
The Perfect
MES System Guide
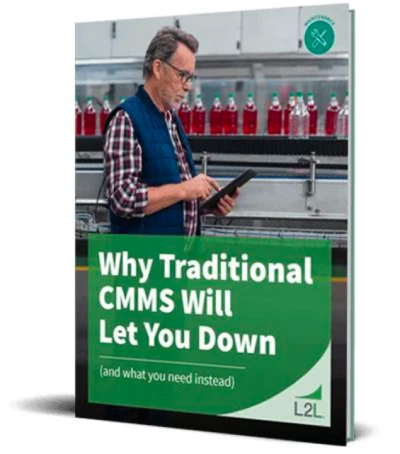
Ready to Get Started? Request a Free Consultation.
MES stands for manufacturing execution system. It’s software that brings together lean transformation, shop floor automation, machine connectivity, and more — all to help manufacturers track, control and document the production process from raw materials to finished goods. The ability to manage these processes can greatly improve operational performance on the plant floor.
For most manufacturers, the MES journey has lasted over 20 years. Many companies started with big ideas for MES, believing that it was going to revolutionize their plants to provide more automation and visibility. To guide these ideas on the shop floor and throughout the supply chain, the Manufacturing Enterprise Solutions Association (MESA) attempted to define MES by listing 11 functions of an MES. In 2000, it merged with the Purdue Reference Model to form the ANSI/ISA-95 standard.
The model spans many functions, and this is perhaps where MES is set up to fail. While MES can help improve OEE, it is not the "silver bullet" that was promised from the start.
Luckily, there may be a simpler approach to getting the majority of MES benefits without the cost and complexity of a full-blown MES implementation.
At a high level, MES benefits deliver on three core elements:
-
Product traceability ("Track and Trace")
-
Recipe management
-
Machine process control
You can also expect the occasional benefit from MES in these areas:
-
Labor management
-
Regulatory compliance
-
Supply chain visibility
-
Logistics scheduling and planning
There are many different kinds of software and systems that integrate with a manufacturing execution system. Some are comparable but not synonymous with MES. These include:
-
Computerized Maintenance Management System (CMMS)
-
Enterprise Resource Planning (ERP)
-
Manufacturing Operations Management (MOM)
-
Manufacturing Resource Planning/Material Resource Planning (MRP)
-
Enterprise Asset Management (EAM)
-
Statistical Process Control (SPC)
MES capabilities can be very valuable, especially if you’re in a highly regulated industry where the risk of production process error can be costly or catastrophic to your business.
Many companies don't have machines with programmable logic controllers (PLCs), or they use paper to manage recipes, tracing, and other shop floor processes. If any of this sounds familiar, you’ve got a lot of work to do before MES software can create real benefits. You want to evolve your manufacturing operation into a digital factory, but you don't want to spend years and millions of dollars on a complex MES — and you’re not alone.
Unfortunately, integrating is also no easy task. The complexity of PLC programming (both from the machine-level instruction and in terms of the skill required by engineering staff) has set a very high threshold that many manufacturers haven’t overcome. Time and money constraints have made it next to impossible.
MES focuses solely on the equipment and assumes that all manufacturing execution problems can be solved through sensors and PLC software. Yes, this is a factor — but in reality, it only accounts for a portion of the operational availability (OA) gap in manufacturing. It neglects to incorporate other critical abnormality management elements, such as:
-
Material issues: A glaring gap in MES is the ability to track material issues — ordering, material shortages, and inventory management — in your production process.
-
Training issues: Unlike a cloud-based system, MES systems can’t track employee skills training and certifications.
-
Quality problems: MES software can help manage production but does not have the capability to track and monitor quality assurance.
-
Audits: Unlike a complete manufacturing system, MES does not track records and necessary information for audits.
-
Total Productive Maintenance: This element, also known as Total Preventive Maintenance, goes untracked by MES. That’s because MES software can’t monitor your entire maintenance system.
-
Additional areas: There are plenty more opportunities for issues to arise, such as 5S, product changeovers, trial management, product verification runs, and cleaning procedures — all neglected by MES systems.
In theory, an MES platform defines capabilities for managing every element of the shop floor. Unfortunately, it's fallen short.
We've been told that MES can do it all. With enough time and money, it probably could. Of course, we've never come across a plant with unlimited resources.
In addition, due to the climate of global competition, manufacturers have been forced to narrow the MES scope because most implementations have taken many years and millions of dollars. In cases where they eventually do pull the trigger, they typically have portions implemented on the machine side; unfortunately, the scope has been narrowed so much that they resort back to manual methods for many execution processes.
If you’re still thinking about purchasing MES software, review these points first:
-
In our digital age, committing to anything that takes 2–3 years to implement is sure to put you behind the times before you even finish the project.
-
Companies are often being sold off and merged, and left with a myriad of different MES systems that present challenges, including the consistency of production data, process, and integration capability.
