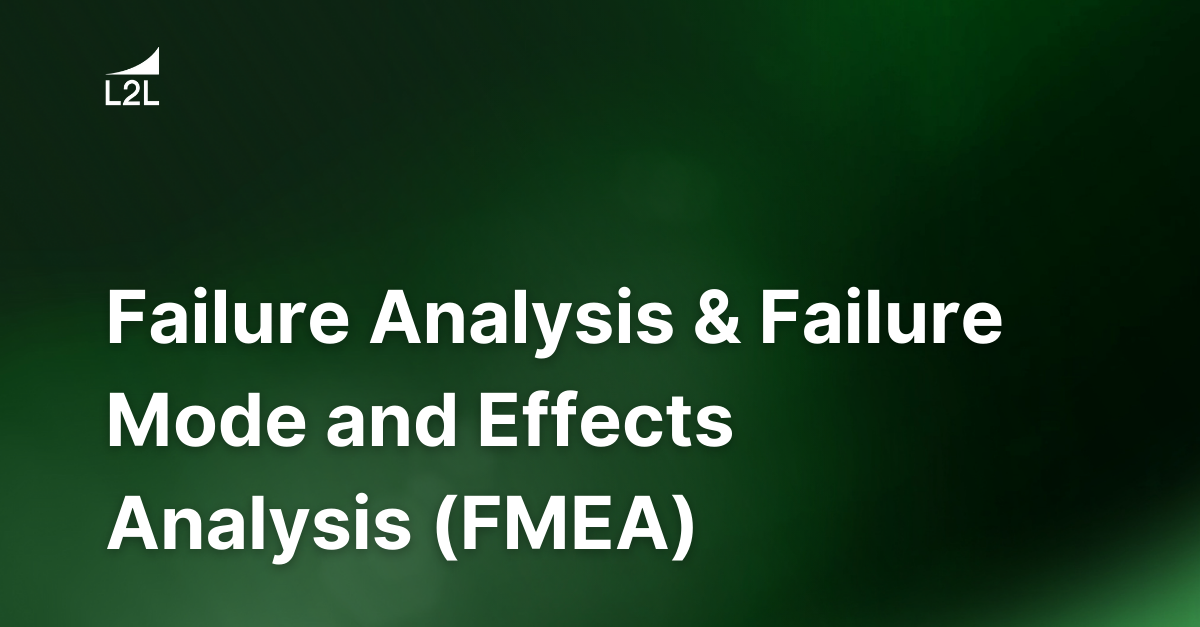
One of my all-time favorite topics is Failure Analysis. Who doesn't just love failure? And not just the failing part, which is always a good time. The opportunity to publicly dissect your failure and let everyone roll around in it with you. Just light some formaldehyde scented incense, and you're right back in high school again. All joking aside, this is a true story.
Failure Analysis. Not just any Failure Analysis. While my personal favorites are those that I used most frequently in manufacturing, failure analysis has applications and huge potential benefits for every industry and business.
Failure Mode and Effects Analysis (FMEA)
My favorite? Failure Mode and Effects Analysis, also known as FMEA. And not just because it's fun to say. Failure Analysis is potentially one of the most powerful tools you can use to guide improvements. FMEA has almost endless uses in manufacturing: from Process PFMEA, Product PFMEA, or even Design DFMEA. Ultimately, using this powerful and effective Quality Management Tool has nearly endless applications.
So how is Failure Analysis helpful in manufacturing? FMEA, or Failure Mode and Effects Analysis, is a great tool to identify failure modes, making problems objective rather than subjective. It's always better to remove emotion and finger pointing. Looking at failures from a frequency, severity, prevention, and detection point of view allows for analyzing the source, the underlying issues which resulted in failure.
FMEA can be used proactively from a Product and Process Design standpoint. This methodology is ideally suited for pre-production process and design, and presents tremendous opportunities for growth. We can gain the most from our mistakes, particularly when our response is to learn from them. Using FMEA in Product and Process Design to identify all potential failure modes prior to beginning full scale production allows for analysis of prior known failures. With good data in hand, design is approached strategically to prevent recurrence of those previous failures. The ultimate goal is to implement proven elements and poke yoke design and production methods and processes going forward, proactively eliminating resurfacing of previous failures.
