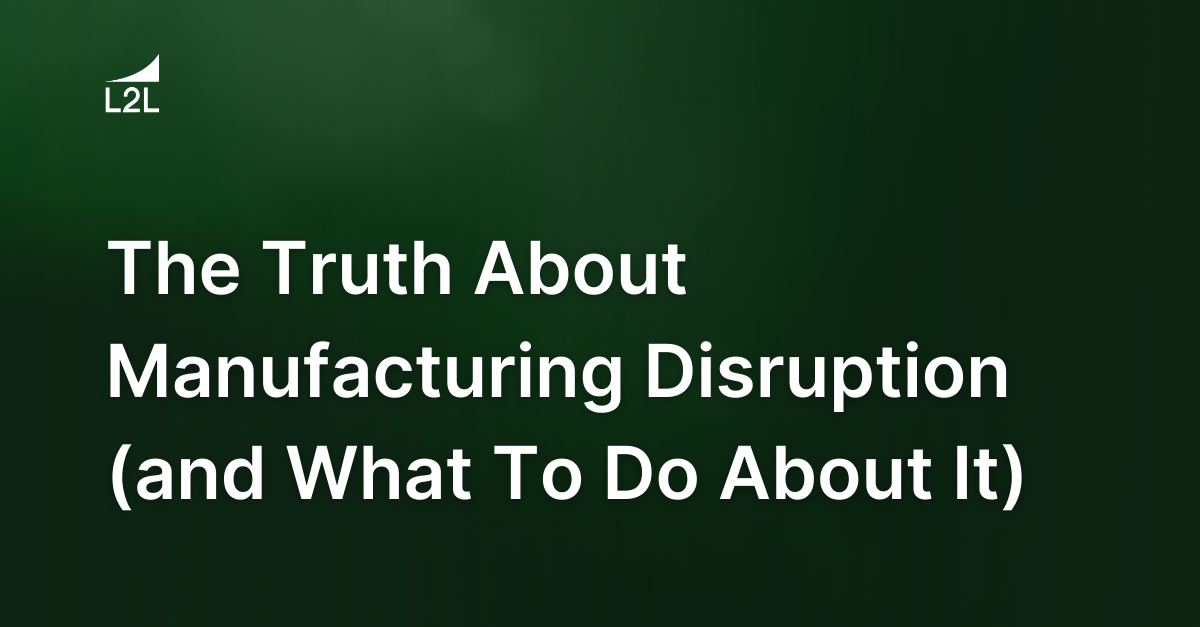
Estimated read time: 7 minutes
It’s probably safe to say production disruption is every manufacturer’s worst nightmare. We work hard to avoid it by analyzing risk, managing supply chains and doing exactly what we’re supposed to do — yet, somehow, disruption shows its ugly face anyway.
The truth about production disruption is that it’s inevitable.
As manufacturers, there are some things we’ll never be able to control. Machines will always go down, technology will always throw new curveballs, stakeholders across the supply chain will always have challenges of their own — the list goes on. Luckily, these uncontrollable elements don’t have to be world-shattering.
By identifying and addressing controllable disruptors, the manufacturing industry can better handle everything else. Basically, it’s a case of “pick your battles,” and today, we’re here to help you pick the right ones.
Will disruption define the decade?
If production disruption is really a manufacturer’s worst nightmare, then it’s a nightmare we’ve been collectively having since the beginning of the manufacturing industry itself. The concept of process interruption is nothing novel — it’s just wearing new hats.
For an example of one such hat, look no further than COVID-19. The pandemic introduced all kinds of new disruptors to the manufacturing landscape, from worldwide quarantines to supply chain issues. It started the decade with a bang — and what could have been the next Roaring Twenties quickly became the Disrupted Twenties. So, will disruption continue to define the decade?
We’re pretty sure the answer is yes.
At this point, the shockwaves caused by COVID-19 have permanently reshaped the way we view global supply chain management, risk assessment and the manufacturing sector overall. There’s even been a shift in preventive maintenance — because if you wait until a machine breaks down to order a necessary part, you could be waiting weeks or even months to get back on track. Efficiency-boosting solutions like smart manufacturing are more important than ever, while outdated approaches like spreadsheets and manual data entry are looking especially archaic. In short, large-scale disruption has changed us forever.
