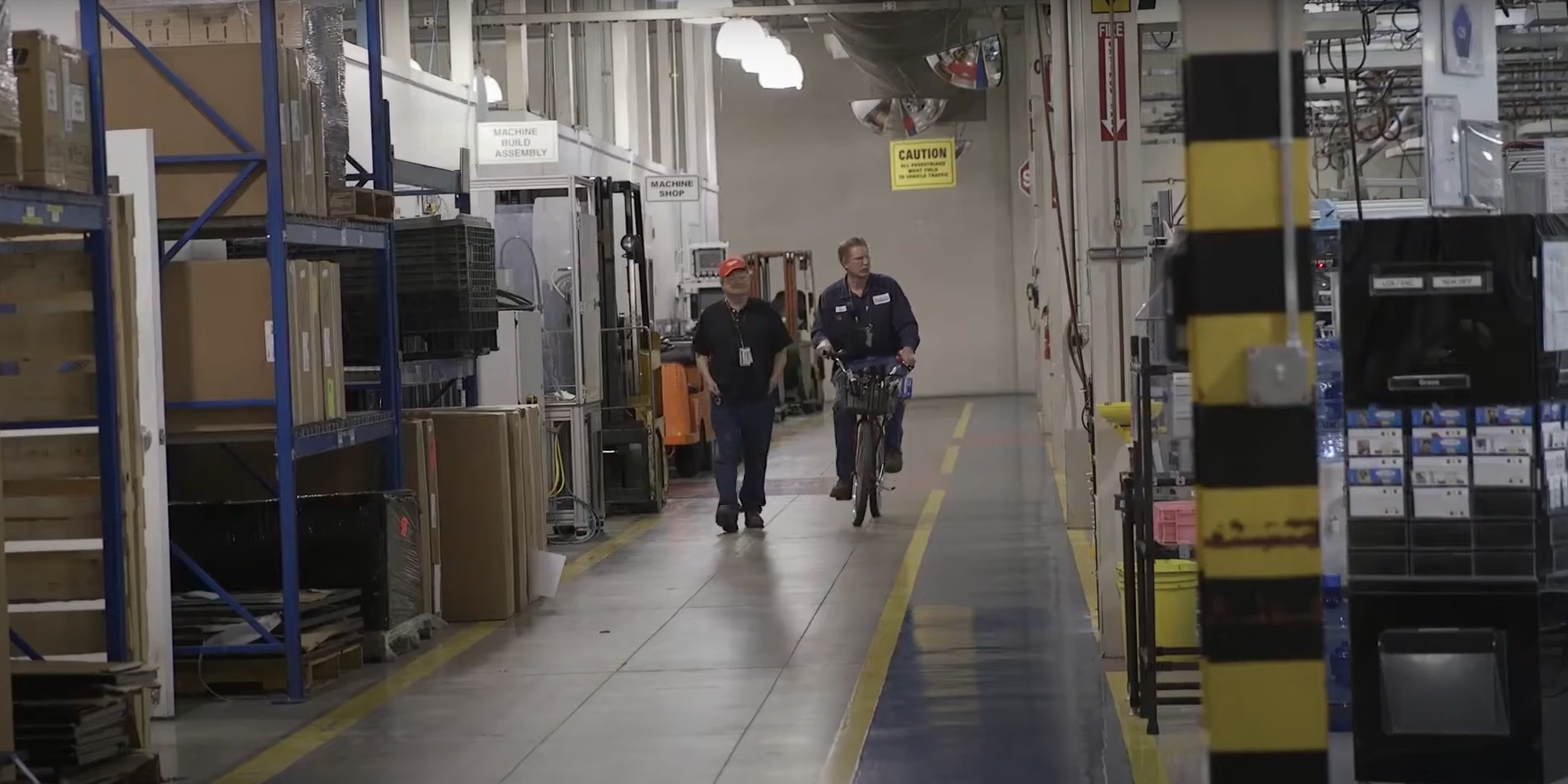
Before

Managers had limited insight into technician activities and productivity. It was difficult to track who was working on what equipment and for how long, resulting in inefficient resource allocation and potential accountability issues.
Now
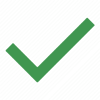
L2L tracks technician activities in real-time, showing exactly where resources are allocated. Management can easily generate reports showing technician productivity and accountability. The data helps optimize staffing and assignment decisions.