-
Many manufacturers are fed up with the seemingly never-ending journey toward digital transformation. They’re frustrated that the bill of goods they were sold never materialized.
Part of the complexity is often because many manufacturers have a growing list of stock-keeping units (SKUs) — all while IT staff numbers continue to dwindle. This creates a conflict between the ongoing support of MES and other competing IT projects. We’re not saying implementing MES can’t or shouldn't be done, but you should know what it will accomplish and what it won’t.
The PLC Problem
Historically, people who monitored shop floor processes and performed visual inspections to maintain production efficiency and quality also operated machinery. They identified the manual adjustments necessary to restore control in uncontrolled situations.
At the time, it was common to have multi-decade veteran employees who performed the same jobs their entire careers. In today’s environment, workers and jobs change with much greater frequency, making it difficult to maintain consistency in productivity and scrap control.
As manufacturing processes become more automated and sophisticated, it’s critical to remove variance and to mistake-proof processes. The goal is to increase productivity, reduce scrap and minimize wasteful overproduction. Optimization is accomplished by automatically adjusting for variations in product attributes and machine parameters, such as:
-
Dimension
-
Weight
-
Verification/inspection data
-
Machine settings
By building this functionality into the process, you create a standard to measure against. This helps you identify when the process has drifted out of normal operating conditions, allowing you to notify the operator that a problem has occurred.
Of course, many companies aren't in this boat. Some don’t have machines with PLCs, or primarily use hand tools for assembly. Others may have these things, but they currently use paper to manage items such as recipe and trace processes. These manufacturers don’t want to spend years and millions of dollars on a complex MES but still want to evolve into a digital factory.
Lack of Standardized Approach
An MES platform comes up short by only identifying and surfacing problems. What you need is a standardized approach that allows you to focus on systemic issues and resolve problems.
Often, there is no system in place to manage the follow-up and corrective actions; therefore, the ball is often dropped, and companies struggle to close the loop on common problems in their facilities. This puts an additional burden on your key resources, as they are constantly fighting recurring plant floor issues.
Real-world example: Cars are getting more and more sophisticated every day, but they still rely on the operator. The computer in the car can tell you that the air in your tires is low, but it can't tell you that the tires aren't wearing evenly because you have a bad shock. Often, trying to use sensors to capture everything is just not cost-effective. Trying to eliminate the driver from the equation at this point is all but impossible.
Minimal Impact on Problem-Solving
It’s important to know what your problems are. Many companies struggle with common problems like:
-
Raw material supply and deviation in quality
-
Poor visibility
-
Low expectations
There can be up to 200 processes and subprocesses in manufacturing, many of which are managed with manual methods such as paper, radios, and Post-it notes.
Utilizing processes and software to help bridge the gaps beyond machine control can deliver huge gains without breaking the bank. Maybe you need a full-blown MES system to make that happen and maybe you don’t.
Either way, the good news is you have options. Manufacturing is really about creating an efficient, consistent and repeatable process.
Successful companies can bridge a significant portion of that OA gap by focusing on abnormality management. “Abnormalities” are disruptions — and MES system alternatives like connected worker platforms are about eliminating these disruptions.
This means that, when a problem is likely to occur, these platforms implement a closed-loop digital system like L2L Dispatch to streamline and solve problems at all levels. (Plus, L2L Dispatch can integrate with every major MES solution on the market.)
MES vs. Connected Worker Platforms
There are four main aspects of the business that manufacturers have to deal with on the floor every day: man, materials, machine, and methods.
-
Man is the people — both the people who build the product and those who support them.
-
Materials are the components to make the product. Like it or not, your competitor is probably also buying from the same suppliers and paying the same prices you are.
-
Methods are how you manage the processes or workflows in the facility. This is where you gain a competitive edge: through the methods you choose to deploy or manage these four main aspects.
-
Machine is the fourth element. Of course, your competitors probably buy their machines from the same vendor at close to the same cost.
A connected worker platform brings all these elements together in ways that make sense. That means man, materials, methods, and machines are all on the same page and connected on the same platform — something MES software doesn't accomplish on its own.
When to Focus on an MES Solution
To achieve your objectives, you may still find it necessary to implement an MES solution. A wide array of companies are available to provide this service, but you may choose to build it yourself. It’s critical, however, to be clear on what you’ll be able to achieve with an MES.
When it comes to machines, a good MES solution controls equipment settings or parameters like fill rate and speed. Next, you need to include the material control aspect of MES, including the components to build the product and the traceability of their lot and/or serial numbers.
Once you’ve included all that, you’ll likely realize it's costly and time-consuming to build an MES system — especially if you want it to control the whole plant. However, sometimes they're required by your customers and needed for the traceability of the product.
When a Connected Worker Platform is What You Need
An MES can only notify you of problems related to machines. Our research has shown that these machine-related issues typically represent 35% or less of the total issues that occur on the plant floor.
Improvement lies beyond MES systems. That’s because the opportunity to solve the other 65% of your issues is not only critical but also extremely valuable.
