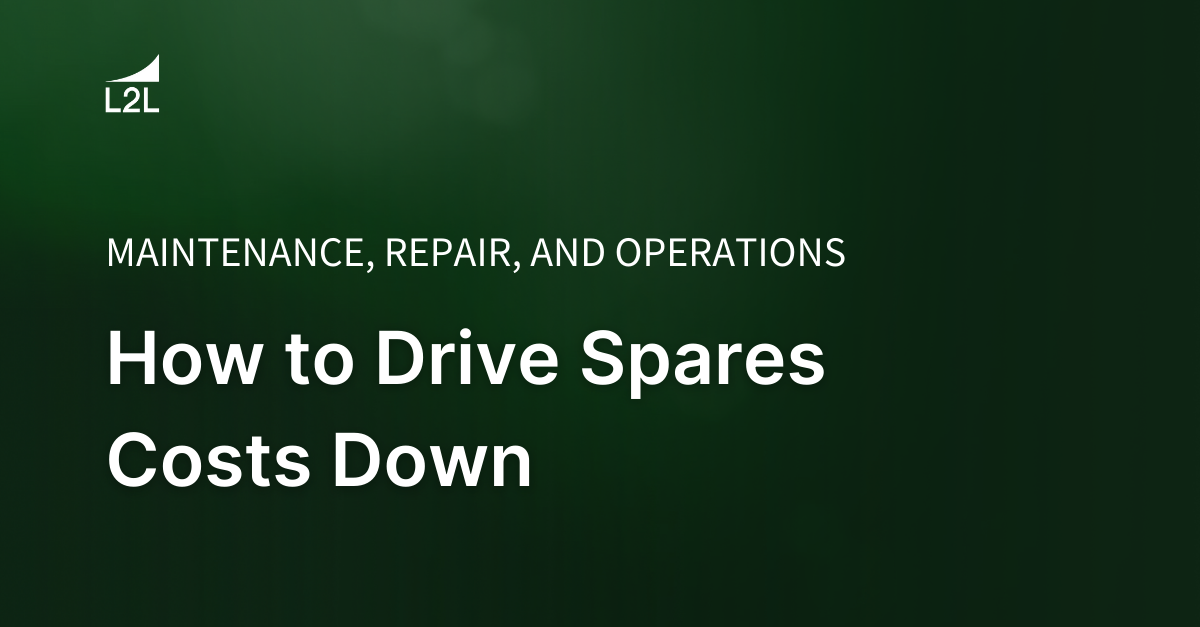
Maintenance managers are being challenged to reduce inventory costs while also maintaining and improving the reliability of equipment.
These two objectives may seem at odds with each other, but they don't have to be. In this blog, we'll show you how.
What Maintenance, Repair, and Operations (MRO) Needs to Understand About Reliability
Improving machine reliability reduces the need to stock large quantities of spare parts and will help you predict your min/max inventory levels for maintenance, repair, and operations managers.
For example, a sensor gets damaged on a production line conveyor, so a technician pulls a new sensor from spares inventory and installs it on the conveyor. Problem solved, right?
Not necessarily. A sensor should never be damaged, it should only wear out. There has to be a reason why the sensor was damaged so the first thing a technician should do is find out the cause. This may seem obvious, but a lot of times the tech is in a hurry to restore the line and isn't able (or take the time) to identify the root cause of the issue.
In that moment, there are two possible sources of information about this issue.
-
First, the operators may have insight into what happened (if they stuck around)
-
And second, machine history (if you have it in a system and have access to the data while at the scene of the crime)
From The Point of View of a Maintenance, Repair, and Operations Leader
Theresa Alvarado, a maintenance, repair, and operations supervisor for a major food packaging producer recently told me, "Real-time visibility in the hands (mobile devices) of mechanics is crucial for them to make better decisions based on what spare parts have been used on a piece of equipment recently."
I agree 100% with Theresa. If the tech can see whether the machine has already been called down in the recent past for the same issue, it's a clue that there's an underlying problem that needs to be resolved. Otherwise, it will just happen again, blowing through more of your spares inventory.
Real-Time Data Drives Reliability and Improves Maintenance, Repair, and Operations
Having this type of real-time history for the equipment allows you to see patterns, like a part being replaced more frequently than it used to be. This kind of information at the fingertips of the technician, while they're on the line looking at the problem, may also bring to light improvement ideas to eliminate the cause of downtime. For example, they could add a follow-up work order (improvement idea) to place a guard over the sensor, or make it non-adjustable so it won't get hit by moving conveyor pallets again.
Having the right real-time data is critical to your overall maintenance, repair, and operations targets. Also, teaching the technician to ask why a part is malfunctioning instead of just replacing it will build the continuous improvement culture you need to improve your machine reliability.
Maintenance, Repair, and Operations Needs an Easy Way to Communicate with Technicians
Alvarado also observed: "Our mechanics have an easy way to communicate what they need, and we can supply them with the needed parts. This helps keep our inventory more accurate because it's easy for them to request spare parts."
By simply having real-time visibility of machine and spare parts consumption history, your maintenance, repair, and operations will improve through:
-
Improved MTBF (Mean Time Between Failure)
-
Better ideas submitted for improvement projects
-
Spares inventories are set to the right min/max levels (which in turn reduces costs)
-
Happy technicians that have the tools (data and devices) needed to succeed
-
Satisfied "customers" in operations
The result will be both improved machine reliability and lower cost of inventory. Everybody wins!
Ready to improve reliability and reduce spares inventory costs? Find out how L2L's CloudDISPATCH can help you improve your maintenance, repair, and operations.
Schedule a demo today!
Revisions
Original version: 18 July 2024
Written by: Evelyn DuJack
Reviewed by: Daan Assen
Please read our editorial process for more information
Subscribe to Our Blog
We won't spam you, we promise. Only informative stuff about manufacturing, that's all.