Use Failure Analysis to Fully Understand the Problem
FMEA analysis can be an immensely powerful tool to use in manufacturing. I have found one of the most important parts of any problem solving exercise is to fully understand the problem. Fully understanding the problem is half the battle in problem solving. Capturing and understanding all event specifics such as Shift, Time, Product, Changeover, Machine Issue, etc., will lay out the evidence trail and recipe that will allow your team to recreate these problems that plague us.
If we learn the event specifics and the recipe to problems, we can ultimately eliminate these problems from future recurrence. So many times, we use poor or small sample sizes of data and knee jerk reactions to these issues without fully understanding the true root of the problem. Many of the problems we fix today may not be the highest priority or have the best return on investment. However, they are the ones with high emotion or the most vocalized (i.e., get yelled about the most).
Trust your data and use good Pareto Analysis Tools to objectively identify your most significant problems. The increasingly digital time we are in comes with many advantages. We have endless supplies of great data when using an LES like Leading2lean (L2L). Finding data and problems to work on may not be the problem. Determining the right problem to address first to eliminate recurrence of a given failure is the immediate goal of any fruitful Failure Analysis.
Use Data to Know the Root Cause
A logical, easy place to start when using the FMEA approach is to compile your data so you understand the true Occurrence Rates of any repeating Failure Mode. That's the surest way to know you are focusing on the biggest offenders in terms of recurring problems. To ensure that you have accurate and sufficient data, so that you know with certainty the true Occurrence Rates of those most frequently occurring Failure Modes, requires constant access to accurate and transparent information. A reliable means to always have good data immediately available in order to calculate these occurrences. Having a great Lean Execution System (LES) like L2L, provides you with a very objective, precise instrument with which to obtain this data.
Having accurate historical occurrence information is critical and must be consistently repeatable without exception. Using your Dispatch History and other reporting functions to determine the total number of events will provide valuable information regarding the frequency and recurrence likelihood of a failure event. This Dispatch History is not only critical to determine frequency: this information and documentation are providing a wealth of empirical information. Data and history do not lie. This information is gold and is vital to help identify Root Cause. Great data and documentation are key to FMEA.
When you utilize your LES data and listen to the story it is telling, you can begin to uncover the hidden layers behind that mask - the Root Cause. By simply documenting and utilizing an Event Management System like Leading2Lean, you will immediately begin to build the History and event specifics, the recipe, that maps out the evidence trail to help identify and eliminate future occurrences.
Detecting Failures
Another great attribute of FMEA is understanding the detection side of any problem or anomaly. If your process can create a failure, how well can it detect the anomaly? Many manufacturing sites focus on the detection side of problems or anomalies. Many fully understand and accept the likelihood of creating a problem or anomaly. However, I would suggest putting your efforts into working towards an emphasis on the detection side of the problem.
Ideally, we manufacture products with an emphasis on the prevention side of problems. In reality, many sites are forced to accept the probability and likelihood of manufacturing defects, and therefore focus on the detection side of identifying the defects or problems they create. In some instances, detection may be the primary method to identify problems or anomalies. On these occasions, a stable process and rigorously tested measuring devices are invaluable to maintain a level of confidence in capability.
When utilizing detection as your only method to eliminate sending problems or failures to a customer, it is imperative you have an adequate measuring device. How reliable is your measuring device? Is your measuring device capable? When was the last time you measured your measuring device? These are all great questions to an unfavorable or less than ideal process! Even if you are running with a less than ideal process, wouldn't it be great to have all these answers to your less than desirable conditions?
Close the Loop on Failures with L2L
You can greatly improve your capabilities and close the loop on many difficult and less than ideal processes with an LES System like Leading2Lean. Utilizing the capabilities of a modern LES system allows users to connect processes, transfer information, and close the loop on many processes and designs that are susceptible to failure. Whether you are measuring number of occurrences, trying to prevent or detect problems in your process or design, Leading2Lean can significantly improve your likelihood for success and close the loop on many common pitfalls that plague manufacturing sites around the world.
Revisions
Original version: 18 July 2024
Written by: Evelyn DuJack
Reviewed by: Daan Assen
Please read our editorial process for more information
Related Posts
Subscribe to Our Blog
We won't spam you, we promise. Only informative stuff about manufacturing, that's all.