The good news is that the manufacturing industry has a long history of surviving tough situations. We can use production disruption as an opportunity to get stronger — but only if we approach it in the right way.
Why you need to determine your manufacturing disruptors
The key to riding the waves of disruption is to focus on the right details. If you get bogged down by things outside your influence, you’ll waste time and resources chasing those two birds in the bush while you totally neglect the one in your hand. Simply put, the best way to prepare for things you can’t control is to get better at identifying and preventing the disruptors you can.
Luckily, there’s a lot more in the latter category than you might have realized.
Take, for example, one of our favorite stats here at L2L: More than 65% of processes on the shop floor are non-machine related, and all of those processes experience disruptions. When we think of downtime, we typically think of machine breakdowns, but the rest of the non-machine-related disruptions are oftentimes wreaking as much or more of the havoc on your production throughput. And these tend to fly under the manufacturer’s radar while they erode throughput and profits. That means there are all kinds of production disruptions just waiting for you to catch red-handed.
The first step is to determine what your manufacturing disruptors are so you can focus on the right ones. This process begins by making sure you’re measuring the right things in your plant, and it ends with benefits like these:
-
Less wasted time: Although identifying and addressing disruption takes patience, it leads to less wasted time in the end. That’s because you’ll already know where to focus your efforts and when to admit a particular element is beyond your influence.
-
Added flexibility: When uncontrollable production disruption does happen, and it will, you need breathing room. You create that breathing room by quickly, efficiently and effectively handling other issues on the plant floor, giving you the flexibility to problem-solve when something unexpected happens.
-
Improved resilience: Say the supply chain experiences another pandemic-level disruption, and suddenly it’s near-impossible to get raw material. Once you get your hands on the necessities, it’s vital to be sure you’re capitalizing on that investment. Lucky for you, focusing on the right disruptors means you’ll be able to eliminate inefficiencies and get the most out of those hard-to-find materials.
Around here, that’s what we call “becoming disruption-proof,” and it will save time, money, energy and a whole lot of stress for the entire manufacturing industry.
Becoming disruption-proof
So, now you know why it’s important to define production disruption in your manufacturing organization — but how do you actually become disruption-proof?
It all starts with data.
There’s no way to identify production disruption without first gathering information about what’s really going on in your manufacturing company. If a machine even thinks about breaking down, you need to know about it.
As you gather this data, you’ll start to build a complete picture of your plant from the inside out, like assembling a puzzle one piece at a time. You’ll know how things look when they’re working right so you can quickly and easily identify when something goes wrong. Better yet, you’ll have a top-down view of the whole operation, which means you can catch disruption patterns and deploy solutions that target the source instead of the symptoms.
To do all this, you need a connected workforce platform to unite data from all sources and locations. With all the information in one place, you’ll be able to:
-
Utilize raw materials more effectively.
-
Make better, more efficient decisions.
-
Navigate supply chain challenges outside your control.
-
Deploy risk management techniques.
-
Overcome production disruption, both machine-based and non-machine-based.
A connected workforce platform is your first step toward becoming disruption-proof. It’s up to you to take that step.
Where to start
If you’re tired of suffering through the production disruption nightmare, you’re not alone. Although these disruptors are our constant companions, some of them are well within your control — all you have to do is figure out how to tell them apart.
A connected workforce platform can help you gather the data necessary to do just that, but there’s always more to the story. For example, how can you turn that data into insights? And at what point do those insights stand up and say, “Focus on this instead of that”?
Don’t panic — we have the answer for that, too. Check out our platform overview video to see how you can know which disruptors deserve your time and effort.
Revisions
Original version: 18 July 2024
Written by: Evelyn DuJack
Reviewed by: Daan Assen
Please read our editorial process for more information
Subscribe to Our Blog
We won't spam you, we promise. Only informative stuff about manufacturing, that's all.