For many manufacturers, deploying a connected worker platform first is the smartest move.
Connected worker platforms allow you to achieve production process and shop floor improvements by standardizing issue responses. Additionally, this software provides the continuous improvement foundation on which the MES can sit. Better yet, connected work extends MES capabilities for driving improvement. For example:
-
MES data and metrics can trigger processes outside of a machine.
-
Machine notifications will have a trackable and required action or response in order to close the loop on resolving the issue.
-
A data interface serves operators where no MES data is available.
-
Processes can launch across any part of the plant through the LES based on MES data.
The terms MES and MOM are often used interchangeably. While they’re similar concepts, they are not identical.
MOM stands for “Manufacturing Operations Management,” defined as a collection of systems for managing end-to-end manufacturing processes with a view to optimizing efficiency. MOM encompasses scheduling, dispatching, maintenance, skills management, and MES system functions. In contrast, a manufacturing execution system is simply one part of the solution and is rarely the all-encompassing software needed in your facility.
In simple terms, think of it this way: MES + Connected Worker Platform = Lean MOM. Combined, they offer a comprehensive solution for:
-
Machine issues related to track and trace, recipe management, process control, and more.
-
All of the human actions/responses to abnormalities happening every day on the plant floor.
The good news is that while you have problems every day that need to be solved, you also have the people to help solve those problems. Problems are equal opportunities — and opportunities are where you become more efficient.
The more quickly you can identify those problems (opportunities) and manage the necessary solutions, the more efficient you become and the more money you save.
That’s where L2L’s Connected Worker Platform comes in.
Simply put, this platform combines three things:
-
MES functionality
-
Computerized maintenance management system/enterprise asset management functionality
-
Connected worker philosophy and technology
It’s a pragmatic approach to digital transformation — one that makes you more efficient at a faster rate. Plus, it’s more budget-friendly than traditional approaches, especially traditional MES systems.
Here are just a few things it can do:
-
Identify the issues and roadblocks on the shop floor
-
Understand each problem you're facing
-
Prioritize those problems and opportunities using data instead of emotions
-
Put actions in place to solve the problem and manage the actions built around them
-
Measure the actions (review data) to ensure the problem has been solved (follow-up)
-
Share those lessons learned with other parts of your plants, or even throughout the company, to eliminate the possibility of repeat issues
Manufacturers are always looking to increase productivity. You can achieve this objective by consistently identifying and solving costly problems — and by managing the methods and people to build a continuous improvement culture. A connected worker platform makes it possible with a fraction of the time commitment and resources it takes to deploy and manage an MES implementation.
With an off-the-shelf connected worker platform like L2L, agility is becoming a cost-effective alternative. Unlike an MES, L2L can be deployed and run in your plant in as little as 4-6 weeks.
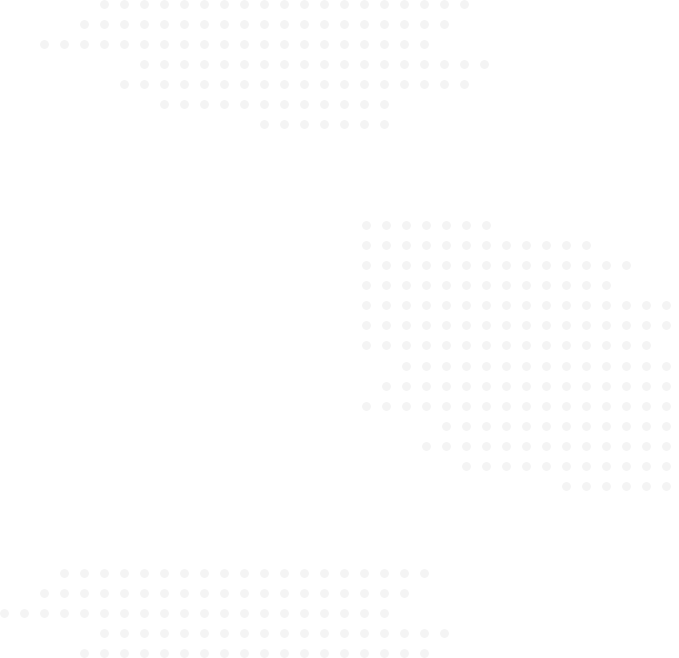
Change Your Culture
“We wanted to make information transparent at every level, and make everyone a problem solver. It’s how we’re going to operate all of our plants to a single standard going forward.”
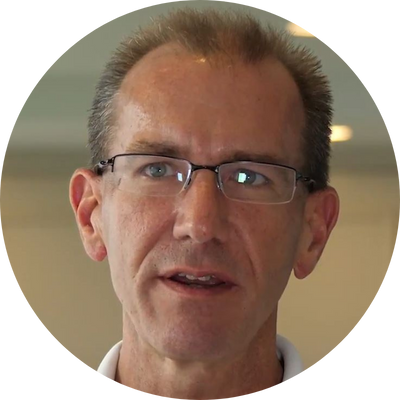