L2L holds people accountable. I can actually pull reports that look at how much they've been busy during the day. It's very important for us to understand on maintenance side.
Production impact tracking
L2L provides tools to identify and address production-impacting events.
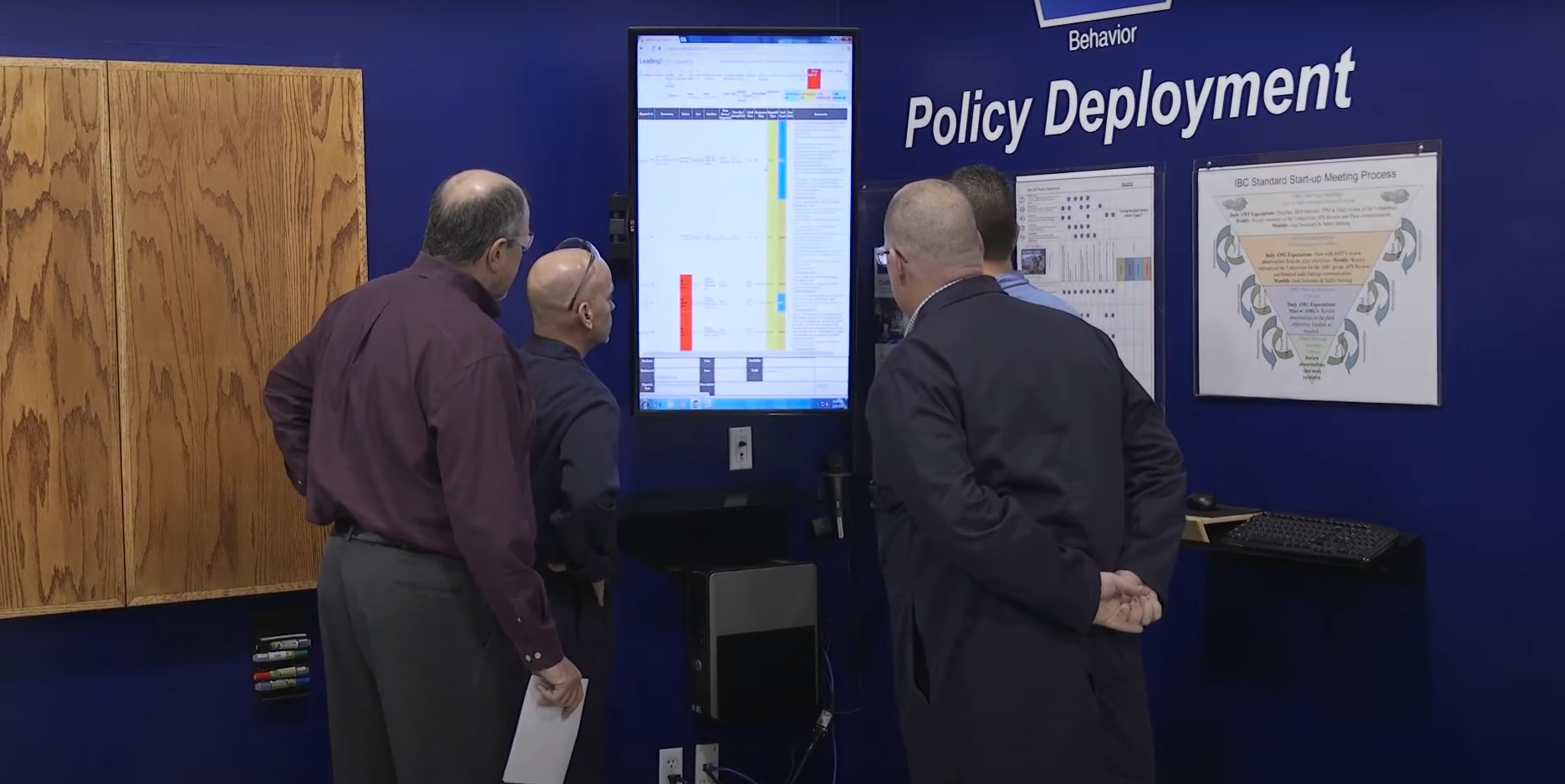
Before

Production issues were often poorly documented, making it difficult to identify recurring problems or patterns. Material shortages and other abnormalities would frequently impact production lines before they were addressed.
Now
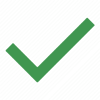
Any situation that impacts production is recorded in L2L. The system can identify trends in downtime situations and detect when equipment is starting to deteriorate. The team can now identify material shortages before they impact production lines.

Anytime there is a situation on the floor that impacts production, we want to record that, and this is the system that we use to record that. We can trend downtime situations, we can trend when something's starting to go bad.
Cross-departmental problem-solving
L2L transforms how departments at Autoliv collaborate to address issues.
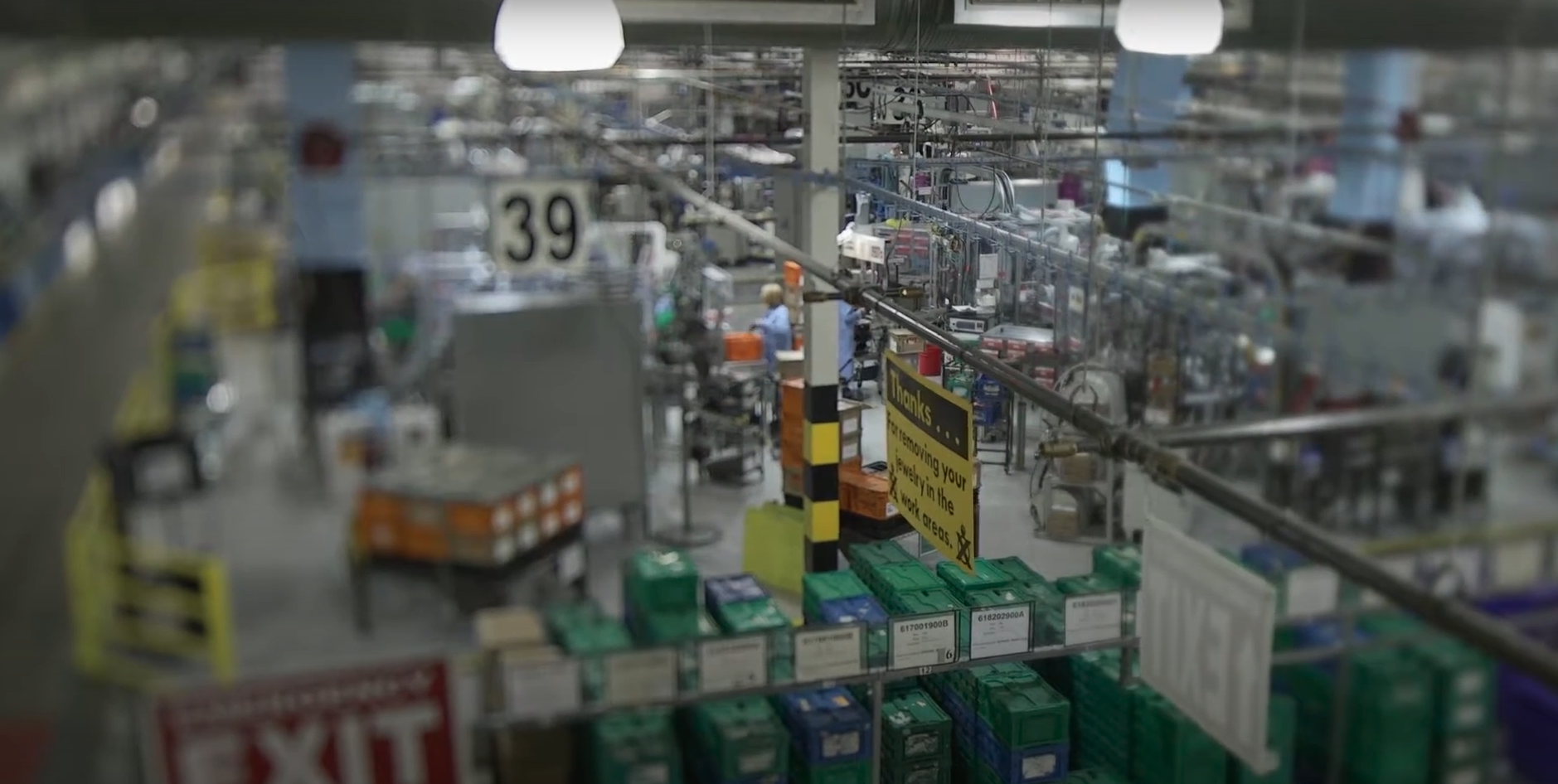
Before

Siloed information and disconnected problem-solving approaches made departmental problem-solving a challenge. Hot-shot calls, missed shipments, and expedited materials were difficult to track consistently across functions.
Now
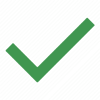
Multiple departments—Maintenance, Production Control, Quality, and Production—use the same system to track abnormalities. This creates a unified view of issues and enables collaborative problem-solving that wasn't possible before.

They can use it in any department. The quality department can use it, production control can use it, [along with] production and the maintenance world. L2L makes your job easier.
The return on investment
Review time ↓
Equipment review time reduced from a full day to minutes
Easy to access information
Elimination of paper-based processes
Continuous improvement
Communication ↑
Better ways of working
Reduced material shortages and expedited shipments
Equipment failure prevention
Early identification of potential equipment failures
The solution that shows your manufacturing problems—and fixes them too
Drive continuous improvement in availability, performance, quality, and workforce enablement.
Quickly identify problems and take action faster with L2L. Empower your teams to achieve daily wins and drive success every day.
Trusted by leading sites around the globe.